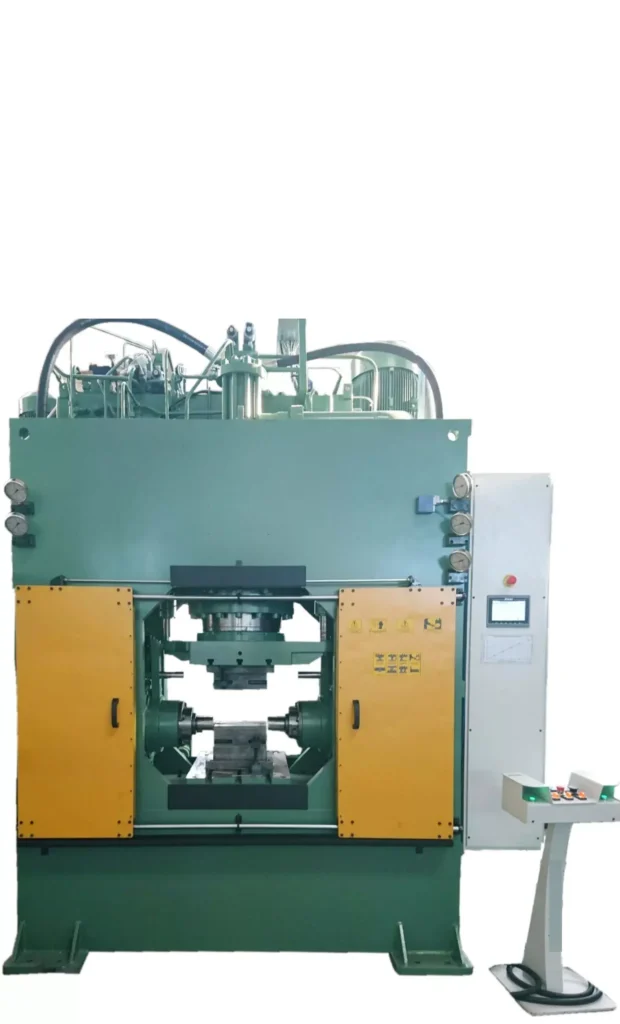
Hidroform Presi: Hidroform presi, inşaat sektöründe kullanılan bir tür hidrolik pres teknolojisidir. Beton blokların, tuğlaların ve benzeri yapı malzemelerinin yüksek basınç altında sıkıştırılarak kalıplara dökülmesini sağlar. Hidroform presleri, özellikle dayanıklı ve yüksek yoğunluklu yapı malzemeleri üretmek için tercih edilir. Bu sayede, binaların yapı taşı olarak kullanılan elemanlar çok daha sağlam ve uzun ömürlü hale gelir.
Hidroform Presinin Özellikleri ve Avantajları
- Yüksek Basınç ve Sıkıştırma Gücü: Hidroform presler, güçlü hidrolik sistemleri sayesinde çok yüksek basınç uygulayarak malzemeyi sıkıştırır. Bu, özellikle homojen ve yoğun yapı malzemeleri üretmek için idealdir.
- Dayanıklı ve Yüksek Yoğunluklu Ürünler: Sıkıştırma işlemi ile elde edilen yapı malzemeleri, normal presleme tekniklerine göre daha dayanıklı olur. Özellikle beton bloklar, bu yöntemle üretilirse basınca ve dış etkenlere karşı daha dirençli hale gelir.
- Enerji ve Malzeme Tasarrufu: Hidroform presler, istenen yoğunluk ve dayanıklılığı elde etmek için çok fazla ek katkı malzemesine ihtiyaç duymaz. Bu, enerji ve malzeme maliyetlerinde tasarruf sağlar.
- Esneklik ve Özelleştirilebilirlik: Hidroform presler, çeşitli boyutlarda ve şekillerde ürünler üretmeye imkan tanır. Bu da inşaat projelerinin gereksinimlerine göre özel yapı elemanları üretme avantajı sunar.
Kullanım Alanları
- Beton Blok Üretimi: Yüksek mukavemetli beton bloklar elde edilmesi için hidroform presleri sıkça kullanılır.
- Yapı Malzemeleri Üretimi: Binalarda kullanılan tuğla, parke, bordür gibi yapı elemanları da bu presler sayesinde üretilir.
- Modüler Yapı Elemanları: Özellikle modüler inşaat projelerinde, çeşitli şekil ve boyutlarda dayanıklı yapı elemanları üretiminde tercih edilir.
Hidroform Presi Seçiminde Dikkat Edilmesi Gerekenler
- Basınç Kapasitesi: Üretilecek malzemenin özelliklerine göre uygun basınç kapasitesine sahip bir pres seçilmelidir.
- Üretim Hızı: Seri üretim için uygun hızda çalışan makineler tercih edilmelidir.
- Enerji Tüketimi: Ekonomik bir işletim için enerji tüketimi düşük modeller tercih edilebilir.
- Kalıplama Esnekliği: Farklı kalıplarla uyumlu makineler, çeşitli yapı elemanları üretimine olanak tanır.
Hidroform presleri, yapı malzemesi üretiminde kullanılan verimli ve dayanıklı bir teknolojidir. Sağlam ve uzun ömürlü yapı elemanları üretmek isteyen firmalar için oldukça faydalı bir çözümdür.
Hidroform Presinin Özellikleri ve Avantajları
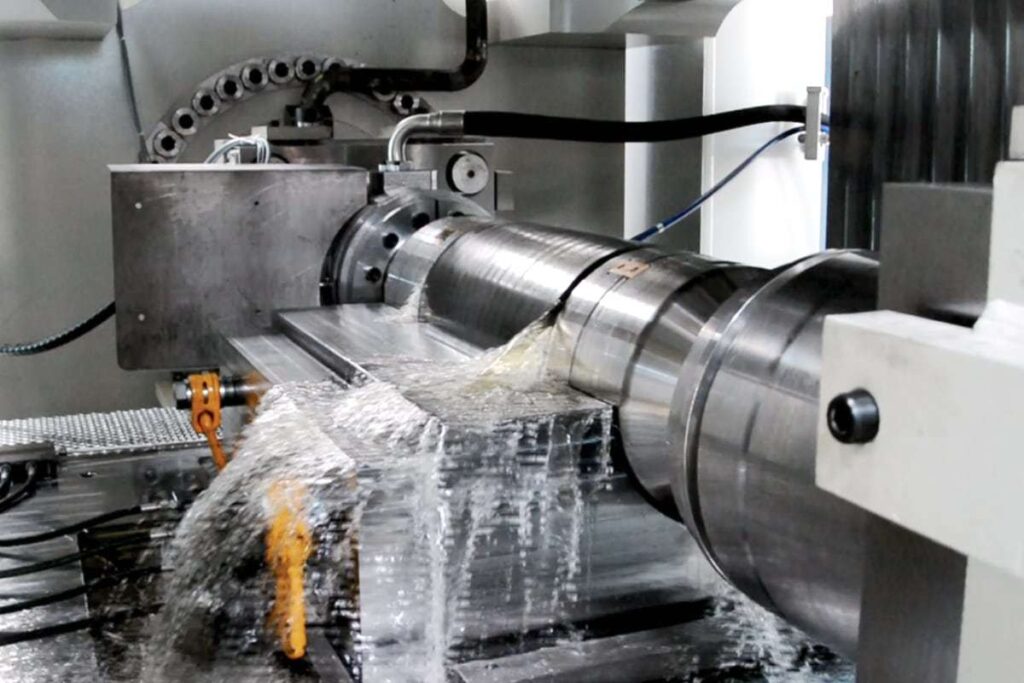
1. Giriş: Hidroform Pres Teknolojisi Nedir?
- Hidroform preslerinin tanımı: Temel işleyiş prensibi, hidrolik basınç kullanarak yapı malzemelerini sıkıştırmak.
- Kullanım alanları: Beton bloklar, tuğla, parke taşı gibi yapı elemanlarının üretiminde yaygın olarak kullanılması.
- İnşaat sektöründeki yeri: Dayanıklı ve yoğun yapı malzemelerine olan talep doğrultusunda artan önemi.
2. Hidroform Presinin Teknik Özellikleri
- Basınç Kapasitesi
- Yüksek hidrolik basınçla çalışan bu preslerin tipik basınç kapasitesi aralığı.
- Farklı yapı malzemeleri için gereken basınç değerleri.
- Kalıplama ve Şekillendirme Yeteneği
- Kalıpların değiştirilebilirliği ve özelleştirilebilir kalıp seçenekleri.
- Farklı boyut ve şekillerde ürün üretme imkanı.
- Malzeme Yoğunluğu ve Homojenlik
- Sıkıştırma işleminin malzemenin yoğunluğunu artırması.
- Ürünlerin homojen yapıda olması ve dayanıklılığı.
- Sıcaklık ve Isıl İşlem Uygulamaları
- Sıcaklık kontrol mekanizmaları ve gerektiğinde ısıl işlem uygulanabilmesi.
- Yüksek sıcaklıkta sıkıştırmanın malzemenin kalitesine etkisi.
3. Hidroform Presin Sağladığı Avantajlar
- Yüksek Dayanıklılık ve Mukavemet
- Yüksek basınç altında üretilen malzemelerin dayanıklılığı.
- Yapı elemanlarının basınca, çevresel etkenlere ve aşınmaya karşı direncinin artması.
- Enerji Verimliliği
- Hidroform preslerin enerji tüketimi ve verimliliği.
- Düşük enerji tüketimi ile yüksek verimli üretim sağlama avantajı.
- Malzeme Tasarrufu ve Ekolojik Avantajlar
- Az katkı maddesi ile dayanıklı ürün elde edilmesi.
- Daha az malzeme ile sağlam yapı elemanları üretimi, bu sayede çevresel sürdürülebilirlik katkısı.
- Üretim Hızı ve Verimlilik
- Hidroform preslerin seri üretim kapasitesi.
- İstenen boyut ve şekillerde yapı elemanları üretim hızının artması.
- Düşük Bakım Maliyetleri ve Uzun Ömür
- Dayanıklı ve uzun ömürlü parçalar kullanıldığı için düşük bakım maliyetleri.
- Hidrolik sistemin bakım kolaylığı ve uzun ömürlü olması.
4. Hidroform Preslerin Uygulama Alanları
- Beton Blok Üretimi
- Yüksek mukavemetli beton blokların üretim süreci.
- Beton blok üretiminde hidroform presin rolü.
- Yapı Malzemeleri ve Modüler Eleman Üretimi
- Tuğla, parke taşı, bordür taşı gibi yapı elemanlarının üretilmesi.
- Modüler yapı projelerinde hidroform preslerle üretilen elemanların avantajları.
- Geri Dönüştürülebilir Malzemelerle Çalışma İmkanı
- Geri dönüşümden elde edilen malzemelerle kaliteli yapı elemanları üretme.
- Çevresel sürdürülebilirlik açısından geri dönüştürülebilir malzemelerin kullanım avantajları.
5. Hidroform Preslerin Çeşitleri ve Seçim Kriterleri
- Farklı Basınç Kapasitelerine Göre Pres Çeşitleri
- Düşük, orta ve yüksek basınç kapasitesine sahip preslerin özellikleri.
- Farklı yapı malzemeleri için uygun pres çeşitlerinin karşılaştırılması.
- Kalıplama Kapasiteleri ve Özelleştirilebilirlik
- Farklı kalıplar kullanarak özelleştirilebilir ürünler üretme.
- Standart ve özel üretim için uygun modellerin değerlendirilmesi.
- Enerji Tüketimi ve Ekonomik Modeller
- Düşük enerji tüketimli modellerin seçimi ve maliyet avantajları.
- Büyük üretim hacmi olan işletmeler için uygun ekonomik çözümler.
6. Hidroform Pres Kullanımının İnşaat Sektöründeki Geleceği
- Sürdürülebilir Yapı Malzemeleri Üretimi
- Hidroform preslerle çevre dostu yapı malzemeleri üretme.
- İnşaat sektörünün çevreye duyarlılık konusundaki dönüşümünde hidroform preslerin rolü.
- Yenilikçi Malzemeler ve İleri Teknolojilerin Entegrasyonu
- Yeni malzemelerin sıkıştırılabilmesi ve dayanıklılık kazanması.
- İleri teknoloji ile akıllı hidroform pres sistemlerinin geliştirilmesi.
- Otomasyon ve Dijitalleşmenin Etkileri
- Hidroform preslerin otomasyon ve dijital izleme sistemleri ile geliştirilmesi.
- Verimlilik artışı için dijitalleşmenin etkisi ve robotik sistemlerle uyumluluk.
7. Sonuç: Hidroform Preslerinin Yapı Malzemeleri Üretiminde Sağladığı Katma Değer
- Genel Değerlendirme: Hidroform preslerin sağlam, çevreci ve ekonomik çözümler sunması.
- Gelecek Perspektifi: Hidroform preslerin daha verimli, dayanıklı ve sürdürülebilir yapı malzemeleri üretiminde artan önemi.
- İnşaat Sektöründeki İnovasyon ve Hidroform Presin Yeri: Sektörün ihtiyaçlarına göre gelişme alanları ve fırsatlar.
1. Giriş: Hidroform Pres Teknolojisi Nedir?
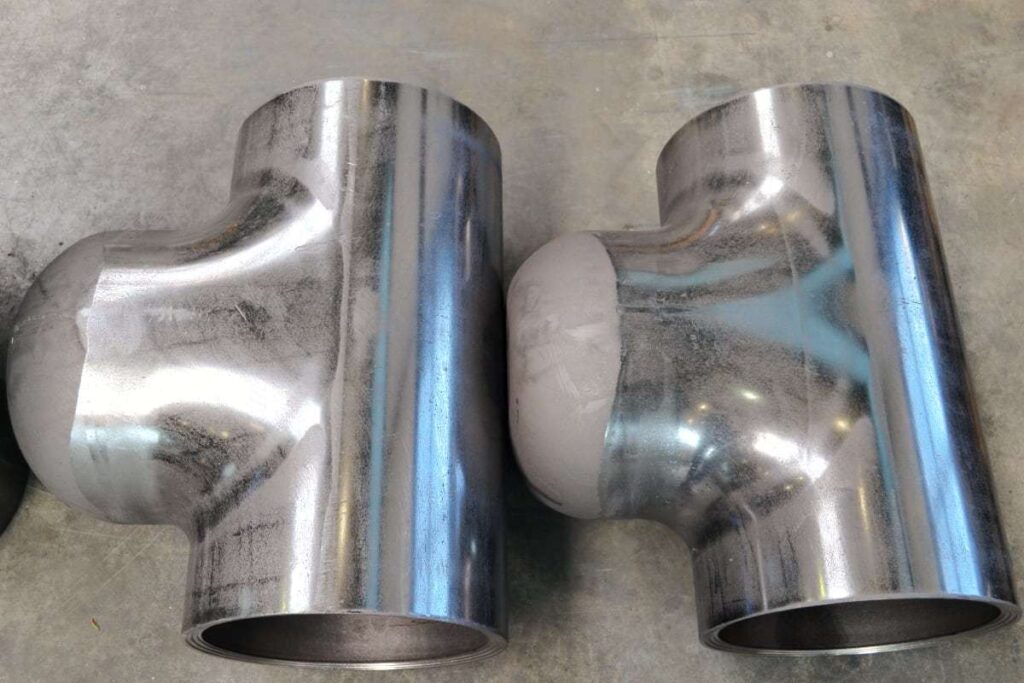
Hidroform Preslerinin Tanımı
Hidroform presler, hidrolik basınç kullanarak yapı malzemelerinin yüksek yoğunluklu, sağlam ve homojen bir yapıda üretilmesini sağlayan gelişmiş makineler olarak bilinir. Bu presler, özellikle beton bloklar, tuğla, parke taşları gibi yapı elemanlarının üretiminde tercih edilir. Hidroform preslerin çalışma prensibi, malzemeyi yüksek basınç altında kalıp içerisinde sıkıştırarak şekillendirmektir. Bu işlem, normal preslere kıyasla çok daha dayanıklı ve yoğun yapı malzemelerinin üretilmesine olanak tanır.
Kullanım Alanları
Hidroform presler, genellikle inşaat sektöründe kullanılan yapı malzemelerinin üretiminde tercih edilir. Yüksek dayanıklılık gerektiren projelerde, hidroform pres ile üretilen beton bloklar veya tuğlalar kullanılır. Özellikle dayanıklılığın önemli olduğu altyapı projeleri, konutlar, endüstriyel yapılar ve modüler yapı projeleri gibi geniş bir kullanım alanı vardır. Bu yapı malzemeleri, sağlamlıkları sayesinde uzun ömürlü ve çevresel etkenlere dayanıklı bir yapı sunar.
İnşaat Sektöründeki Önemi
Günümüz inşaat sektöründe, yapı elemanlarının dayanıklılığı ve sürdürülebilirliği önemli bir kriter haline gelmiştir. Hidroform pres teknolojisi, hem dayanıklılığı yüksek ürünler üreterek yapı ömrünü uzatır, hem de daha az katkı maddesi kullanılarak ekonomik bir üretim sağlar. Bu özellikleri nedeniyle, yapı projelerinde kaliteli malzemelere yönelik talep giderek artmaktadır. Ayrıca, hidroform preslerin geri dönüştürülebilir malzemelerle de çalışabilmesi, çevre dostu inşaat projelerinde önemli bir avantaj sağlar.
Hidroform Presinin Teknik Özellikleri
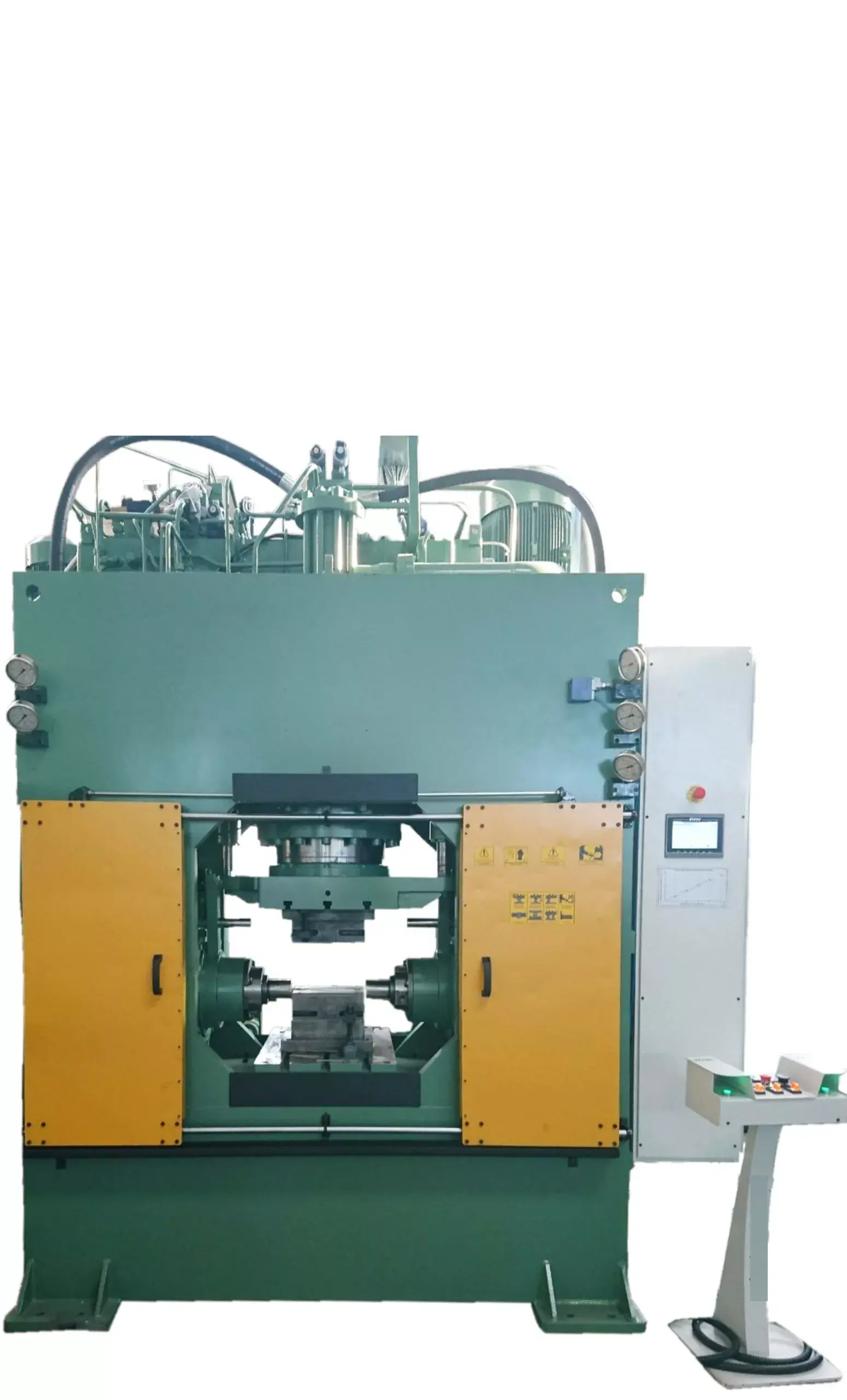
Basınç Kapasitesi
Hidroform presler, özellikle yüksek basınç altında sıkıştırma yapmalarıyla öne çıkar. Bu makinelerde kullanılan hidrolik sistemler, tipik olarak 50 ila 200 ton arasında değişen basınç kapasitesine sahiptir. Üretilecek yapı malzemesinin türüne bağlı olarak bu kapasite artırılabilir ya da azaltılabilir. Örneğin, daha dayanıklı beton bloklar için çok yüksek basınç değerleri gerekebilirken, daha hafif yapı elemanlarında bu basınç değeri daha düşük tutulabilir.
Yüksek basınç kapasitesi, özellikle inşaat projelerinde gerekli olan dayanıklı ve kompakt yapı elemanlarının üretimini mümkün kılar. Bu nedenle hidroform presler, normal preslerin sağlayamadığı yüksek dayanıklılık standartlarını karşılayarak malzemelerin yapı ömrünü uzatır.
Kalıplama ve Şekillendirme Yeteneği
Hidroform preslerin bir diğer önemli özelliği, farklı kalıplar kullanılarak çeşitli boyut ve şekillerde ürünlerin üretilebilmesidir. Bu makineler, standart boyutlarda beton blokların yanı sıra, proje gereksinimlerine göre özelleştirilmiş yapı elemanları da üretme kapasitesine sahiptir. Örneğin, özel bir yapı tasarımı için benzersiz şekillerde tuğlalar ya da parke taşları üretmek mümkündür.
Bu esneklik, hem standart yapı malzemeleri üretiminde hem de estetik açıdan özel projelerde büyük bir avantaj sağlar. Kalıplama ve şekillendirme yeteneği sayesinde, mimarlar ve mühendisler, projelerinin estetik gereksinimlerine uygun özel tasarımlar geliştirebilirler.
Malzeme Yoğunluğu ve Homojenlik
Hidroform preslerin sağladığı yüksek basınç, malzemenin içerisindeki boşlukları minimuma indirerek yoğun ve homojen bir yapı elde edilmesini sağlar. Sıkıştırma işlemi sırasında, malzemenin içinde kalan hava ve boşluklar tamamen ortadan kaldırılır, bu da üretilen yapı elemanının her noktasında aynı dayanıklılığı ve yoğunluğu sağlar.
Bu özellik, özellikle yüksek mukavemet gerektiren projelerde çok önemlidir. Homojen ve yoğun malzemeler, yapıların ömrünü uzatırken aynı zamanda çevresel etkilere karşı da daha dayanıklı hale gelir. Ayrıca, homojen yapı elemanları, taşıma, montaj ve kullanım esnasında daha güvenli ve dayanıklıdır.
Sıcaklık ve Isıl İşlem Uygulamaları
Bazı hidroform pres modelleri, sıkıştırma işlemi sırasında sıcaklık kontrolü ve ısıl işlem uygulama özelliğine sahiptir. Yüksek sıcaklık altında yapılan sıkıştırma işlemleri, bazı malzemelerin mukavemetini daha da artırabilir. Örneğin, ısıl işlem görmüş tuğlalar veya beton bloklar, normal koşullarda üretilen malzemelere göre daha uzun ömürlü ve dayanıklı olabilir. Bu tür preslerde, sıcaklık kontrol sistemleri kullanılarak homojen bir ısı dağılımı sağlanır ve yapı elemanının kalitesini artırmak için özel ısıl işlemler uygulanabilir.
Isıl işlemler sayesinde, malzemelerde oluşabilecek çatlamalar veya bozulmalar önlenir ve dış etkenlere karşı daha dirençli ürünler elde edilir. Özellikle yüksek sıcaklık veya nem gibi çevresel koşullara maruz kalacak yapılar için ısıl işlem görmüş malzemeler tercih edilir.
Hidroform Presin Sağladığı Avantajlar
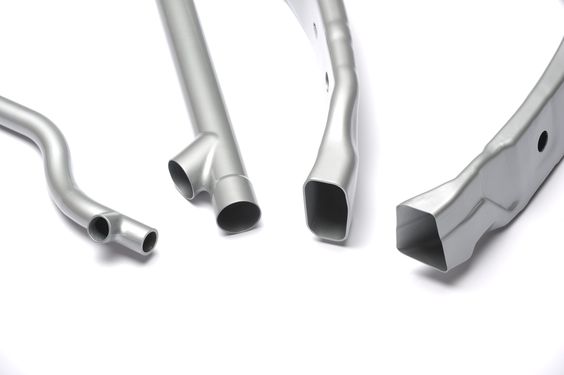
Yüksek Dayanıklılık ve Mukavemet
Hidroform presler, yapı malzemelerini yüksek basınç altında sıkıştırarak üretir; bu da üretilen malzemelerin dayanıklılığını ve mukavemetini artırır. Standart presleme yöntemlerine kıyasla, hidroform preslerle üretilen beton bloklar, tuğlalar ve diğer yapı elemanları çok daha dayanıklıdır. Bu dayanıklılık, malzemeyi daha uzun ömürlü kılarken, yapının tamamının güvenliğini de artırır. Örneğin, hidroform preslerle üretilen beton bloklar, binaların ağırlığını taşıma kapasitesi açısından geleneksel bloklara göre çok daha sağlamdır.
Ayrıca bu yöntem, özellikle aşırı hava koşulları, nem ve mekanik etkilere karşı yüksek direnç gerektiren projelerde tercih edilir. Hidroform preslerin sunduğu yüksek dayanıklılık, yapıların gelecekte bakım maliyetlerini düşürmeye yardımcı olur; çünkü sık sık yenilenme veya onarım gerektirmezler.
Enerji Verimliliği
Hidroform presler, yüksek basınç ve sıkıştırma işlemleri sırasında kullanılan enerji açısından da verimlidir. Günümüzde enerji maliyetlerinin artması, inşaat sektöründe enerji verimliliği konusunu daha önemli hale getirmiştir. Hidroform presler, enerji tüketimini optimize ederek düşük enerji ile yüksek verimli üretim sağlar. Bu, özellikle büyük hacimli üretim yapan tesisler için uzun vadede büyük bir maliyet avantajı sunar.
Enerji verimliliği sadece maliyetleri düşürmekle kalmaz, aynı zamanda çevresel sürdürülebilirliği de destekler. Daha az enerji harcayarak yüksek kaliteli ürün elde edilmesi, karbon ayak izini azaltır ve çevreye duyarlı projelerde hidroform preslerin tercih edilmesine yol açar.
Malzeme Tasarrufu ve Ekolojik Avantajlar
Hidroform presler, yapı malzemelerinin yoğunluğunu artırarak daha az malzeme ile daha dayanıklı ürünler üretmeyi mümkün kılar. Standart presleme yöntemlerinde malzeme yoğunluğunu artırmak için ekstra katkı maddeleri veya ek malzemeler gerekebilir. Ancak, hidroform preslerde uygulanan yüksek basınç sayesinde daha az katkı maddesiyle daha sağlam yapı elemanları elde edilir. Bu durum, hem üretim maliyetlerini azaltır hem de malzeme tasarrufu sağlar.
Ekolojik açıdan, daha az malzeme kullanımı çevresel etkileri de azaltır. Daha az doğal kaynak kullanımı ve geri dönüştürülebilir malzemelerin hidroform preslerle işlenmesi, çevre dostu inşaat projelerinde büyük bir avantaj sağlar. Hidroform presler, sürdürülebilir bir üretim süreci sağladığı için yeşil bina sertifikasyonu ve çevreye duyarlı yapı projelerinde önemli bir rol oynar.
Üretim Hızı ve Verimlilik
Hidroform presler, yapı elemanlarının seri üretiminde büyük bir hız ve verimlilik sağlar. Bu makineler, kısa sürede yüksek hacimli ürün üretebilir ve özellikle büyük projelerde üretim sürecini hızlandırır. Örneğin, bir inşaat projesinde kullanılan beton blokların sayısı oldukça fazladır ve bu blokların hızlı bir şekilde üretilmesi, projenin tamamlanma süresini kısaltır.
Seri üretim kapasitesi, projelerin daha hızlı tamamlanmasını sağlar ve iş gücü maliyetlerini düşürür. Ayrıca, istenen boyut ve şekillerde ürün üretme esnekliği sayesinde, proje gereksinimlerine uygun özelleştirilmiş yapı elemanları kısa sürede üretilebilir. Bu durum, projelerin üretim aşamasında zamandan ve maliyetten tasarruf sağlar.
Düşük Bakım Maliyetleri ve Uzun Ömür
Hidroform presler, genellikle dayanıklı ve uzun ömürlü olacak şekilde üretilir. Hidrolik sistemleri güçlü ve sağlam olan bu makinelerin bakım maliyetleri de düşüktür. Hidroform preslerde kullanılan parçalar, yüksek kalite standartlarına göre üretildiğinden, arıza oranı daha azdır ve uzun süre dayanabilir. Bu da işletmelerin bakım ve onarım için daha az harcama yapmasını sağlar.
Hidroform preslerin uzun ömürlü olması, özellikle büyük üretim tesislerinde önemli bir avantajdır. Sürekli çalışmaya uygun olan bu makineler, kesintisiz bir üretim süreci sağlar ve işlerin aksamasını önler. Düşük bakım maliyetleri ve uzun ömür, hidroform presleri inşaat sektöründe tercih edilen makinelerden biri haline getirir.
Hidroform Preslerin Uygulama Alanları
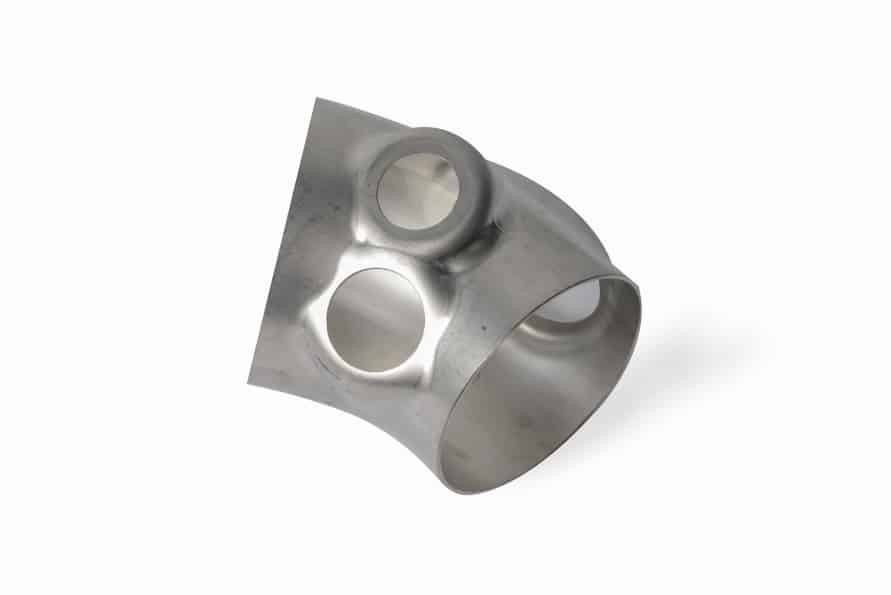
Beton Blok Üretimi
Hidroform preslerin en yaygın kullanım alanlarından biri beton blok üretimidir. İnşaat projelerinde kullanılan beton bloklar, yapıların temel taşıyıcı elemanları olarak büyük önem taşır. Hidroform preslerin yüksek basınç altında malzemeyi sıkıştırarak ürettiği beton bloklar, standart üretim yöntemleriyle elde edilen bloklara göre çok daha yoğun ve sağlamdır.
Yüksek mukavemetli beton bloklar, özellikle çok katlı binalar, köprüler, tüneller ve barajlar gibi büyük ölçekli projelerde tercih edilir. Bu bloklar, ağır yük taşıma kapasitesine sahip oldukları için güvenli bir yapı sağlar. Hidroform pres ile üretilen beton blokların homojen ve kompakt yapısı, binaların güvenlik ve dayanıklılık standartlarını artırır. Ayrıca, bu bloklar çevresel etkilere karşı daha dirençli olduğundan, uzun yıllar boyunca dayanıklılığını korur.
Yapı Malzemeleri ve Modüler Eleman Üretimi
Hidroform presler, yalnızca beton bloklarla sınırlı kalmaz; aynı zamanda tuğla, parke taşı, bordür taşı gibi çeşitli yapı elemanlarının üretiminde de kullanılır. Bu presler, farklı kalıplarla çalışarak yapı malzemelerini çeşitli boyut ve şekillerde üretebilir. Özellikle modüler inşaat projelerinde, hidroform preslerle üretilen standart ve özelleştirilmiş yapı elemanları büyük bir avantaj sağlar. Modüler projelerde kullanılan elemanların hızlı ve uygun maliyetle üretilmesi, projelerin tamamlanma sürecini hızlandırır.
Modüler yapılar, önceden üretilmiş bileşenlerin birleştirilmesiyle oluşturulur, bu da hızlı bir inşaat süreci sunar. Hidroform presler, proje gereksinimlerine göre özelleştirilebilen yapı elemanları ürettiği için bu tür projelerde çok yönlü bir çözüm sunar. Standart boyutların yanı sıra, estetik ve fonksiyonel gereksinimlere uygun özel şekilli yapı elemanları da bu preslerle üretilebilir.
Geri Dönüştürülebilir Malzemelerle Çalışma İmkanı
Geri dönüşüm, inşaat sektöründe giderek daha fazla önem kazanmaktadır ve hidroform presler, geri dönüştürülebilir malzemelerle çalışabilen bir teknolojiye sahiptir. Atık beton, cam ve hatta plastik gibi geri dönüştürülebilir malzemeler, belirli oranlarda karıştırılarak yeni yapı elemanları üretilebilir. Hidroform preslerde geri dönüştürülen malzemeler kullanılarak, hem doğal kaynak tüketimi azaltılır hem de çevreye verilen zarar en aza indirilir.
Geri dönüştürülebilir malzemelerle üretilen yapı elemanları, çevre dostu projelerde önemli bir yer tutar. Özellikle LEED (Leadership in Energy and Environmental Design) gibi çevre dostu sertifikalara sahip projelerde, geri dönüştürülmüş malzemeler kullanılması tercih edilir. Hidroform preslerin geri dönüşüm sürecinde sunduğu bu avantaj, çevresel sürdürülebilirlik hedeflerine katkı sağlar ve yapı projelerinin çevre üzerindeki olumsuz etkilerini azaltır.
Özel Projeler İçin Esnek Çözümler
Bazı projelerde standart ölçü ve şekillerin dışına çıkan özel yapı elemanlarına ihtiyaç duyulabilir. Hidroform presler, bu tür projeler için esnek ve özelleştirilebilir çözümler sunar. Farklı kalıpların kolayca değiştirilebilmesi sayesinde, istenen şekil ve boyutlarda yapı malzemeleri üretmek mümkün olur. Örneğin, kentsel düzenleme projelerinde veya peyzaj projelerinde kullanılan özel şekilli parke taşları ve bordürler hidroform preslerle kolayca üretilebilir.
Bu esneklik, özellikle estetik açıdan farklı tasarımlar isteyen projelerde büyük bir avantajdır. Mimari olarak benzersiz bir yapıya sahip projelerde, hidroform preslerle üretilen özelleştirilebilir yapı elemanları, tasarımın korunmasını sağlar ve projelere özel çözümler sunar. Bu esneklik, hidroform preslerin yalnızca yapı malzemeleri üretiminde değil, aynı zamanda sanat ve mimari projelerinde de kullanılmasını sağlar.
Hidroform Preslerin Çeşitleri ve Seçim Kriterleri
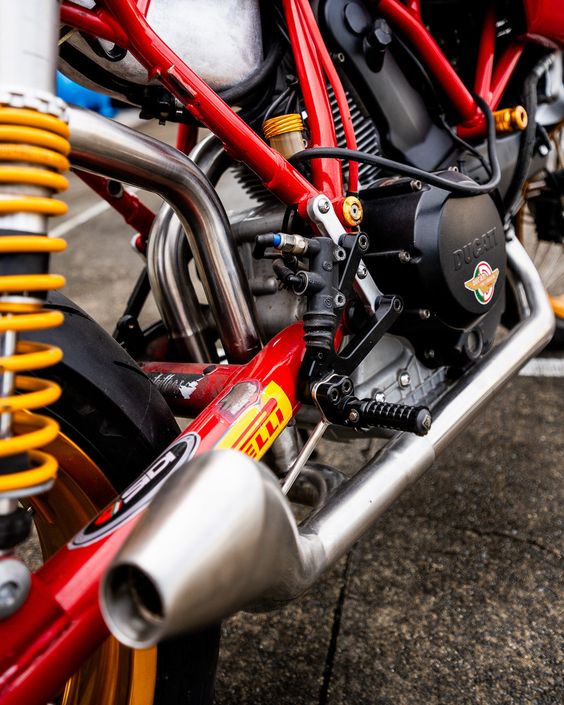
Farklı Basınç Kapasitelerine Göre Pres Çeşitleri
Hidroform presler, üretilecek yapı malzemesinin ihtiyaçlarına göre farklı basınç kapasitelerine sahip modeller sunar. Genel olarak, düşük, orta ve yüksek basınç kapasiteli hidroform presler bulunmaktadır. Basınç kapasitesi arttıkça, presin ürettiği yapı elemanlarının yoğunluğu ve dayanıklılığı da artar. Bu özellik, projelerin gereksinimlerine göre uygun basınç kapasitesine sahip pres seçilmesini sağlar.
- Düşük Basınçlı Hidroform Presler: Genellikle hafif yapı elemanları ve düşük yoğunluk gerektiren malzemeler için kullanılır. Bu tip presler, daha küçük ölçekli projeler veya estetik amaçlı yapı malzemeleri üretiminde uygundur.
- Orta Basınçlı Hidroform Presler: Konut yapımı gibi dayanıklılık gereksinimi olan ancak çok ağır basınç gerektirmeyen projelerde tercih edilir. Bu presler, standart beton blok ve tuğla üretiminde yaygın olarak kullanılır.
- Yüksek Basınçlı Hidroform Presler: Çok katlı binalar, köprüler ve altyapı projeleri gibi ağır yük taşıma kapasitesi gereken projelerde kullanılır. Bu tip presler, çok yoğun ve mukavemeti yüksek yapı elemanları üretmek için idealdir.
Pres seçimi yaparken, projenin türüne göre basınç kapasitesini dikkate almak önemlidir. Aşırı yüksek basınç kapasitesine sahip bir presin maliyeti yüksek olabilir; bu nedenle, basınç kapasitesini projenin ihtiyaçlarına uygun bir seviyede seçmek maliyet açısından da faydalı olacaktır.
Kalıplama Kapasiteleri ve Özelleştirilebilirlik
Hidroform preslerin kalıplama kapasitesi, üretilecek ürünlerin çeşitliliğini ve özelleştirilebilirliğini doğrudan etkiler. Kalıplar, pres makinelerine kolayca takılıp çıkarılabilecek şekilde tasarlanmıştır ve farklı şekillerde yapı elemanları üretebilir. Kalıpların değiştirilebilir olması, özellikle özel projeler için özelleştirilebilir yapı elemanları üretme esnekliği sunar.
- Standart Kalıplar: Genellikle standart boyutlarda beton blok, tuğla ve parke taşı üretimi için kullanılır. Standart kalıplar, seri üretim için uygundur ve yapı malzemelerinin hızlı bir şekilde üretilmesini sağlar.
- Özelleştirilmiş Kalıplar: Estetik amaçlı veya projeye özel şekillerde yapı elemanları üretmek için kullanılan kalıplardır. Özelleştirilebilir kalıplar, proje gereksinimlerine göre tasarlanabilir ve hidroform preslere entegre edilebilir.
Kalıplama kapasitesini değerlendirirken, kullanılacak kalıpların pres makinesine uygunluğuna dikkat etmek önemlidir. Ayrıca, projede gerekli olan çeşitli şekillerde ürünler üretebilmek için değiştirilebilir kalıplara sahip modeller tercih edilebilir.
Enerji Tüketimi ve Ekonomik Modeller
Hidroform preslerin enerji tüketimi, uzun vadeli maliyetler üzerinde büyük bir etkiye sahiptir. Enerji maliyetlerinin yüksek olduğu günümüzde, düşük enerji tüketimli modeller tercih edilerek tasarruf sağlanabilir. Ekonomik modeller, üretim kapasitesini düşürmeden enerji tüketimini minimumda tutacak şekilde tasarlanmıştır. Bu tür presler, özellikle büyük üretim tesisleri veya uzun süreli üretim süreçleri için uygundur.
Enerji tüketimi dikkate alınarak yapılan doğru bir seçim, işletme maliyetlerinde uzun vadede tasarruf sağlar. Bu nedenle, büyük ölçekli üretim yapan tesisler, enerji verimliliğine sahip presleri tercih ederek maliyetlerini optimize edebilirler. Aynı zamanda, çevresel sürdürülebilirlik hedeflerine ulaşmak isteyen işletmeler için düşük enerji tüketimli modeller büyük bir avantaj sunar.
Büyük Üretim Hacmi Olan İşletmeler İçin Uygun Ekonomik Çözümler
Büyük ölçekli projelerde yüksek hacimli üretim yapabilen hidroform presler tercih edilir. Yüksek üretim kapasitesine sahip ekonomik modeller, geniş çaplı inşaat projelerinde hız ve verimlilik sağlar. Bu modeller, daha az duraklama süresi, kolay bakım ve yüksek dayanıklılıkla öne çıkar. Özellikle üretim tesislerinde maliyet avantajı sağlamak adına ekonomik çözümler tercih edilir.
Hidroform Pres Kullanımının İnşaat Sektöründeki Geleceği
Sürdürülebilir Yapı Malzemeleri Üretimi
Günümüzde inşaat sektörü, çevresel etkilerini azaltmaya yönelik çözümler arayışında ve sürdürülebilir yapı malzemelerine olan talep giderek artmakta. Hidroform presler, çevreye duyarlı yapı malzemeleri üretmek için ideal bir araçtır. Bu preslerin geri dönüştürülebilir malzemelerle çalışabilme yeteneği, inşaat sektörünün sürdürülebilirlik hedeflerine ulaşmasına katkı sağlar. Geri dönüştürülmüş malzemelerle üretilen beton bloklar veya tuğlalar, projelerde kullanılan doğal kaynak miktarını azaltır ve karbon ayak izini düşürür.
Sürdürülebilir malzeme üretimi, aynı zamanda yeşil bina standartlarına (LEED, BREEAM gibi) uygun projelerin sayısını artırır. Hidroform preslerle üretilen çevre dostu yapı elemanları, bu tür projelerde tercih edilerek ekolojik etkilerin azaltılmasına katkıda bulunur. Sürdürülebilir üretim süreçlerinin önemi arttıkça, hidroform preslerin inşaat sektöründeki önemi de artmaya devam edecektir.
Yenilikçi Malzemeler ve İleri Teknolojilerin Entegrasyonu
Hidroform pres teknolojisi, yeni yapı malzemelerinin geliştirilmesi ve mevcut malzemelerin özelliklerinin iyileştirilmesi açısından geniş bir potansiyele sahiptir. Örneğin, kompozit malzemeler veya ultra yüksek mukavemetli betonlar gibi yenilikçi malzemeler, hidroform preslerde işlenerek yoğun ve dayanıklı hale getirilebilir. Bu durum, yapı malzemelerinin daha hafif, daha dayanıklı ve daha esnek olmasına olanak tanır.
İleri teknolojiyle entegre edilen hidroform presler, akıllı sensörler ve otomasyon sistemleri sayesinde üretim süreçlerini optimize edebilir. Bu tür akıllı presler, sıkıştırma sürecini izleyerek malzeme kalitesini kontrol altında tutar ve her üründe aynı dayanıklılık ve yoğunluk seviyesini sağlar. Bu otomasyon ve dijital entegrasyon sayesinde, preslerin verimliliği artarken, hata oranı azalır. Teknolojinin gelişmesiyle birlikte, inşaat sektöründe daha verimli, dayanıklı ve hafif yapı malzemelerine olan talep de artacağından, hidroform preslerin bu yeniliklere uyum sağlaması beklenmektedir.
Otomasyon ve Dijitalleşmenin Etkileri
Endüstri 4.0 ile birlikte, üretim süreçlerinde otomasyon ve dijitalleşme hız kazanmıştır. Hidroform presler de bu dönüşümden etkilenerek otomasyon sistemleriyle donatılmaya başlanmıştır. Akıllı hidroform presler, üretim sürecini gerçek zamanlı olarak izleyebilir, verileri analiz edebilir ve gerektiğinde müdahalede bulunabilir. Bu durum, üretim sürecini hızlandırırken hata oranını en aza indirir. Otomasyon sistemleri sayesinde, presin bakım ihtiyaçları önceden tahmin edilebilir ve gerekli önlemler alınarak kesintisiz bir üretim süreci sağlanır.
Dijitalleşmenin etkisi, özellikle büyük ölçekli projelerde ve üretim tesislerinde daha belirgin hale gelir. Otomatik presler, iş gücü gereksinimini azaltarak maliyetleri düşürür ve verimliliği artırır. Ayrıca, uzaktan izleme ve kontrol sistemleri sayesinde üretim süreci her an takip edilebilir. Bu gelişmeler, hidroform preslerin uzun vadede inşaat sektörü için daha cazip hale gelmesine katkıda bulunacaktır.
Gelecek Perspektifi: Hidroform Preslerin İnşaat Sektöründeki Artan Önemi
Hidroform presler, inşaat sektöründe daha dayanıklı, çevre dostu ve özelleştirilebilir yapı malzemeleri üretimi için gelecekte daha da önemli hale gelecektir. Sektörün sürdürülebilirlik hedeflerine ulaşması, yapıların dayanıklılığını artırmak ve çevresel etkileri azaltmak için hidroform preslere olan talep artacaktır. Aynı zamanda, bu preslerin dijitalleşme ve otomasyon sistemleriyle entegre edilmesi, üretim süreçlerini daha verimli ve ekonomik hale getirecektir.
Hidroform preslerin inşaat sektöründe sunduğu esneklik, dayanıklılık ve sürdürülebilirlik avantajları, onları geleceğin yapı malzemeleri üretiminde vazgeçilmez bir araç haline getirecektir. Gelecek projeksiyonları, daha gelişmiş malzemelerle çalışan, akıllı otomasyon sistemleriyle donatılmış ve sürdürülebilirlik odaklı hidroform preslerin inşaat sektöründe yaygın olarak kullanılacağını göstermektedir.
Sonuç: Hidroform Preslerinin Yapı Malzemeleri Üretiminde Sağladığı Katma Değer
Hidroform presler, inşaat sektöründe dayanıklı, yoğun ve çevre dostu yapı malzemeleri üretiminde vazgeçilmez bir araç haline gelmiştir. Yüksek basınç altında yapılan sıkıştırma işlemi, beton bloklardan tuğlalara, parke taşlarından bordürlere kadar pek çok yapı elemanının mukavemetini artırırken homojen ve kompakt bir yapı sağlar. Hidroform preslerin sunduğu yüksek dayanıklılık ve malzeme yoğunluğu, yapıların güvenlik ve uzun ömürlülüğünü artırarak inşaat projelerinin değerini yükseltir.
Hidroform presler, enerji verimliliği ve malzeme tasarrufu sunarak sürdürülebilir projelerde de önemli bir rol oynamaktadır. Özellikle geri dönüştürülebilir malzemelerle çalışma imkanı, çevreye duyarlı projelerde hidroform preslerin tercih edilmesini sağlar. Bu makineler, inşaat sektöründe sürdürülebilir yapı malzemeleri üretme konusundaki talepleri karşılayarak çevresel sorumluluğun bir parçası haline gelir.
Geleceğe dönük olarak, hidroform presler yeni teknoloji ve malzemelerin entegrasyonuyla daha da gelişecektir. Akıllı sensörler ve otomasyon sistemleri ile donatılmış, dijital olarak izlenebilen ve düşük enerji tüketimi sağlayan hidroform presler, sektörde verimliliği artırırken hata oranını azaltacaktır. Bu gelişmeler, hidroform preslerin sadece geleneksel yapı malzemeleri üretiminde değil, aynı zamanda yenilikçi projelerde ve yeşil bina sertifikalarına uygun yapı elemanlarının üretiminde de önemli bir yer edinmesini sağlayacaktır.
Özetle, hidroform presler inşaat sektörünün güvenilir, ekonomik ve çevre dostu yapı malzemeleri üretme ihtiyacını karşılayarak sektörde kalıcı bir çözüm sunmaktadır. Hem dayanıklılığı yüksek ürünler sunarak yapıların güvenliğini artırmakta, hem de sürdürülebilirlik hedeflerine ulaşmaya yardımcı olmaktadır. Bu özellikleri ile hidroform preslerin, yapı malzemeleri üretiminde önümüzdeki yıllarda da çok önemli bir rol oynayacağı öngörülmektedir.
Hidroform Preslerinin Tanımı – İçerik Taslağı
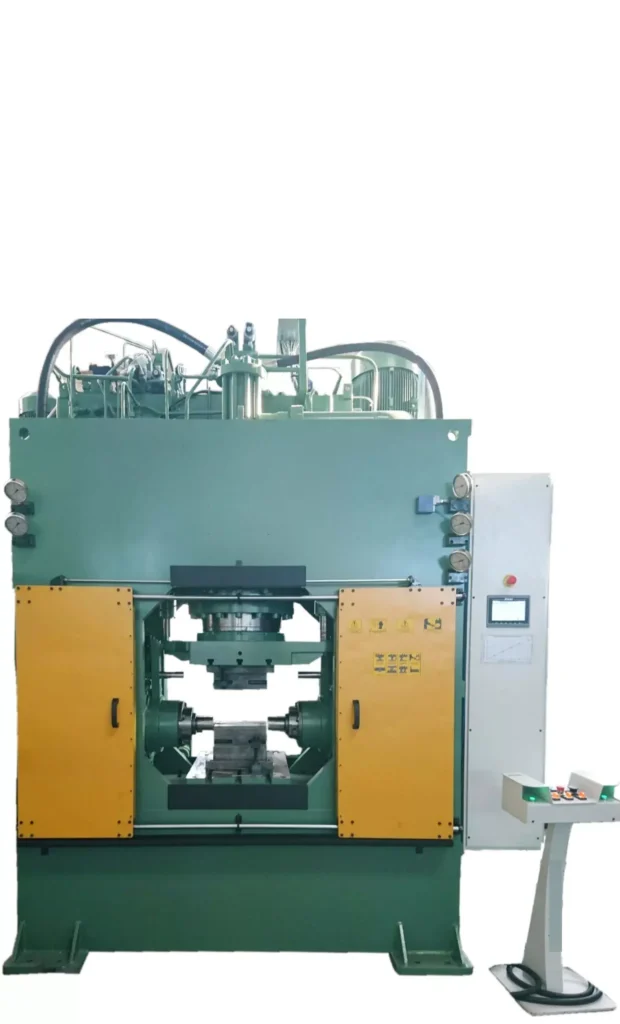
1. Giriş: Hidroform Pres Nedir?
- Hidroform preslerin genel tanımı ve temel özellikleri.
- Hidroform preslerin inşaat sektöründeki artan önemi ve kullanımı.
2. Hidroform Preslerin Çalışma Prensibi
- Hidroform preslerin hidrolik sistemlerle çalışma yapısı.
- Yüksek basınç altında malzemelerin şekillendirilmesi.
- Sıkıştırma ve kalıplama sürecinin işleyişi.
3. Hidroform Pres Teknolojisinin Tarihçesi ve Gelişimi
- Hidrolik pres teknolojisinin ortaya çıkışı ve tarihçesi.
- Hidroform preslerin gelişim süreci.
- Günümüzdeki hidroform pres teknolojisinin endüstriyel kullanımı.
4. Hidroform Preslerin Teknik Yapısı
- Hidroform preslerin bileşenleri (hidrolik sistem, piston, kalıp, basınç regülatörleri vb.).
- Farklı tiplerdeki hidroform preslerin yapısal özellikleri.
- Hidroform preslerde kullanılan hidrolik yağ ve basınç denetleme sistemleri.
5. Hidroform Preslerin Çalışma Süreci ve Uygulama Alanları
- Hidroform preslerde uygulanan aşamalar (hazırlık, sıkıştırma, kalıplama, çıkış).
- İnşaat sektörü için üretilen yapı elemanlarının süreçleri.
- Geri dönüştürülebilir malzemeler ve özel projeler için uygulama örnekleri.
6. Hidroform Preslerle Üretilen Ürünler ve Kullanım Alanları
- Hidroform preslerle üretilen yapı elemanları (beton blok, tuğla, parke taşı vb.).
- Hidroform preslerin tercih edildiği sektörler (inşaat, altyapı, çevre düzenleme).
- Geniş kullanım alanları ve esneklik sağlayan ürün çeşitleri.
7. Hidroform Preslerin Avantajları ve Faydaları
- Yüksek mukavemetli ve dayanıklı malzemeler üretme imkanı.
- Malzeme yoğunluğu ve homojenlik sağlama.
- Enerji tasarrufu ve çevresel avantajları.
8. Hidroform Pres Teknolojisinin Geleceği
- Hidroform preslerin inşaat sektöründe ve diğer alanlarda artan kullanımı.
- Otomasyon ve dijitalleşme ile hidroform preslerin gelişim yönü.
- Hidroform preslerin sürdürülebilir inşaat projelerine katkısı.
Giriş: Hidroform Pres Nedir?
Hidroform Preslerin Genel Tanımı ve Temel Özellikleri
Hidroform presler, yüksek basınç uygulayarak çeşitli malzemeleri kalıplar içinde sıkıştırarak yoğun ve dayanıklı yapı elemanları oluşturan hidrolik pres sistemleridir. Hidroform preslerin temel özelliği, malzemeleri çok güçlü bir basınç altında sıkıştırarak homojen ve yüksek mukavemetli ürünler elde etme imkanı sunmasıdır. Bu makineler, genellikle hidrolik yağlar veya su bazlı hidrolik sistemlerle çalışır ve oldukça yüksek tonajlarda basınç üretebilir. Yapısal olarak hidroform presler, hidrolik basınç sağlayan bir motor, basınç regülatörleri, piston ve kalıplardan oluşur.
Hidroform preslerin bir diğer karakteristik özelliği, malzemeleri sadece şekillendirmekle kalmayıp, aynı zamanda bu malzemelerin yoğunluğunu da artırarak dayanıklılığı yüksek ürünler üretmesidir. Özellikle inşaat sektöründe, yoğun, homojen ve dayanıklı malzemelerin kullanılması yapıların ömrünü uzatırken güvenliğini artırır. Bu nedenle hidroform presler, beton bloklar, tuğlalar, parke taşları, bordürler gibi inşaat sektöründe yaygın olarak kullanılan yapı elemanlarının üretiminde büyük bir önem taşır.
Hidroform Preslerin İnşaat Sektöründeki Artan Önemi
Günümüzde inşaat sektörü, yapı malzemelerinin dayanıklılığını ve sürdürülebilirliğini sağlamak için daha gelişmiş ve verimli teknolojilere yönelmektedir. Hidroform presler, özellikle yapı elemanlarının dayanıklılığını artırma ve uzun ömürlü yapılar inşa etme hedefi olan projelerde sıkça tercih edilmektedir. Beton blokların, tuğlaların ve diğer yapı elemanlarının yüksek basınçla sıkıştırılması, malzemelerin mukavemetini artırırken, bina güvenliğini ve çevresel direnci de yükseltmektedir.
Bu makineler, aynı zamanda hızlı üretim süreci ve düşük enerji tüketimi ile de dikkat çeker. Hidroform preslerin sağladığı yüksek verimlilik, büyük ölçekli inşaat projelerinde zaman ve maliyet tasarrufu sağlar. İnşaat sektöründe hidroform preslerin artan önemi, bu makinelerin gelişmiş projelerde dayanıklılık, kalite ve sürdürülebilirlik açısından güvenilir bir çözüm olarak benimsenmesine yol açmıştır.
Hidroform Preslerin Çalışma Prensibi
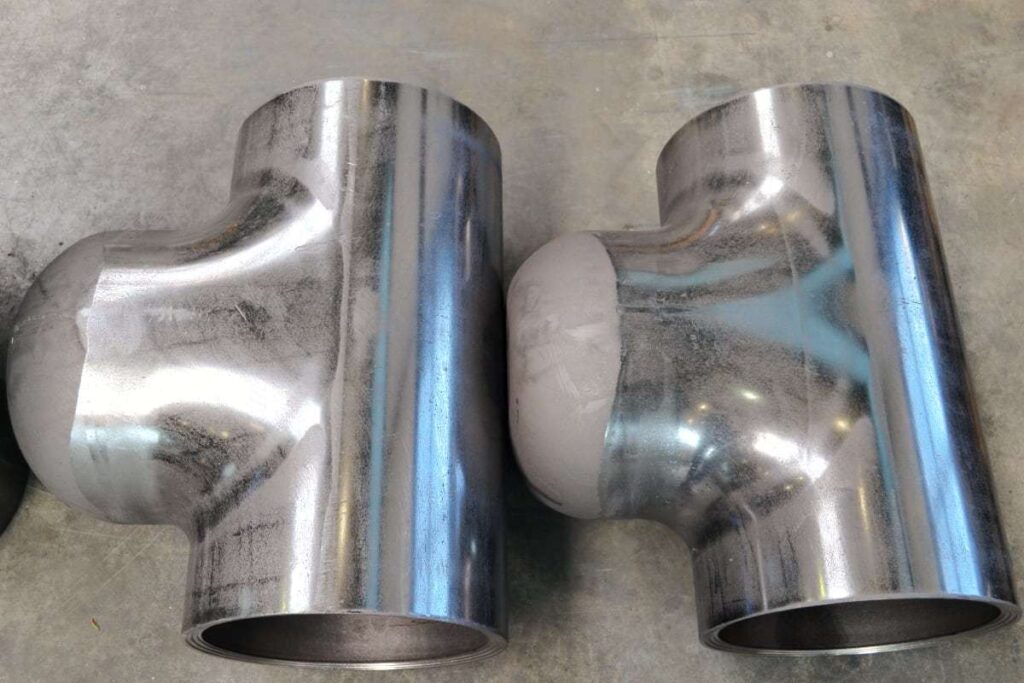
Hidrolik Sistemle Çalışma Yapısı
Hidroform preslerin çalışma prensibi, hidrolik basınç kullanarak malzemeleri kalıplar içerisinde yoğunlaştırma esasına dayanır. Bu makineler, hidrolik sistemleri aracılığıyla yüksek basınç oluşturur ve bu basıncı malzemeye uygulayarak sıkıştırma işlemini gerçekleştirir. Hidrolik sistemin kalbinde yer alan hidrolik yağ veya su bazlı sıvılar, bir piston veya silindir içinde hareket ettirilir ve yüksek basınçlı sıvı sayesinde malzemeye uygulanan kuvvet artırılır.
Hidroform presin temel işlevi, basıncı eşit ve homojen bir şekilde malzemenin tüm yüzeyine dağıtarak kalıp içerisine sıkıştırılmasıdır. Bu sıkıştırma işlemi sırasında, malzeme içerisindeki hava boşlukları ortadan kaldırılır ve malzeme kompakt, yoğun bir yapı haline getirilir. Bu yoğunluk, malzemenin mukavemetini artırırken aynı zamanda yapısal dayanıklılığı da sağlar.
Yüksek Basınç Altında Malzemelerin Şekillendirilmesi
Hidroform preslerin ana çalışma prensiplerinden biri de malzemeyi yüksek basınç altında şekillendirme sürecidir. Genellikle 50 ila 200 ton arasında değişen basınç değerleri uygulanır ve bu basınç, malzemenin kalıp içine tam olarak oturmasını sağlar. Bu işlem sırasında kullanılan basınç miktarı, üretilmek istenen yapı elemanının cinsine ve dayanıklılık gereksinimlerine göre ayarlanabilir. Örneğin, yüksek mukavemetli beton bloklar için gereken basınç değeri, standart beton bloklara göre daha yüksek olabilir.
Şekillendirme süreci, hidroform presin kalıplarına bağlı olarak değişiklik gösterir. Özellikle özel projelerde kullanılan şekilli yapı elemanları veya estetik özellikler gerektiren ürünler için farklı kalıplar kullanılarak özelleştirilmiş yapı elemanları elde edilir. Basıncın tüm yüzeylere homojen bir şekilde yayılması, ürünün her noktasında aynı dayanıklılık ve yoğunluk seviyesini sağlar.
Sıkıştırma ve Kalıplama Sürecinin İşleyişi
Hidroform preslerde sıkıştırma ve kalıplama işlemi, birbirini takip eden adımlardan oluşur ve her adım üretim sürecinde belirli bir işlevi yerine getirir:
- Hazırlık Aşaması: Malzeme, önceden belirlenen kalıplara yerleştirilir ve hidrolik sistemin basınca hazır hale gelmesi sağlanır. Bu aşamada malzemenin homojen bir şekilde dağıtılması ve kalıba tam oturması sağlanır.
- Basınç Uygulama Aşaması: Hidrolik sistem, kalıptaki malzemeye basınç uygulamaya başlar. Bu aşamada, malzeme içerisindeki boşluklar ortadan kaldırılır ve sıkıştırma işlemi başlar. Hidroform presin motoru, gereken basıncı sağlamak için çalışır ve malzeme tamamen sıkıştırılıncaya kadar bu basınç devam eder.
- Kalıplama ve Şekillendirme Aşaması: Basınç altında şekillendirilen malzeme, kalıp içerisine tam olarak yerleşir. Kalıp formuna göre şekillenen yapı elemanı, homojen ve yoğun bir yapıya sahip olur. Bu aşamada kalıp kullanımı, üretilen ürünün nihai şeklinin belirlenmesini sağlar.
- Çıkış Aşaması: Sıkıştırılmış malzeme, kalıptan çıkarılır ve kurutulma veya soğutma işlemlerine geçilir. Çıkarılan ürün, son kontrollerden geçerek dayanıklılık ve kalite açısından değerlendirilir.
Bu aşamalar, hidroform preslerin her türlü yapı elemanını dayanıklı ve sağlam bir yapıya dönüştürmesi için oldukça önemlidir. Her aşama, ürün kalitesinin korunması ve malzeme mukavemetinin artırılması için dikkatle yönetilir. Bu işlemler sayesinde, hidroform preslerde üretilen malzemeler homojen, yoğun ve çevresel etkilere karşı dayanıklı hale gelir.
Hidroform Pres Teknolojisinin Tarihçesi ve Gelişimi
Hidrolik Pres Teknolojisinin Ortaya Çıkışı
Hidroform preslerin gelişimi, hidrolik pres teknolojisinin temel prensiplerine dayanır. Hidrolik preslerin ilk ortaya çıkışı, 18. yüzyılın sonlarına doğru İngiliz mucit Joseph Bramah’ın çalışmalarıyla gerçekleşmiştir. 1795 yılında Bramah, “Bramah Presi” olarak bilinen ilk hidrolik presi icat ederek basınç altında sıkıştırma prensibini uygulamaya koymuştur. Bu makine, basit bir hidrolik pompa aracılığıyla çalışmakta ve sıvı basıncını kullanarak malzemelerin sıkıştırılmasını sağlamaktadır.
Hidrolik preslerin kullanımı, başlangıçta yalnızca temel sıkıştırma işlemleri için kullanılırken, zamanla endüstriyel ve inşaat sektörü gibi alanlarda yaygınlaşmıştır. Basınç kullanarak daha dayanıklı ve yoğun malzemeler üretebilme kapasitesi sayesinde, hidrolik pres teknolojisi sanayinin birçok alanında vazgeçilmez bir araç haline gelmiştir. 20. yüzyılda ise, yüksek tonajlı ve güçlü preslerin geliştirilmesiyle, günümüzde kullanılan hidroform preslerin temelleri atılmıştır.
Hidroform Preslerin Gelişim Süreci
Hidroform preslerin ortaya çıkışı ve yaygınlaşması, özellikle inşaat sektörü ve büyük ölçekli yapı projeleri için dayanıklı ve uzun ömürlü yapı elemanları üretme ihtiyacının artmasıyla hız kazanmıştır. 20. yüzyılın ortalarından itibaren, dayanıklılığı artırılmış beton bloklar, tuğlalar ve parke taşları gibi yapı elemanlarının üretimi için hidroform presler geliştirilmeye başlanmıştır. Hidroform pres teknolojisi, hidrolik preslerin daha yüksek basınçlarda çalışma kapasitesi kazanmasıyla evrilmiş ve yapı malzemelerini daha homojen bir şekilde sıkıştırarak kalıba dökme imkanı sunmuştur.
1970’lerde ve 1980’lerde gelişen otomasyon teknolojisi, hidroform preslerin daha geniş çapta kullanımını sağlamıştır. Bu dönemde geliştirilen makinelerde, hidrolik sistemler elektronik kontrol sistemleri ile entegre edilmiştir ve bu sayede basınç, hız ve sıcaklık gibi parametreler daha hassas bir şekilde kontrol edilebilir hale gelmiştir. Otomasyon sistemleriyle geliştirilen hidroform presler, yapı malzemesi üretiminde seri üretimi mümkün kılmıştır ve günümüzdeki yüksek kapasiteli üretim tesislerinin temel taşını oluşturmuştur.
Günümüzdeki Hidroform Pres Teknolojisi ve Endüstriyel Kullanımı
Günümüzde hidroform presler, hem inşaat sektörü hem de çevre düzenlemesi, modüler yapı projeleri, altyapı çalışmaları gibi birçok farklı endüstride yoğun olarak kullanılmaktadır. Yüksek basınç kapasitesi, dayanıklılığı yüksek yapı elemanları üretme imkanı sunarken, otomasyon sistemleri ile donatılmış makinelerle seri üretim yapılabilmektedir. Ayrıca, hidrolik preslerin çevresel sürdürülebilirlik sağlama kapasitesi, geri dönüştürülebilir malzemeler kullanılarak çevreye duyarlı yapı elemanları üretme imkanı sunmaktadır.
Modern hidroform preslerde, basınç ve sıcaklık gibi parametrelerin bilgisayar destekli kontrol sistemleri ile yönetilmesi sayesinde üretim süreçleri daha güvenli, hızlı ve verimli hale gelmiştir. Günümüzde akıllı teknolojilerle entegre edilen hidroform presler, otomatik izleme sistemleri ve hata tespit algoritmaları ile kesintisiz üretim sağlamakta ve işletme maliyetlerini düşürmektedir. Bu gelişmeler, hidroform preslerin endüstriyel kullanımlarını daha verimli hale getirerek inşaat sektöründe vazgeçilmez bir araç olmasını sağlamıştır.
Hidroform Preslerin Teknik Yapısı
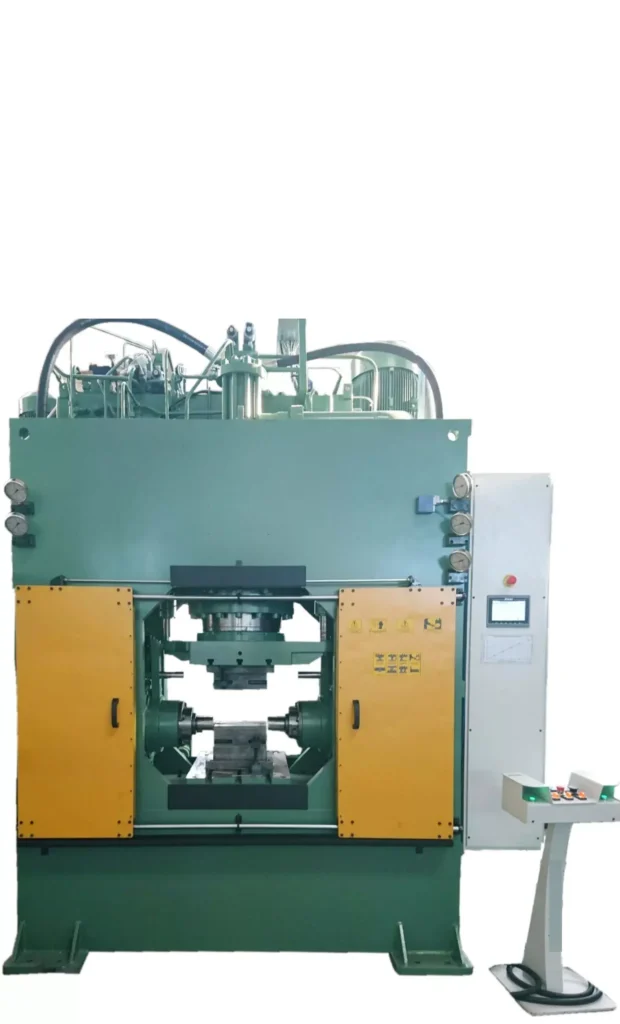
Hidroform Preslerin Bileşenleri
Hidroform preslerin verimli bir şekilde çalışmasını sağlayan birden fazla bileşeni bulunmaktadır. Bu bileşenler, hidrolik basınç üretmek, bu basıncı malzemeye uygulamak ve malzemeyi sıkıştırarak istenilen forma getirmek için uyum içinde çalışır. Temel bileşenler şunlardır:
- Hidrolik Sistem: Hidroform presin ana gücünü sağlayan hidrolik sistem, presin kalbidir. Bu sistem, basınç üretmek için hidrolik yağı veya su bazlı hidrolik sıvılar kullanır. Basınç, hidrolik sistemdeki pistonlara iletilir ve sıkıştırma işlemi bu basınç ile gerçekleştirilir. Hidrolik sistem, presin basınç değerlerini kontrol edebilmesi için basınç regülatörleri ile donatılmıştır.
- Piston: Piston, hidrolik basıncı doğrudan malzemeye uygulayan bileşendir. Basınç altındaki hidrolik sıvı, pistonun hareket etmesine neden olur ve bu hareket, kalıptaki malzemeye kuvvet uygulayarak sıkıştırır. Piston, dayanıklı ve yüksek mukavemetli materyallerden yapılır, çünkü sıkıştırma işlemi sırasında büyük bir baskı altında çalışır.
- Kalıp: Hidroform preslerde, üretilmek istenen yapı elemanının şekline göre kalıplar kullanılır. Bu kalıplar, malzemeye şekil vermek için özel olarak tasarlanmıştır. Kalıplar genellikle çelik veya yüksek dayanıklılığa sahip alaşımlardan üretilir, çünkü yüksek basınç altında bozulmadan formunu koruması gerekir. Kalıplar değiştirilebilir özelliktedir; bu da farklı şekil ve boyutlarda ürünlerin üretimine olanak tanır.
- Basınç Regülatörleri ve Valfler: Hidrolik sistemdeki basıncı kontrol eden regülatörler, sıkıştırma işlemi sırasında istenilen basınç seviyesini korumayı sağlar. Valfler ise hidrolik sıvının akış yönünü ve hızını kontrol eder. Bu bileşenler, sıkıştırma işleminin istenen şekilde gerçekleşmesini sağlar ve presin güvenli çalışmasına katkıda bulunur.
- Elektronik Kontrol Sistemi: Modern hidroform preslerde, basınç, sıcaklık, hız gibi parametreleri yönetmek için elektronik kontrol sistemleri bulunur. Bu sistemler, operatörün her bir aşamayı kontrol etmesine olanak tanır ve hata riskini azaltır. Ayrıca, bilgisayar destekli kontrol sistemleri sayesinde, presin çalışma süreci otomatikleştirilmiş ve verimli hale getirilmiştir.
Farklı Tiplerdeki Hidroform Preslerin Yapısal Özellikleri
Hidroform presler, farklı üretim ihtiyaçlarına göre çeşitli tiplerde ve kapasitelerde üretilir. Basınç kapasitesine ve uygulama alanına göre farklı türlerde hidroform presler mevcuttur:
- Düşük Basınçlı Hidroform Presler: Küçük ölçekli projeler veya hafif yapı elemanları üretimi için tercih edilir. Basınç kapasitesi daha düşük olduğundan daha az dayanıklı ürünlerin üretiminde kullanılır.
- Orta Basınçlı Hidroform Presler: Standart beton bloklar, tuğlalar ve parke taşları gibi yapı elemanlarının üretiminde kullanılan preslerdir. Orta seviyedeki basınç kapasitesi sayesinde yüksek verimlilikle çalışır ve çoğu inşaat projesine uygun ürünler üretir.
- Yüksek Basınçlı Hidroform Presler: Çok katlı binalar, köprüler gibi yüksek dayanıklılık gerektiren yapı elemanları için tercih edilir. Yüksek basınç kapasitesi sayesinde dayanıklılığı yüksek ürünler üretebilir ve ağır yüklere dayanıklı yapı elemanları sağlar.
Hidroform Preslerde Kullanılan Hidrolik Yağ ve Basınç Denetleme Sistemleri
Hidroform preslerde kullanılan hidrolik sıvılar, presin işleyişini doğrudan etkiler. Hidrolik sistemlerde çoğunlukla hidrolik yağ kullanılır. Hidrolik yağ, ısıya karşı dayanıklı ve yüksek basınca dirençli özellikleri ile sıkıştırma işlemi sırasında gerekli olan kuvveti sağlar. Ayrıca, bu yağlar, sistemin aşırı ısınmasını engelleyerek presin çalışma verimliliğini artırır.
Basınç denetleme sistemleri, hidrolik yağın basıncını istenen seviyede tutar ve sıkıştırma işlemi sırasında basıncın dengeli olmasını sağlar. Basınç denetleme valfleri ve regülatörler, hidrolik sistemin düzgün çalışmasını sağlarken, basıncın fazla yükselmesi durumunda güvenlik valfleri devreye girer. Bu önlemler, presin güvenli bir şekilde çalışmasını ve arızaların önlenmesini sağlar.
Hidroform Preslerin Çalışma Süreci ve Uygulama Alanları
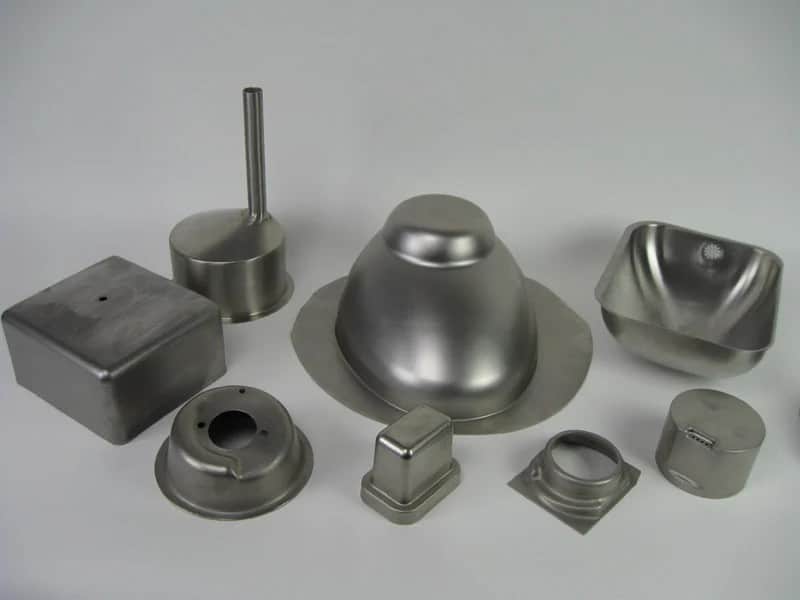
Hidroform Preslerde Uygulanan Aşamalar
Hidroform preslerin üretim süreci, malzemenin kalıba yerleştirilmesinden sıkıştırma işlemine ve son ürünün çıkarılmasına kadar belirli aşamalardan oluşur. Bu aşamalar, her seferinde aynı kalitede ürün elde edilmesini sağlar. Hidroform preslerde temel olarak şu işlemler gerçekleştirilir:
- Hazırlık Aşaması: Malzeme, sıkıştırılmak ve kalıba dökülmek üzere presin içine yerleştirilir. Kalıplar, ürüne nihai şeklini veren bileşenlerdir ve malzeme, kalıba uygun şekilde yerleştirilir. Kalıp içerisine düzgün ve homojen şekilde yerleştirilen malzeme, işlem boyunca aynı yoğunlukta kalır.
- Basınç Uygulama Aşaması: Hidrolik sistem, hazırlık aşamasında yerleştirilen malzemeye basınç uygulamaya başlar. Bu aşamada, malzeme içindeki hava ve boşluklar tamamen ortadan kaldırılır ve sıkıştırma işlemi ile yoğun bir yapı oluşturulur. Hidrolik basınç, kalıbın her noktasına eşit şekilde yayılır ve malzemeyi kalıbın tam şeklinde sıkıştırır.
- Kalıplama ve Şekillendirme Aşaması: Basınç altında sıkıştırılan malzeme, kalıp içerisine tam olarak oturur ve nihai formunu kazanır. Kalıplama süreci sırasında kullanılan basınç miktarı, malzemenin mukavemetini ve homojenliğini artırır. Basıncın homojen dağılması, malzemenin dayanıklılığını ve uzun ömürlü olmasını sağlar.
- Çıkarma ve Soğutma Aşaması: Sıkıştırılan malzeme, presin içinden çıkarılır ve kurutma veya soğutma işlemlerine tabi tutulur. Çıkartılan ürün, kalite kontrol aşamasından geçirilir ve dayanıklılık açısından test edilir. Bu son aşamada ürün, istenilen özelliklere uygun olup olmadığını kontrol eden testlerden geçerek, projeye uygunluğuna göre değerlendirilir.
Bu aşamaların her biri, hidroform presin ürettiği ürünlerin kalitesini artırmak ve aynı kalitede seri üretim yapmak için önemlidir. Süreç boyunca elektronik kontrol sistemleri ile her bir aşama takip edilerek, üretim verimliliği en üst seviyede tutulur.
İnşaat Sektörü İçin Üretilen Yapı Elemanlarının Süreçleri
Hidroform presler, inşaat sektöründe kullanılan yapı elemanlarının üretiminde yaygın olarak tercih edilir. Bu preslerle üretilen yapı elemanları arasında beton bloklar, tuğlalar, parke taşları, bordür taşları gibi malzemeler bulunur. Bu yapı elemanları, sıkıştırma ve kalıplama aşamalarında elde edilen yüksek yoğunluk sayesinde normal malzemelere kıyasla daha dayanıklıdır.
Örneğin, beton blok üretimi için, önce beton karışımı kalıba dökülür ve ardından hidroform pres, bu malzemeye çok yüksek basınç uygulayarak beton blokların daha dayanıklı hale gelmesini sağlar. Parke taşları ve bordür taşları gibi ürünlerde de aynı işlem uygulanır ve ürünlerin çevresel etkilere, darbelere karşı dayanıklılığı artırılır. Hidroform preslerin, inşaat projelerinde bu tür yapı elemanlarının üretiminde kullanılması, yapıların genel mukavemetini ve ömrünü uzatır.
Geri Dönüştürülebilir Malzemeler ve Özel Projeler İçin Uygulama Örnekleri
Hidroform preslerin kullanım alanları sadece standart yapı malzemeleri ile sınırlı değildir. Geri dönüşüm projeleri için çevre dostu yapı elemanları üretilmesinde de hidroform presler büyük bir katkı sağlar. Geri dönüştürülebilir atıklar, belirli oranlarda karıştırılarak yapı malzemesi üretiminde kullanılır ve bu malzemeler hidroform preslerde sıkıştırılarak yeni ürünler haline getirilir. Bu uygulama, çevreye duyarlı projelerde ve yeşil bina sertifikasyonuna sahip inşaat projelerinde büyük önem taşır.
Özellikle kentsel düzenleme projeleri ve peyzaj uygulamalarında, geri dönüştürülebilir malzemeler kullanılarak yapılan parke taşları veya bordür taşları gibi ürünler tercih edilir. Hidroform preslerin sağladığı yoğunluk ve dayanıklılık, bu ürünlerin dış etkenlere karşı uzun süre dayanmasını sağlar. Aynı zamanda, özel projeler için tasarlanan estetik amaçlı parke taşları veya şekilli yapı elemanları da hidroform presler sayesinde üretilir.
Hidroform Preslerle Üretilen Ürünler ve Kullanım Alanları
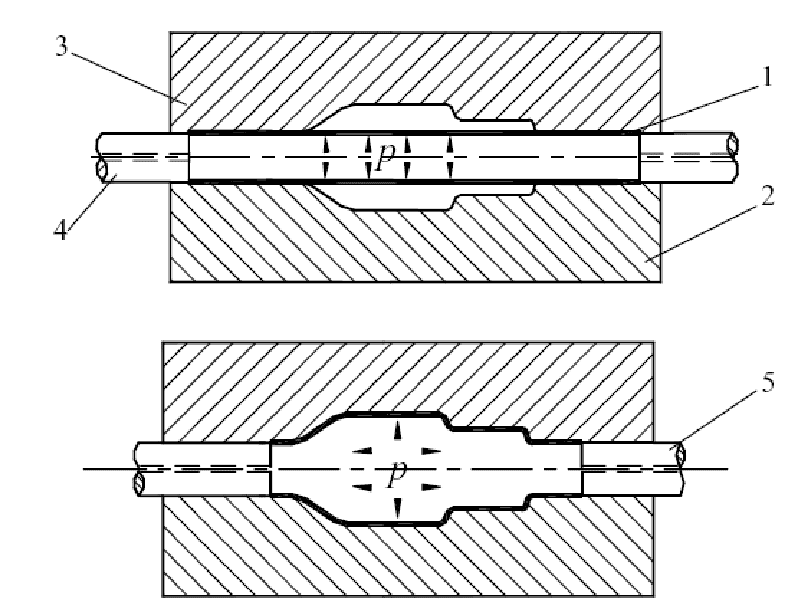
Hidroform Preslerle Üretilen Yapı Elemanları
Hidroform presler, yüksek basınç ve sıkıştırma kapasitesi sayesinde çeşitli yapı elemanları üretebilir. Bu elemanlar, dayanıklılık ve yoğunluk gerektiren projelerde kullanılmak üzere üretilir. Hidroform preslerle üretilen temel yapı elemanları şunlardır:
- Beton Bloklar: İnşaat sektöründe duvar örme, temel güçlendirme ve çeşitli taşıyıcı yapı elemanları için en yaygın kullanılan malzemelerden biridir. Hidroform preslerle üretilen beton bloklar, normal bloklara göre daha dayanıklıdır ve yüksek yoğunlukları sayesinde dış etkenlere karşı daha dirençlidir. Bu tür bloklar, konut, ticari binalar ve altyapı projelerinde sıklıkla kullanılır.
- Tuğlalar: Tuğlalar, binaların iç ve dış duvarlarında kullanılan temel yapı elemanlarıdır. Hidroform preslerin sağladığı yoğunluk ve homojenlik, tuğlaların dayanıklılığını artırır ve yapısal bütünlük sağlar. Tuğlalar ayrıca çeşitli estetik projelerde, mimari tasarımlarda da kullanılabilir.
- Parke Taşları: Hidroform preslerle üretilen parke taşları, peyzaj düzenlemeleri, bahçe yolları, yaya kaldırımları ve açık hava alanlarında kullanılır. Parke taşları, hem dayanıklı yapıları hem de dekoratif özellikleriyle projelere estetik bir katkı sunar.
- Bordür Taşları: Kaldırımlar ve peyzaj projelerinde kullanılan bordür taşları da hidroform preslerde üretilir. Bordür taşları, yolları ve yaya alanlarını ayırarak düzen sağlar. Hidroform preslerle üretilen bordürler, araç ve yaya trafiğine karşı dayanıklı oldukları için uzun süreli kullanıma uygundur.
- Özelleştirilmiş Yapı Elemanları: Hidroform presler, çeşitli kalıplar kullanılarak özelleştirilebilir yapı elemanları üretir. Örneğin, estetik amaçlı şekilli taşlar veya dekoratif bloklar gibi yapı elemanları, özel projelerde veya mimari tasarım gereksinimlerinde kullanılmak üzere üretilebilir. Bu esneklik, projelere özgünlük katar ve tasarımcılara geniş bir ürün yelpazesi sunar.
Hidroform Preslerin Tercih Edildiği Sektörler
Hidroform presler, inşaat sektörü başta olmak üzere çeşitli endüstrilerde yaygın olarak kullanılır. Bu makinelerin yüksek basınç kapasitesi ve dayanıklı ürünler sunması, hidroform preslerin tercih edilme sebeplerinin başında gelir. Kullanım alanlarını detaylandıracak olursak:
- İnşaat Sektörü: Konut, ticari bina, altyapı projeleri ve çok katlı yapılar gibi birçok inşaat projesinde dayanıklı yapı elemanlarına ihtiyaç vardır. Hidroform preslerle üretilen beton bloklar ve tuğlalar, binaların taşıyıcı elemanları olarak kullanılır ve yapısal güvenlik sağlar.
- Altyapı Projeleri: Yol yapımı, köprü, baraj ve tünel gibi altyapı projelerinde, yüksek dayanıklılığa sahip yapı elemanlarına ihtiyaç vardır. Hidroform preslerle üretilen bordür ve parke taşları, bu projelerde hem dayanıklılık hem de uzun ömür açısından önem taşır.
- Peyzaj ve Çevre Düzenleme: Parke taşları, dekoratif taşlar ve bordürler, peyzaj projelerinde ve çevre düzenlemelerinde sıklıkla tercih edilir. Hidroform presler, dış mekan koşullarına dayanıklı ve estetik açıdan uyumlu ürünler üreterek peyzaj projelerine katkı sağlar.
- Endüstriyel Yapı Projeleri: Fabrika ve depo gibi endüstriyel yapıların inşasında da hidroform preslerle üretilen dayanıklı yapı elemanları kullanılır. Bu tür yapılarda, özellikle ağır yük taşıma kapasitesine sahip beton bloklar ve bordürler tercih edilir.
Geniş Kullanım Alanları ve Esneklik Sağlayan Ürün Çeşitleri
Hidroform preslerin sunduğu ürün çeşitliliği, inşaat sektöründe esneklik ve çok yönlülük sağlar. Hidroform preslerle üretilen malzemeler, dayanıklılık, mukavemet ve estetik değer açısından yüksek performans gösterdiği için birçok farklı proje türünde kullanılabilir. Örneğin, estetik ve dayanıklılığı bir arada sunan dekoratif parke taşları, hem konut projelerinde hem de ticari alanlarda popülerdir. Ayrıca, farklı kalıplarla özelleştirilebilen yapı elemanları, projelerin ihtiyaçlarına göre üretilerek proje özgünlüğünü artırır.
Hidroform preslerin esnekliği, farklı boyutlarda, şekillerde ve dayanıklılık seviyelerinde ürün üretme imkanı sunar. Bu da hidroform presleri inşaat projelerinde vazgeçilmez hale getirir. Üretilen malzemeler, yüksek dayanıklılık standartlarına sahip olduğu için aşınma ve yıpranma oranı düşüktür; bu nedenle, özellikle uzun ömürlü projelerde hidroform preslerle üretilen ürünler tercih edilir.
Hidroform Preslerin Avantajları ve Faydaları
Yüksek Mukavemetli ve Dayanıklı Malzemeler Üretme İmkanı
Hidroform preslerin en büyük avantajlarından biri, yüksek mukavemetli ve dayanıklı yapı malzemeleri üretme kabiliyetidir. Bu makinelerde uygulanan yüksek basınç, malzemeleri yoğun bir yapıya dönüştürerek mukavemetlerini artırır. Hidroform preslerle üretilen beton bloklar, tuğlalar ve parke taşları, basınca ve çevresel etkenlere karşı oldukça dirençli hale gelir. Bu özellikleri sayesinde, hidroform presle üretilen yapı elemanları, yüksek dayanıklılık gerektiren projelerde tercih edilir. Örneğin, çok katlı binalarda veya altyapı projelerinde kullanılan beton blokların uzun ömürlü olması, yapıların genel güvenliğini artırır.
Dayanıklılık özellikleri sayesinde hidroform preslerle üretilen ürünler, hem bakım maliyetlerini düşürür hem de yapıların uzun süre güvenle kullanılmasını sağlar. Bu durum, özellikle altyapı projelerinde ve ağır yük taşıyan yapıların inşasında büyük avantaj sağlar.
Malzeme Yoğunluğu ve Homojenlik Sağlama
Hidroform preslerin sunduğu bir diğer önemli avantaj, malzeme yoğunluğunu artırma ve homojen bir yapı elde etme imkanıdır. Sıkıştırma işlemi sırasında malzeme içindeki hava boşlukları minimuma indirilir ve bu sayede malzemenin her bölgesi aynı yoğunluğa sahip olur. Bu özellik, yapı elemanlarının her noktasında eşit dayanıklılık ve mukavemet sağlar. Malzemenin homojen bir yapıya sahip olması, ürünün uzun ömürlü olmasına ve darbe, nem, sıcaklık değişimleri gibi çevresel etkenlere karşı daha dayanıklı hale gelmesine katkıda bulunur.
Homojenlik, özellikle zorlu çevresel koşullara maruz kalan yapı malzemeleri için kritik öneme sahiptir. Hidroform preslerle üretilen malzemeler, darbelere ve aşınmaya karşı dirençli bir yapıda olduklarından, özellikle yol yapımı, peyzaj projeleri ve yaya alanları gibi yoğun kullanılan alanlarda avantaj sağlar.
Enerji Tasarrufu ve Çevresel Avantajlar
Hidroform presler, yapı elemanlarının üretiminde enerji verimliliğini sağlayan makineler olarak öne çıkar. Hidrolik sistemlerin verimli bir şekilde kullanılması sayesinde daha az enerji harcanarak yüksek basınç elde edilir. Günümüzde enerji maliyetlerinin yükselmesi, inşaat sektöründe enerji tasarrufunun önemini artırmaktadır. Hidroform presler, düşük enerji tüketimi ile yüksek verim sağladığından, uzun vadede işletme maliyetlerinde tasarruf sağlar. Bu durum, büyük üretim tesisleri için büyük avantaj sunar.
Ayrıca, hidroform presler çevreye duyarlı projelerde de önemli bir rol oynar. Geri dönüştürülebilir malzemelerle çalışabilme özelliği, doğal kaynak kullanımını azaltır ve çevresel sürdürülebilirlik hedeflerine katkı sağlar. Özellikle yeşil bina sertifikalarına sahip projelerde, geri dönüştürülmüş malzemelerden üretilen yapı elemanları kullanılması tercih edilir. Bu sayede hidroform presler, çevre dostu inşaat projelerinin ayrılmaz bir parçası haline gelir.
Üretim Hızı ve Verimlilik
Hidroform preslerin sağladığı yüksek basınç kapasitesi, hızlı ve verimli üretim süreçlerine olanak tanır. Seri üretim imkanı sunan hidroform presler, büyük çaplı projeler için gereken yapı elemanlarının kısa sürede üretilmesini sağlar. Bu durum, inşaat projelerinin zamanında tamamlanmasına ve iş gücü maliyetlerinin düşmesine katkıda bulunur. Özellikle hızlı teslimat gerektiren projelerde, hidroform preslerin sağladığı üretim hızı ve verimlilik büyük bir avantaj sunar.
Ayrıca, hidroform preslerde kullanılan kalıpların değiştirilebilir olması, çeşitli yapı elemanlarının aynı presle üretilmesini sağlar. Bu esneklik, hem üretim süreçlerini hızlandırır hem de farklı yapı elemanlarının tek bir üretim hattında üretilmesini mümkün kılar.
Düşük Bakım Maliyetleri ve Uzun Ömür
Hidroform presler, dayanıklı malzemelerden üretilmiş ve uzun ömürlü olacak şekilde tasarlanmıştır. Hidrolik sistemlerin dayanıklılığı ve yüksek kaliteli bileşenler kullanılması, makinelerin uzun süre kesintisiz çalışmasını sağlar. Hidroform preslerin düşük arıza oranı ve kolay bakım özellikleri, işletmeler için önemli bir maliyet avantajı sunar. Hidrolik sistemlerde kullanılan parçaların dayanıklı olması ve aşınmaya karşı dirençli olması, bakım ihtiyaçlarını minimum seviyede tutar.
Uzun ömürlü hidroform presler, işletmelerin makineleri yenileme veya sık sık bakım yapma gereksinimini azaltarak maliyet tasarrufu sağlar. Ayrıca, presin çalışma ömrünün uzun olması, yatırım geri dönüş süresini kısaltır ve yüksek verimlilikle sürekli üretim yapma olanağı tanır.
Hidroform Pres Teknolojisinin Geleceği
İnşaat Sektöründe Hidroform Preslerin Artan Kullanımı
İnşaat sektöründe sürdürülebilirlik, dayanıklılık ve yüksek verimlilik gibi ihtiyaçların artması, hidroform preslerin gelecekteki önemini artırmaktadır. Hidroform preslerle üretilen yüksek dayanıklılığa sahip yapı elemanları, modern yapı projelerinde güvenliğin ve uzun ömürlülüğün garantisi olarak kabul edilmektedir. Bu durum, özellikle çok katlı binalar, altyapı projeleri, endüstriyel yapılar ve yeşil bina projelerinde hidroform preslere olan talebi artıracaktır.
Ayrıca, hidroform preslerin geri dönüştürülebilir malzemelerle çalışma kapasitesi, çevreye duyarlı projelerde bu makinelerin tercih edilmesine katkıda bulunacaktır. Çevresel sürdürülebilirlik ve ekolojik yapı tasarımlarının ön planda olduğu gelecekte, hidroform preslerin kullanımı daha da yaygınlaşacaktır. Bu presler, çevre dostu yapı malzemeleri üreterek yeşil bina sertifikasyonuna uygun projelerde önemli bir rol oynayacaktır.
Otomasyon ve Dijitalleşme ile Gelişen Hidroform Pres Teknolojisi
Endüstri 4.0 ile birlikte üretim süreçlerinde otomasyon ve dijitalleşme ön plana çıkmıştır. Hidroform presler de bu dönüşümden etkilenerek daha gelişmiş kontrol sistemleri ve dijital izleme mekanizmalarıyla donatılmaktadır. Akıllı sensörler, izleme sistemleri ve bilgisayar destekli yönetim sistemleri, hidroform preslerin üretim süreçlerini optimize etmelerine olanak tanır. Bu sayede, basınç, sıcaklık, hız gibi parametreler anlık olarak kontrol edilip ayarlanabilir, bu da daha yüksek verimlilik sağlar.
Otomasyon ve dijitalleşme, hidroform preslerin bakım sürecini de kolaylaştırmaktadır. Arıza tespiti ve önleyici bakım özellikleri, preslerin sürekli izlenmesi ve çalışma durumlarının anında değerlendirilmesini mümkün kılar. Bu özellikler, makinelerin arıza süresini en aza indirirken, bakım maliyetlerini de düşürür. Gelecekte, akıllı hidroform presler sayesinde üretim süreçleri daha hızlı, güvenilir ve maliyet açısından verimli hale gelecektir.
Sürdürülebilir Yapı Malzemeleri Üretiminde Hidroform Preslerin Rolü
Gelecekte hidroform preslerin en önemli katkılarından biri, sürdürülebilir yapı malzemeleri üretme kapasitesidir. Hidroform preslerin geri dönüştürülebilir malzemeleri kullanarak dayanıklı yapı elemanları üretebilmesi, doğal kaynak kullanımını azaltır. Bu durum, inşaat sektöründe çevresel duyarlılığın arttığı bir dönemde hidroform preslerin önemini artıracaktır. Çevre dostu malzemeler, inşaat projelerinde karbon ayak izini azaltırken, doğal kaynakların korunmasına da katkı sağlar.
Sürdürülebilir yapı projelerine duyulan ihtiyaç, hidroform preslerin yaygın kullanımını desteklerken, çevresel hedeflere katkı sağlayan inovasyonlar geliştirilmesine de öncülük edecektir. Gelecekte, hidroform preslerle üretilen yapı elemanları, çevre dostu projeler ve yeşil bina standartlarına uyum sağlamak amacıyla tercih edilen ürünler haline gelecektir.
Hidroform Preslerin Gelecek Perspektifi
Özetle, hidroform presler gelecekte inşaat sektöründe dayanıklılık, verimlilik ve çevresel sürdürülebilirlik hedeflerini karşılayan temel bir teknoloji olarak kalmaya devam edecektir. Dijitalleşme ve otomasyon teknolojileri ile gelişen hidroform presler, daha hassas üretim süreçleri, düşük enerji tüketimi ve çevre dostu üretim kapasitesi sunarak yapı sektöründe fark yaratacaktır. Aynı zamanda, özel projeler için özelleştirilebilir yapı elemanları sunan hidroform presler, mimarlara ve tasarımcılara esnek ve yenilikçi çözümler sağlayacaktır.
Sonuç olarak, hidroform presler, yapı sektöründeki sürdürülebilirlik hedeflerine katkı sunan, dayanıklı, çevre dostu ve verimli bir çözüm olarak kalıcılığını sürdürecektir.
Hidrolik sıvama presi
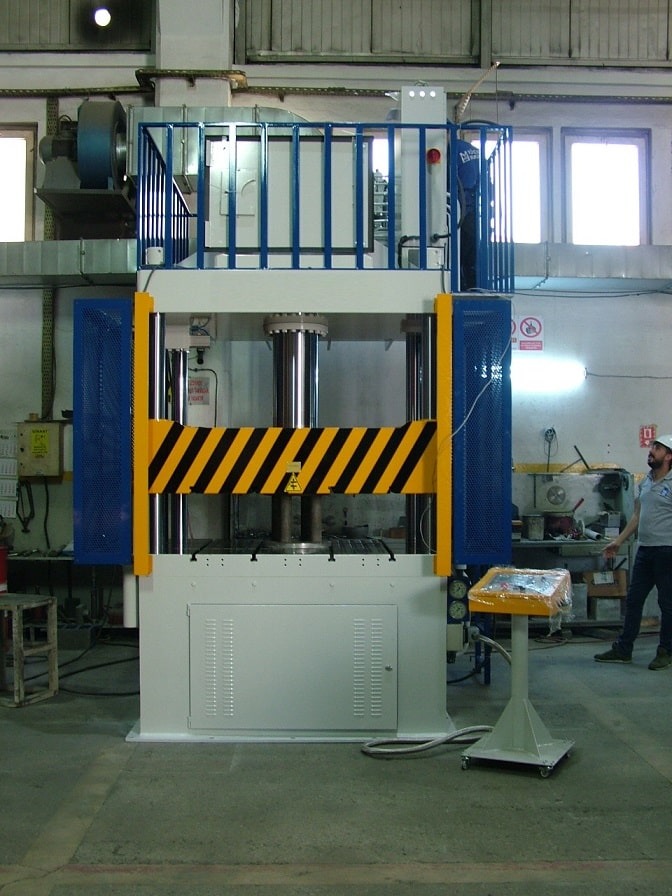
Hidrolik sıvama presi, metal şekillendirme teknolojilerinde önemli bir yer tutan, özellikle sac metal parçaların karmaşık ve derin geometrilere dönüştürülmesinde kullanılan güçlü bir üretim makinesidir. Bu pres türü, yüksek basınç altında çalışan hidrolik silindirler yardımıyla metali bir kalıba bastırarak istenilen formu elde etmeye dayanır. Özellikle otomotiv, beyaz eşya, havacılık, mutfak ekipmanları ve aydınlatma sanayi gibi sektörlerde geniş bir kullanım alanı bulur.
Sıvama işlemi (diğer adıyla “deep drawing”), düz bir sac metal parçasının, sıvama zımbası yardımıyla kalıp içine çekilerek üç boyutlu bir forma dönüştürülmesidir. Bu işlemde sacın et kalınlığı genellikle sabit kalır, ancak şekli büyük ölçüde değişir. Hidrolik sıvama presleri, bu işlemi kontrollü ve tekrarlanabilir şekilde gerçekleştirmek için idealdir. Çünkü hidrolik sistemler, uygulanan kuvveti hassas bir şekilde kontrol etme kabiliyeti sunar ve uzun strok mesafeleri sayesinde derin sıvamalarda üstün performans sağlar.
Hidrolik sıvama preslerinin en büyük avantajlarından biri, çok yüksek tonajlarda kuvvet üretebilmesidir. Bu özellik, özellikle kalın ve dayanıklı metalleri şekillendirmek için gereklidir. Ayrıca, presleme hızı ayarlanabilir olduğundan, farklı malzemelere ve ürün geometrilerine uygun şekilde optimize edilebilir. Bu makinelerde genellikle aşağı yukarı hareket eden bir ana piston ve ona karşı çalışan bir alt yastık sistemi bulunur. Yastık sistemi, sıvama sırasında sacın buruşmasını önlemek için kontrollü bir karşı kuvvet uygular.
Günümüzde modern hidrolik sıvama presleri, otomatik sac besleme sistemleri, PLC kontrollü işlemler, sensörler ve insan-makine arayüzleri (HMI) ile donatılmıştır. Bu teknolojiler sayesinde hem üretim verimliliği artar hem de hata oranı azalır. Özellikle seri üretim hatlarında, bu presler robotik sistemlerle entegre edilerek tam otomatik hatlar oluşturulabilir. Bu da hem zaman hem de işçilik maliyetlerinde önemli tasarruflar sağlar.
Malzeme açısından değerlendirildiğinde, alüminyum, paslanmaz çelik, pirinç gibi şekillendirilebilir ve aynı zamanda yüksek dayanım gerektiren metaller, hidrolik sıvama preslerinde yaygın olarak kullanılır. Ürünler arasında tencere gövdeleri, otomobil kapı içi panelleri, lambalar için reflektör kasaları ve endüstriyel kaplar yer alır. Ayrıca, hassas yüzey kalitesi ve boyutsal doğruluk gerektiren ürünler için de bu pres türü oldukça uygundur.
Özetle, hidrolik sıvama presleri; yüksek kuvvet kapasitesi, kontrollü hareket kabiliyeti ve modern otomasyon sistemlerine entegrasyon kolaylığı sayesinde, hassas ve karmaşık metal şekillendirme işlemlerinde vazgeçilmez bir üretim ekipmanıdır. Sıvama teknolojisinin gelişmesiyle birlikte bu presler de daha esnek, daha hızlı ve daha güvenli hale gelmekte, sanayideki üretim kalitesini bir üst seviyeye taşımaktadır.
Hidrolik sıvama preslerinin kullanım alanlarının genişlemesiyle birlikte, makinelerin tasarımı ve performans beklentileri de önemli ölçüde gelişmiştir. Artık sadece yüksek tonajlı presleme kapasitesi yeterli olmamakta, aynı zamanda enerji verimliliği, bakım kolaylığı ve üretim esnekliği de öne çıkmaktadır. Bu bağlamda, modern hidrolik sıvama preslerinde servo motor destekli hidrolik sistemler, düşük enerji tüketimiyle daha sürdürülebilir bir üretim sağlar. Ayrıca bu sistemler, daha düşük ısınma, daha az yağ kullanımı ve daha uzun ekipman ömrü gibi avantajlar sunar.
Preslerde kullanılan kalıp sistemleri de sıvama işleminin başarısı açısından kritik öneme sahiptir. Kalıp tasarımı, sacın kırışmadan, çatlamadan ve deformasyona uğramadan şekillenmesini sağlamak zorundadır. Özellikle derin sıvama işlemlerinde, sacın kalıp içine düzgün şekilde çekilebilmesi için sacın belirli noktalardan yağlanması ya da ısıtılması gerekebilir. Bu nedenle, üretim hattının sıvama öncesi ve sonrası süreçleri de dikkatli şekilde planlanmalıdır.
Hidrolik sıvama presi ile çalışan operatörler ya da üretim mühendisleri açısından, makinenin kontrol paneli büyük önem taşır. Günümüzde kullanılan dokunmatik ekranlı HMI paneller üzerinden; strok ayarı, basınç seviyesi, bekleme süreleri ve geri dönüş hızları gibi parametreler kolayca ayarlanabilmekte ve kaydedilebilmektedir. Bu özellik, farklı ürünler için önceden belirlenmiş programların hızlı bir şekilde seçilmesine olanak tanır. Böylece bir üründen diğerine geçiş süresi en aza iner ve üretim hattının verimliliği artar.
Güvenlik açısından da hidrolik sıvama presleri oldukça gelişmiştir. İki elle çalıştırma sistemleri, ışık perdeleri, acil durdurma butonları ve kapak sensörleri gibi önlemlerle operatör güvenliği maksimum seviyeye çıkarılmıştır. Özellikle büyük tonajlı preslerde bu güvenlik sistemlerinin düzenli olarak test edilmesi ve bakımının yapılması, iş kazalarının önüne geçilmesi açısından hayati öneme sahiptir.
Sanayideki dijitalleşme trendiyle birlikte, hidrolik sıvama presleri artık üretim takip sistemlerine entegre edilebilmekte, proses verileri dijital olarak kaydedilmekte ve uzaktan izleme imkânı sunulmaktadır. Bu da işletmelere arıza öncesi bakım planlaması yapma, üretim kalitesini izleme ve genel ekipman verimliliğini (OEE) analiz etme şansı verir. Özellikle seri üretim yapan işletmelerde, bu tür veriye dayalı karar alma mekanizmaları büyük rekabet avantajı sağlar.
Sonuç olarak, hidrolik sıvama presi yalnızca bir metal şekillendirme makinesi değil, aynı zamanda modern üretimin temel taşlarından biridir. Yüksek hassasiyet, güvenilirlik, enerji tasarrufu ve otomasyon kabiliyeti gibi unsurlar, bu presleri yalnızca bugünün değil, geleceğin üretim ihtiyaçlarına da yanıt verebilecek kapasitede bir teknoloji haline getirmiştir. Sıvama presleri sayesinde daha hafif, daha sağlam ve daha estetik ürünler üretmek mümkün hale gelmiş; bu da hem ürün kalitesini hem de marka değerini önemli ölçüde artırmıştır.
Hidrolik sıvama preslerinin geleceği, gelişen malzeme teknolojileri ve üretim sistemleriyle birlikte daha da önem kazanmaktadır. Özellikle hafif ama dayanıklı malzemelere olan talep arttıkça, titanyum, magnezyum alaşımları ve gelişmiş yüksek dayanımlı çelikler gibi yeni nesil sac malzemelerin sıvanması da ön plana çıkmaktadır. Bu tür malzemeler genellikle geleneksel yöntemlerle şekillendirilmesi zor olan, yüksek yaylanma sınırlarına sahip yapılardır. Ancak modern hidrolik sıvama presleri, yüksek basınç, hassas kontrol ve özel kalıplarla bu zorlukları aşarak ileri düzey çözümler sunar.
Özellikle otomotiv sektöründe hafif malzemelerle araç ağırlığını düşürme hedefi, sıvama teknolojisinin çok daha stratejik hale gelmesine neden olmuştur. Hafiflik, hem yakıt verimliliği hem de emisyon kontrolü açısından önemlidir. Aynı zamanda elektrikli araç üretiminde kullanılan batarya kutuları, termal koruyucular ve çeşitli gövde parçaları da hidrolik sıvama ile yüksek hassasiyetle üretilebilmektedir. Bu yönüyle pres teknolojisi, çevreci ve sürdürülebilir üretim anlayışının bir tamamlayıcısı haline gelmiştir.
Beyaz eşya sektöründe ise hidrolik sıvama presleri, özellikle çamaşır makinesi kazanları, iç tamburlar, su tankları, kapaklar ve ocak yüzeyleri gibi parçaların üretiminde kritik rol oynamaktadır. Parçalarda hem yüksek dayanıklılık hem de estetik yüzey kalitesi arandığı için sıvama presleri, metal yüzeylerde dalga, buruşma, çatlama gibi istenmeyen etkileri minimize ederek mükemmele yakın sonuçlar verir.
Yüksek üretim hacmine sahip işletmelerde, preslerin çok istasyonlu olarak yapılandırılması mümkündür. Çok istasyonlu sistemlerde, sıvama işlemi birkaç aşamada gerçekleştirilir ve bu sayede daha karmaşık geometriler elde edilebilir. Bu tür sistemlerde sac metal, her adımda bir miktar daha şekillendirilir ve nihayetinde istenen üç boyutlu forma ulaşır. Çok istasyonlu pres hatları, otomatik transfer sistemleriyle çalıştırıldığında hem çevrim süresi düşer hem de işçilik ihtiyacı minimuma iner.
Ayrıca, preslerin bakım süreçleri de üretim sürekliliği açısından hayati öneme sahiptir. Hidrolik sistemlerde meydana gelebilecek kaçaklar, filtre tıkanmaları veya sensör arızaları, erken tespit edilmezse ciddi üretim aksaklıklarına yol açabilir. Bu nedenle modern preslerde kullanılan akıllı bakım sistemleri sayesinde, makineye entegre edilen sensörler yağ seviyesi, sıcaklık, basınç ve titreşim gibi parametreleri sürekli izler ve operatörü uyarır. Bu sayede plansız duruşlar azalır, üretim güvenliği artar.
Son olarak, eğitimli personelin bu makineleri verimli şekilde kullanabilmesi de önemli bir gerekliliktir. Operatörlerin, hem makine kontrolleri hem de sac şekillendirme prensipleri hakkında yeterli bilgiye sahip olması, hem ürün kalitesini artırır hem de makine ömrünü uzatır. Bu nedenle, işletmelerin hidrolik sıvama presleriyle çalışacak ekiplerini düzenli olarak eğitmesi, kalite ve verimlilik açısından büyük avantaj sağlar.
Genel olarak değerlendirildiğinde, hidrolik sıvama presi teknolojisi; dayanıklı, hafif, karmaşık ve yüksek yüzey kalitesi gerektiren parçaların üretiminde sağladığı esneklik ve yüksek hassasiyet sayesinde, modern üretimin vazgeçilmez unsurlarından biri haline gelmiştir. Teknolojik gelişmelerle birlikte daha da entegre, akıllı ve enerji verimli hale gelen bu makineler, endüstriyel üretimin hem bugünü hem de geleceği için stratejik bir konuma sahiptir.
1. Hidrolik Sıvama Presinin Temel Çalışma Prensibi
Hidrolik sıvama presi, sac metalin kalıp içerisine çekilerek derin ve karmaşık formlara dönüştürülmesini sağlayan bir şekillendirme makinesidir. Yüksek tonajlı hidrolik kuvvetle çalışan bu sistem, hassas kontrollü presleme yaparak sacın buruşmadan veya çatlamadan şekil almasını sağlar.
2. Kullanım Alanları ve Endüstriyel Uygulamalar
Bu presler otomotiv, beyaz eşya, havacılık, mutfak eşyaları ve aydınlatma gibi birçok sektörde kullanılır. Özellikle otomobil kaplamaları, çamaşır makinesi tamburları, tencere gövdeleri ve reflektör kasaları gibi hassas ve dayanıklı parça üretiminde tercih edilir.
3. Modern Teknolojik Özellikler ve Otomasyon
Günümüz presleri, dokunmatik kontrol panelleri (HMI), PLC sistemleri, servo hidrolik teknolojiler ve robotik otomasyonla donatılmıştır. Bu sistemler sayesinde enerji tasarrufu sağlanır, üretim esnekliği artar ve insan hataları azaltılır.
4. Malzeme Uyumluğu ve Kalıp Sistemleri
Hidrolik sıvama presleri, alüminyum, paslanmaz çelik, yüksek dayanımlı çelikler gibi çeşitli malzemeleri şekillendirebilir. Kalıp tasarımı, sacın şekil alırken buruşmaması ve çatlamaması için kritik öneme sahiptir. Yağlama ve çok istasyonlu sıvama sistemleriyle karmaşık parçalar üretilebilir.
5. Bakım, Güvenlik ve Operatör Eğitimi
Pres sistemlerinin uzun ömürlü ve güvenli çalışması için düzenli bakım gereklidir. Akıllı sensörlerle donatılmış sistemler, yağ seviyesi, basınç ve sıcaklık gibi parametreleri izleyerek arızaları önceden bildirir. Ayrıca operatörlerin eğitimi, hem üretim kalitesini artırır hem de iş güvenliğini sağlar.
Hidrolik sıvama presinin temel çalışma prensibi, sac metal malzemelerin yüksek basınç altında şekillendirilmesine dayanır. Bu işlemde, düz bir sac parçası, bir zımba yardımıyla bir kalıbın içine doğru itilerek derin ve genellikle silindirik ya da karmaşık geometrili bir forma dönüştürülür. İşlem sırasında sac, kalıp yüzeyine doğru akar ve kalıbın şekline uyum sağlar. Bu şekillendirme işlemi, plastik deformasyon prensiplerine dayanır; yani metal, elastik sınırını aşarak kalıcı şekilde şekil değiştirir.
Hidrolik sıvama preslerinde esas güç kaynağı hidrolik sistemdir. Bu sistemde, hidrolik silindirler aracılığıyla yüksek basınçlı yağ kullanılarak lineer hareket sağlanır. Ana silindir, zımbayı aşağıya doğru iterken, aynı anda alt kısımdaki yastık sistemi sacı yukarıdan destekler. Bu karşı kuvvet, sıvama sırasında sacın buruşmasını veya yırtılmasını önler. Böylece hem düzgün bir şekil elde edilir hem de malzemenin yüzey kalitesi korunur.
Presin kalıpları genellikle iki ana parçadan oluşur: sabit olan kalıp (dişi kalıp) ve hareketli olan zımba (erkek kalıp). Zımba, sacı aşağı doğru bastırarak malzemeyi kalıp boşluğuna iter. Sacın kenarları, kenetleme kuvveti uygulanarak kontrollü şekilde tutulur. Bu kuvvet, sacın serbestçe kaymasını engelleyerek düzgün bir akış sağlar. Bu aşamada hidrolik sistemin basıncı ve hareket hızı son derece önemlidir. Fazla basınç, sacın yırtılmasına; düşük basınç ise form eksikliğine yol açabilir.
Hidrolik sıvama preslerinin en önemli avantajlarından biri, kuvvetin ve hareketin hassas bir şekilde kontrol edilebilmesidir. Bu sayede pres operatörü veya otomasyon sistemi, farklı malzeme türlerine ve ürün geometrilerine uygun basınç ve hız ayarları yapabilir. Örneğin ince duvarlı alüminyum parçalar için daha düşük basınç ve yavaş ilerleme gerekliyken, kalın paslanmaz çelik için yüksek kuvvet ve daha sert bir sıvama gerekebilir.
Sıvama işleminin bir diğer önemli unsuru da strok kontrolüdür. Hidrolik sistemlerde strok, yani zımbanın aşağı doğru hareket mesafesi, istenilen ürün derinliğine göre ayarlanabilir. Derin sıvama işlemleri için uzun stroklar gerekirken, daha sığ parçalar için kısa stroklarla daha hızlı bir çevrim süresi elde edilir. Bu özelliği sayesinde hidrolik sıvama presleri, hem derin hem de sığ sıvamalarda yüksek verimlilikle çalışabilir.
Yastık sistemi (blank holder veya counter-pressure system), sıvama işleminde büyük rol oynar. Bu sistem, sacın etrafına uygulanan kuvveti dengeler ve sacın kontrollü bir şekilde zımba tarafından kalıp içine çekilmesini sağlar. Yastık basıncı, sacın türüne, kalınlığına ve ürün geometrisine göre ayarlanabilir. Eğer yastık kuvveti çok düşükse, sac buruşur veya kırışır; çok yüksekse sacın içeri çekilmesi zorlaşır ve çatlamalara yol açabilir.
Sonuç olarak, hidrolik sıvama presinin temel çalışma prensibi; yüksek basınçlı hidrolik sistemle çalışan bir zımba yardımıyla sacın kalıp içine çekilerek istenilen forma getirilmesine dayanır. İşlem boyunca basınç, strok, hız ve yastık kuvveti gibi birçok parametre, ürün kalitesini ve üretim başarısını doğrudan etkiler. Bu nedenle bu preslerin hassas ayarlanabilirliği ve geniş uygulama yelpazesi, onları endüstriyel üretimin vazgeçilmez bir parçası haline getirmiştir.
Hidrolik sıvama preslerinin çalışma prensibine dair süreci daha derinlemesine anlamak için, şekillendirme sırasında gerçekleşen metal akış davranışına da değinmek gerekir. Sıvama işlemi sırasında sac metal, kalıp kenarlarından merkez bölgeye doğru kontrollü bir şekilde akar. Bu akış, plastik deformasyon süreciyle gerçekleştiğinden, malzemenin sünekliği bu noktada büyük önem taşır. Sünekliği düşük olan metaller daha kolay çatlama eğilimi gösterir. Bu nedenle işlem öncesi doğru malzeme seçimi ve uygun sıvama parametreleri belirlenmelidir.
Presin kontrolü genellikle elektro-hidrolik sistemlerle sağlanır. Bu sistemler sayesinde zımbanın hareketi mikrometre seviyesinde hassasiyetle kontrol edilebilir. Bu durum, özellikle yüksek hassasiyetli parçaların üretiminde büyük avantaj sağlar. Aynı zamanda, sıvama esnasında çeşitli sensörler aracılığıyla basınç, konum ve hız verileri anlık olarak izlenir. Geri beslemeli bu sistemler sayesinde presin hareketi gerçek zamanlı olarak düzeltilebilir; böylece ürün kalitesinde süreklilik sağlanır.
Çok istasyonlu hidrolik sıvama preslerinde, şekillendirme işlemi birden fazla adımda gerçekleşebilir. Bu yöntem, özellikle karmaşık ve derin formların daha az gerilme birikimiyle şekillendirilmesini sağlar. İlk aşamada ön şekillendirme yapılır, ardından nihai sıvama gerçekleştirilir. Bu çok kademeli yapı, yırtılma veya kırışma riskini azaltırken daha net ve düzgün bir yüzey kalitesi sunar. Bu tür sistemlerde her istasyon ayrı bir zımba-kalıp kombinasyonuna sahiptir ve parçanın ilerlemesi otomatik transfer mekanizmalarıyla sağlanır.
Bazı özel uygulamalarda, sıvama işlemi ısıtılmış sacla birlikte de uygulanabilir. “Sıcak sıvama” olarak bilinen bu yöntem, özellikle yüksek mukavemetli çelikler gibi zor şekillenen malzemeler için kullanılır. Sac, önceden belirli bir sıcaklığa kadar ısıtılır ve ardından preslenir. Bu işlem, metalin daha kolay akmasını sağlar ve çatlama riskini azaltır. Ancak sıcak sıvama süreçleri, hem kalıp hem de pres sistemleri açısından daha karmaşık ve maliyetlidir.
Gürültü seviyesi açısından bakıldığında, hidrolik sıvama presleri mekanik preslere göre daha sessiz çalışır. Bu da özellikle kapalı atölyelerde ve çalışan sağlığı açısından önemli bir avantajdır. Ayrıca, hidrolik sistemlerin ani darbe yerine yumuşak ve dengeli bir hareket sağlaması, kalıp ömrünü uzatır ve parça yüzey kalitesini olumlu etkiler.
Enerji tüketimi bakımından ise klasik hidrolik sistemler yüksek güç ihtiyacıyla çalışsa da, modern enerji tasarruflu hidrolik üniteler ve servo-hidrolik sistemler sayesinde bu tüketim ciddi ölçüde azaltılmıştır. Pres yalnızca gerektiğinde tam güçle çalışır, boşta veya düşük yükteyken enerji kullanımı en aza iner. Bu da işletmeler için hem çevreci hem de ekonomik bir üretim avantajı yaratır.
Sonuç olarak, hidrolik sıvama presinin çalışma prensibi yalnızca zımbanın sacı aşağı doğru bastırmasından ibaret değildir. Bu süreç; sacın akış kontrolü, karşı basınç ayarı, strok hassasiyeti, malzeme tepkimesi ve sistem izleme gibi çok sayıda değişkenin bir araya gelerek uyum içinde çalışmasını gerektirir. Bu nedenle hidrolik sıvama presleri, mühendislik açısından hem güçlü bir üretim aracı hem de karmaşık bir sistem bütünüdür. İyi tasarlanmış ve doğru parametrelerle çalışan bir sıvama presi, yüksek hassasiyetli, dayanıklı ve estetik parçaların üretiminde kilit rol oynar.
Hidrolik sıvama preslerinin çalışma prensibi kapsamında bir diğer önemli konu da kalıp tasarımıdır. Kalıplar, sıvama işleminin başarısını doğrudan etkileyen unsurlardır. Kalıbın geometrisi, yüzey kalitesi, kenar radyüsleri, zımba-kalıp arasındaki boşluk miktarı gibi detaylar; hem ürünün estetik kalitesini hem de şekillendirme sırasında ortaya çıkabilecek hataları belirler. Örneğin, kalıp radyüsleri çok keskinse sac kolayca çatlayabilir; çok yuvarlaksa buruşma eğilimi artabilir. Bu nedenle her malzeme ve ürün tipi için özel olarak tasarlanmış kalıplar gerekir.
Bununla birlikte, malzeme özellikleri de çalışma prensibi üzerinde belirleyicidir. Sacın kalınlığı, mukavemeti, tane yapısı, sünekliği ve yüzey kalitesi; sıvama sırasında nasıl davranacağını etkiler. Örneğin, paslanmaz çelik gibi sert ve yaylanma eğilimi yüksek malzemeler için daha yüksek basınçlar ve özel yastık kuvvetleri gerekebilir. Buna karşın alüminyum gibi daha yumuşak metaller, daha düşük kuvvetlerle kolayca sıvanabilir, ancak yüzey deformasyonuna daha yatkındır. Bu farklılıklar, presin kontrol parametrelerinin de her malzemeye özel olarak ayarlanmasını zorunlu kılar.
Çalışma sırasında presin her döngüsünde meydana gelen ısınma, hidrolik sistemin performansını etkileyebilir. Yağın sıcaklığındaki artış, sistemin basınç üretme kapasitesini düşürebilir ve kaçak riskini artırabilir. Bu nedenle kaliteli sıvama preslerinde hidrolik yağ soğutma sistemleri ve sıcaklık izleme sensörleri bulunur. Ayrıca, presin devamlı yüksek basınç altında çalışması durumunda, yağ viskozitesi zamanla değişebilir. Bu da sistemin hassasiyetini etkileyebilir. Bu gibi durumların önüne geçmek için hem hidrolik yağ hem de sistem elemanları (filtreler, hortumlar, contalar vb.) belirli periyotlarla kontrol edilmelidir.
Presin uzun süreli ve güvenilir çalışması için senkronizasyon çok önemlidir. Özellikle büyük ebatlı parçaların üretiminde, tabla üzerinde eşit kuvvet dağılımı sağlanmalıdır. Eğer zımba hareketi dengesizse veya tabla bir köşeden daha önce kuvvet uyguluyorsa, ürün asimetrik şekilde şekillenebilir, hatta kalıp kırılabilir. Bu nedenle çift veya dört köşeli silindir sistemlerinde, silindirlerin senkronize hareket etmesini sağlayan özel valf ve kontrol sistemleri kullanılır. Bu tür sistemler, presin her vuruşunda hassas, eş zamanlı ve dengeli bir şekillendirme sağlar.
Ayrıca, üretim güvenliği açısından operatör-makine etkileşimi büyük önem taşır. Preslerde bulunan iki elle başlatma, ışık perdeleri, güvenlik kilitleri ve acil durdurma sistemleri, operatörün yanlışlıkla elini hareketli bölgeye sokmasını engeller. Bazı preslerde, HMI panelden sadece yetkili kişilerin erişebildiği şifreli alanlar bulunur. Bu alanlarda basınç, strok, geri dönüş hızı gibi hayati parametreler ayarlanır. Böylece sadece eğitilmiş kişiler sistemde kritik değişiklikler yapabilir.
Son olarak, hidrolik sıvama preslerinin çalışma prensibi, yalnızca mekanik ve hidrolik düzenekten ibaret değildir. Bu presler, akıllı üretim sistemlerine entegrasyon açısından da günümüzde ciddi bir avantaja sahiptir. Endüstri 4.0 kapsamında geliştirilen çözümlerle, presin üretim verileri (çevrim süresi, basınç eğrileri, arıza geçmişi, parça adedi gibi) anlık olarak izlenebilir, analiz edilebilir ve merkezi üretim kontrol sistemlerine aktarılabilir. Bu sayede hem üretim takibi kolaylaşır hem de arıza öncesi bakım planlamaları yapılabilir.
Özetle, hidrolik sıvama presinin çalışma prensibi; yüksek basınçla metalin kalıp içerisine çekilmesi gibi basit bir temele dayansa da, arkasında çok sayıda parametre, kontrol sistemi, güvenlik önlemi ve mühendislik detayı barındırır. Bu makinelerin verimli, güvenli ve kaliteli çalışabilmesi için tüm bu bileşenlerin birbirini tamamlayan bir bütün olarak uyum içinde çalışması gerekir. Bu nedenle hidrolik sıvama presleri, sadece güçlü değil, aynı zamanda yüksek hassasiyetli, güvenli ve akıllı üretim sistemlerinin de merkezinde yer alır.
Hidrolik sıvama preslerinin çalışma prensibini bütüncül olarak anlamak için, işlemin farklı üretim hedefleri doğrultusunda nasıl özelleştirilebildiğini de değerlendirmek gerekir. Her ürün tipi için gerekli sıvama derinliği, şekil karmaşıklığı, malzeme özellikleri ve yüzey kalitesi gibi unsurlar, presin konfigürasyonunu doğrudan etkiler. İşte bu noktada devreye “uyarlanabilir proses kontrolü” girer. Modern hidrolik sıvama presleri, üretim boyunca dinamik olarak ayarlanabilen parametrelerle çalışır. Bu da presin, değişken üretim şartlarına anında cevap verebilmesini sağlar.
Bu uyarlanabilirlik; sıvama basıncı, zımbanın iniş hızı, bekleme süreleri, yastık basıncı gibi faktörlerin gerçek zamanlı olarak kontrol edilmesiyle mümkündür. Örneğin, sac malzeme kalınlığında küçük bir sapma bile sıvama performansını etkileyebilir. Bu gibi durumlarda sistemde bulunan basınç ve pozisyon sensörleri, presin kendini otomatik olarak yeni duruma göre ayarlamasını sağlar. Bu esneklik, özellikle düşük toleransla çalışan sektörlerde (örneğin otomotiv ve havacılık) çok kritiktir.
Hidrolik sıvama işlemi sırasında, sacın kenar bölgelerinde malzeme birikimi veya incelme oluşabilir. Bu, sacın kalıp boşluğuna doğru çekilirken yaşadığı gerilme ve akma davranışına bağlıdır. Malzeme akışının düzgün olması, presin doğru parametrelerde çalışmasına bağlıdır. Akışın kontrolsüz olması, özellikle derin sıvamalarda ya da ince saclarda, parçada gözle görülür kusurlar doğurur. Bu yüzden sıvama preslerinin kontrol sistemleri yalnızca hareketi değil, aynı zamanda gerilme dağılımını da dolaylı olarak kontrol eder.
Deneme ve prototipleme aşamaları, hidrolik sıvama presinin çalışma prensibinde ayrı bir yer tutar. Yeni bir ürün geliştirilirken kalıp tasarımı, pres ayarları ve sac tipi üzerinde çeşitli testler yapılır. Deneme üretimleri sayesinde en uygun sıvama parametreleri belirlenir. Bu denemelerde presin sunduğu ayarlanabilirlik, kullanıcıya büyük avantaj sağlar. Aynı makine üzerinde farklı geometri ve farklı malzeme testleri yapılabilir, bu da geliştirme sürecini hem hızlandırır hem maliyetleri düşürür.
Hidrolik sıvama preslerinin işleyişinde, geri dönüş hareketi de en az presleme kadar önemlidir. Pres zımbası, sıvama işlemini tamamladıktan sonra geri çekilirken parçanın kalıptan düzgün şekilde ayrılması gerekir. Bu aşamada geri çekilme hızı, zımbanın yavaşlatılması veya ani geri çekilmeden kaçınılması gibi detaylar önemlidir. Çünkü ani geri çekilme, parçada deformasyon yaratabilir ya da parçanın kalıpta sıkışmasına neden olabilir. Bu nedenle geri dönüş aşaması da sistemin kontrol algoritması içinde yer alır ve hassas şekilde ayarlanabilir.
Ayrıca bazı gelişmiş sistemlerde, geri beslemeli kontrol döngüsü sayesinde pres hareketi, gerçek zamanlı olarak izlenerek anlık düzeltmeler yapılır. Bu, örneğin basınç eğrisinin önceden tanımlanan bir referans profil ile eşleşip eşleşmediğinin sürekli kontrol edilmesini sağlar. Böylece olası sapmalar presin bir sonraki döngüsünde otomatik olarak düzeltilir. Bu teknoloji, yüksek hassasiyetli üretimlerde kalite tutarlılığı açısından büyük önem taşır.
Tüm bu süreçlerin işleyişinde, insan-makine etkileşimi merkezi bir rol oynar. Operatör, dokunmatik ekranlar aracılığıyla presin tüm hareketlerini izleyebilir, arıza uyarıları alabilir, üretim sayacı gibi verileri görebilir. Ayrıca sistemlerde yer alan kayıt modülleri sayesinde, yapılan her üretim döngüsüne ait basınç, süre ve konum verileri dijital olarak arşivlenebilir. Bu bilgiler kalite kontrol sürecinde izlenebilirlik sağlar ve olası hata nedenlerini analiz etme imkânı sunar.
Son olarak, hidrolik sıvama presinin bu karmaşık fakat kontrollü çalışma sistemi, onu geleneksel mekanik preslere kıyasla çok daha esnek, güvenilir ve modern üretim sistemlerine uygun hale getirir. Özellikle küçük-orta üretim serilerinde, değişken ürün yapılarında ve prototip geliştirme aşamalarında bu preslerin sunduğu ayarlanabilirlik ve hassasiyet, büyük bir rekabet avantajı sağlar.
Bu prensipler ışığında değerlendirildiğinde, hidrolik sıvama presi yalnızca bir kuvvet makinesi değil; yüksek teknolojiyle donatılmış, hassas, veri odaklı ve operatörle bütünleşmiş bir üretim sistemidir. Mükemmel sonuçlar almak için sadece güçlü değil, aynı zamanda akıllı çalışan bu sistemlerin, endüstriyel üretimdeki rolü her geçen gün daha da artmaktadır.
Kullanım Alanları ve Endüstriyel Uygulamalar
Hidrolik sıvama preslerinin kullanım alanları ve endüstriyel uygulamaları, günümüzün gelişmiş üretim süreçlerinde çok geniş bir yelpazeye yayılmış durumdadır. Bu makineler, özellikle ince sac metalin hassas, derin ve karmaşık şekillere dönüştürülmesi gereken tüm sektörlerde vazgeçilmez bir rol üstlenir. Hidrolik sistemlerin sunduğu yüksek kuvvet kapasitesi, hassas kontrol yeteneği ve esnek çalışma koşulları, onları hem seri üretim hatlarında hem de özel üretim uygulamalarında tercih edilen çözümlerden biri haline getirmiştir.
1. Otomotiv Sanayii
Hidrolik sıvama preslerinin en yaygın kullanıldığı alanların başında otomotiv sektörü gelir. Araç gövdeleri, iç panel bileşenleri, kapı iç sacları, çamurluk içi parçalar, motor kaputları, yakıt deposu parçaları ve yapısal takviyeler gibi birçok komponent, sıvama işlemiyle şekillendirilir. Bu parçalarda hem mekanik dayanım hem de yüzey kalitesi kritik olduğu için sıvama teknolojisi büyük avantaj sağlar. Ayrıca elektrikli araç üretiminde batarya muhafaza kutuları ve termal kontrol kapakları gibi parçalar da hassas sıvama teknikleriyle üretilir.
2. Beyaz Eşya ve Ev Aletleri Sektörü
Çamaşır makineleri, bulaşık makineleri, fırınlar ve buzdolaplarında kullanılan tamburlar, iç kazanlar, arka paneller, kapak iç yüzeyleri ve çeşitli bağlantı gövdeleri sıvama işlemiyle şekillendirilir. Bu parçalarda estetik görünüm, paslanmazlık ve mukavemet gibi unsurlar öne çıkar. Hidrolik sıvama presleri sayesinde hem seri üretime uygunluk sağlanır hem de parça başına düşen üretim maliyeti azaltılır.
3. Mutfak Ekipmanları ve Tencere Üretimi
Paslanmaz çelikten üretilen tencereler, tavalar, çaydanlık gövdeleri, çorba kazanları gibi ürünler, genellikle sıvama yöntemiyle şekillendirilir. Bu sektörde sıvama işleminin en kritik yönü, düzgün yüzey kalitesi ve düzgün et kalınlığı dağılımıdır. Aynı zamanda presleme sırasında çapak, buruşma veya çatlak oluşmaması gerekir. Hidrolik sıvama preslerinin yavaş, kontrollü ve güçlü basma özellikleri, bu ürünlerin üretiminde büyük avantaj sunar.
4. Aydınlatma Sanayii
Endüstriyel ve mimari aydınlatma ürünlerinde kullanılan reflektör kasaları, lamba gövdeleri, dış koruma çerçeveleri gibi birçok metal parça sıvama ile üretilir. Özellikle iç bükey, simetrik ve derin formlar, sıvama için oldukça uygundur. Alüminyum, bakır ve paslanmaz çelik gibi çeşitli metallerin sıvanması sayesinde hem fonksiyonel hem de estetik ürünler elde edilir.
5. Havacılık ve Savunma Sanayi
Havacılık uygulamalarında, özellikle iç gövde parçaları, yakıt tankları, radar muhafazaları, boru bağlantı parçaları gibi yüksek hassasiyet ve dayanıklılık gerektiren bileşenler hidrolik sıvama presleri ile üretilir. Bu alanda sıvama işlemi çoğu zaman ısı ile desteklenerek yapılır, çünkü kullanılan alaşımlar yüksek mukavemetlidir. Aynı durum askeri araç parçaları ve mühimmat muhafazaları gibi savunma sanayi ürünleri için de geçerlidir.
6. Isıtma, Soğutma ve Havalandırma (HVAC) Sistemleri
Klima ve havalandırma sistemlerinde kullanılan fan gövdeleri, motor kapakları, kanal geçiş parçaları gibi öğeler sıvama yöntemiyle şekillendirilir. Genellikle galvanizli çelik, alüminyum ve ince duvarlı saclar kullanılır. Bu parçalar için dairesel simetri ve aerodinamik yapı önemlidir; sıvama yöntemi bu tür geometriler için oldukça uygundur.
7. Elektrik ve Elektronik Sektörü
Bazı elektrik kutuları, priz muhafazaları, hoparlör gövdeleri ve metal dış kaplamalar da sıvama yöntemiyle üretilebilir. Elektronik ürünlerdeki muhafaza parçalarında, ince sacdan yapılmış, hassas toleranslı ve pürüzsüz yüzeye sahip parçalar büyük önem taşır. Bu nedenle sıvama presleri, küçük ve orta ölçekli metal muhafazaların üretiminde kullanılır.
8. Medikal ve Laboratuvar Ürünleri
Steril metal kaplar, analiz cihazı muhafazaları, cerrahi alet gövdeleri gibi medikal alanda kullanılan bazı bileşenler de sıvama ile üretilir. Bu tür ürünlerde pürüzsüzlük, hijyenik tasarım ve paslanmazlık ön plandadır. Sıvama presleri, özellikle paslanmaz çelik gibi zor şekillenen metaller için idealdir.
Sonuç olarak, hidrolik sıvama presleri, sac metalin hassas ve güvenilir biçimde şekillendirilmesi gereken hemen her endüstriyel alanda etkin bir şekilde kullanılmaktadır. Uygulama çeşitliliği sayesinde, hem ağır sanayiden tüketici ürünlerine kadar uzanan geniş bir ürün yelpazesi içinde yer alır hem de üretim süreçlerinde kalite, verimlilik ve maliyet açısından ciddi avantajlar sağlar. Sıvama presleri, yalnızca parça üretiminde değil, aynı zamanda ürün geliştirme ve prototipleme süreçlerinde de kritik rol oynar.
Otomotiv Sanayinde Derin Sıvama
Derin sıvama, otomotiv sanayinde yaygın ve kritik bir metal şekillendirme yöntemidir. Bu yöntem, sac metalin bir zımba yardımıyla kalıp içine çekilerek üç boyutlu, genellikle silindirik veya kutu biçimli parçalar haline getirilmesini sağlar. Derin sıvama, adından da anlaşılacağı üzere, parçanın derinliğinin çapına göre oldukça fazla olduğu durumları ifade eder. Otomotiv sektöründe, özellikle gövde parçaları, iç iskelet panelleri, şasi bileşenleri ve çeşitli muhafazalar gibi dayanıklı ve hassas biçimli parçaların üretiminde bu yöntem sıkça tercih edilir.
Derin Sıvamanın Otomotiv Üretimindeki Rolü
Otomobil üretiminde kullanılan birçok parça, yüksek mukavemet, düşük ağırlık ve mükemmel yüzey kalitesi gibi özelliklere ihtiyaç duyar. Derin sıvama, bu gereksinimlerin çoğuna yanıt verebilen bir teknolojidir. Özellikle ince sac levhaların kullanıldığı bu sektörde, sıvama sayesinde parçalar buruşmadan, çatlamadan ve parça kalınlığını kaybetmeden şekillendirilir.
Örnek parçalar:
- Kapı iç panelleri
- Yakıt tankı gövdeleri
- Motor kaputu iç sacı
- Amortisör muhafazaları
- Tekerlek davlumbazları
- Elektrikli araçlarda batarya kutuları ve modül muhafazaları
Kullanılan Malzemeler
Otomotivde derin sıvama işlemi için genellikle yüksek dayanımlı çelikler (HSLA), galvanizli saclar, alüminyum alaşımları ve bazı özel durumlarda paslanmaz çelikler tercih edilir. Özellikle alüminyum, hafifliği sayesinde araç ağırlığını azaltmak ve yakıt tüketimini düşürmek için yaygınlaşmıştır. Ancak bu malzemelerin sıvama sırasında yırtılmadan veya geri yaylanma (springback) yapmadan şekillenmesi için özel sıvama parametreleri gerekir.
Derin Sıvamada Karşılaşılan Teknik Zorluklar
- Malzeme Yırtılması: Parçanın çekildiği bölgelerde malzeme fazla gerildiğinde yırtılmalar meydana gelebilir. Bu, özellikle keskin köşe ve dar alanlı kalıplarda daha yaygındır.
- Buruşma: Sacın kalıp kenarlarında yeterli tutma kuvveti uygulanmazsa kenar bölgelerde buruşma oluşabilir.
- İncelme: Derin sıvama sırasında sac kalınlığı merkez bölgelerde incelmeye eğilimlidir. Bu da mukavemet kaybına neden olabilir.
- Geri Yaylanma (Springback): Özellikle yüksek dayanımlı çeliklerde form verildikten sonra malzemenin kısmen eski şekline dönmesi olabilir. Bu da şekil doğruluğunu etkiler.
Bu zorlukların üstesinden gelmek için otomotiv sanayisinde gelişmiş hidrolik sıvama presleri, hassas kalıp sistemleri, malzeme yağlama teknikleri ve bilgisayar destekli proses simülasyonları (örneğin AutoForm, DynaForm gibi yazılımlar) kullanılmaktadır.
Hidrolik Preslerin Avantajı
Derin sıvama işlemlerinde, özellikle hassas kontrol gerektiği için hidrolik presler, mekanik preslere kıyasla daha avantajlıdır. Hidrolik sistemler, hareketi daha yavaş ve dengeli iletebildiğinden, sacın gerilmesi daha kontrollü olur. Ayrıca basınç, strok uzunluğu ve yastık kuvveti gibi parametrelerin kolay ayarlanabilir olması, farklı ürün geometrileri için esnek üretim imkânı sağlar.
Seri Üretim ve Otomasyon
Otomotiv sektöründe yüksek adetli üretim yapıldığından, derin sıvama işlemi genellikle robotik besleme sistemleri, otomatik sac yerleştirme aparatları ve parça çıkarıcı robotlar ile birlikte çalışır. Çok istasyonlu sıvama hatlarında parçalar aşama aşama şekillendirilerek daha karmaşık geometrilere ulaşılır. Bu hatlarda üretim çevrim süresi kısa, hata oranı ise minimumdur.
Sonuç
Otomotiv sanayinde derin sıvama, hem yapısal bütünlük hem de üretim maliyeti açısından önemli bir üretim metodudur. Özellikle karmaşık formlu, yüksek dayanımlı ve estetik yüzeyli parçaların seri üretiminde vazgeçilmezdir. Hidrolik pres teknolojisinin sunduğu esneklik ve hassasiyetle birleştiğinde, hem klasik iç-dış gövde parçalarında hem de yeni nesil elektrikli araç bileşenlerinde üstün performans sağlar. Bu yönüyle derin sıvama, otomotiv sektöründe hem bugünün hem de geleceğin temel şekillendirme teknolojilerinden biri olmaya devam edecektir.
Beyaz Eşya ve Ev Aletleri Sektöründe Derin Sıvama
Derin sıvama, beyaz eşya ve ev aletleri sektöründe ince sac metal parçaların yüksek hassasiyetle şekillendirilmesi için yaygın olarak kullanılan kritik bir üretim yöntemidir. Bu sektörün ürünlerinde, dayanıklılık, estetik görünüm ve işlevsellik ön planda olduğundan, derin sıvama teknolojisi ürün kalitesini artırırken üretim verimliliğini de önemli ölçüde iyileştirir.
Derin Sıvamanın Beyaz Eşya Üretimindeki Önemi
Beyaz eşya ürünleri—çamaşır makineleri, bulaşık makineleri, buzdolapları, fırınlar gibi—çoğunlukla geniş yüzeyli, derin ve karmaşık şekilli metal parçalardan oluşur. Bu parçaların üretiminde derin sıvama, sac metalin kalıp içine kontrollü ve eşit şekilde çekilmesini sağlayarak buruşma, çatlama veya kalınlıkta istenmeyen değişiklikler olmadan ürünün istenilen formda üretilmesini mümkün kılar.
Üretimde Derin Sıvama Kullanılan Parçalar
- Çamaşır makinesi tamburları ve iç kazanları: Bu parçalar, yüksek dayanıklılık ve mükemmel yüzey kalitesi gerektirir. Derin sıvama sayesinde sağlam ve düzgün yüzeyli tamburlar elde edilir.
- Buzdolabı iç ve dış panelleri: Hem estetik hem dayanıklı olmaları gerekir; derin sıvama, bu parçaların hacimli ve düzgün şekillerde üretilmesini sağlar.
- Fırın ve ocak kapakları: Isıya dayanıklı, düzgün yüzeyli ve dayanıklı kapaklar için derin sıvama ideal bir yöntemdir.
- Bulaşık makinesi kazanları ve dış gövdeleri: Sıvama ile elde edilen düzgün ve paslanmaya dayanıklı parçalar, ürün ömrünü uzatır.
Kullanılan Malzemeler
Beyaz eşya sektöründe genellikle galvanizli çelik, paslanmaz çelik ve alüminyum alaşımları kullanılır. Bu malzemeler hem dayanıklılık hem de korozyon direnci sağlar. Derin sıvama işlemi sırasında bu malzemelerin mekanik özelliklerine uygun basınç, hız ve yastık kuvveti ayarlamaları yapılır.
Teknik Zorluklar ve Çözümler
Derin sıvama işleminde karşılaşılan başlıca zorluklar arasında malzemenin yırtılması, buruşması ve parçanın şekil tutmaması yer alır. Beyaz eşya sektöründe bu sorunların önüne geçmek için:
- Kalıp tasarımı optimize edilir, kenar radyüsleri ve sac tutma kuvvetleri detaylı hesaplanır.
- Malzemenin yüzeyi uygun şekilde yağlanarak sürtünme azaltılır.
- Presin basınç ve hız parametreleri hassas biçimde ayarlanır.
- Çok aşamalı sıvama prosesleri kullanılarak daha karmaşık geometriler elde edilir.
Hidrolik Preslerin Sektöre Katkısı
Hidrolik sıvama presleri, beyaz eşya parçalarının üretiminde mekanik preslere göre daha kontrollü ve yumuşak bir güç uygulaması sağlar. Bu da sacın eşit biçimde akmasını kolaylaştırır ve ürün kalitesini artırır. Ayrıca, preslerin ayarlanabilir basınç ve strok uzunlukları sayesinde farklı parça tipleri aynı makinada üretilebilir, bu da esnekliği artırır.
Seri Üretim ve Otomasyon
Beyaz eşya üretimi genellikle yüksek adetli olduğundan, pres hatları robotik besleme, parça çıkarma ve kalite kontrol sistemleri ile entegre edilmiştir. Bu sayede işçilik maliyetleri azalır, üretim hızı artar ve insan kaynaklı hata riski minimize edilir.
Sonuç
Beyaz eşya ve ev aletleri sektöründe derin sıvama, ürünlerin dayanıklılığını, estetiğini ve fonksiyonelliğini sağlamak için vazgeçilmez bir yöntemdir. Hidrolik sıvama preslerinin hassasiyet ve esnekliği, bu sektörde kaliteli ve ekonomik üretim yapılmasını mümkün kılar. Böylece, modern beyaz eşya ürünleri hem teknik gereksinimleri karşılar hem de tüketici beklentilerini en üst seviyede tutar.
Mutfak Ekipmanları ve Tencere Üretiminde Derin Sıvama
Mutfak ekipmanları ve özellikle tencere, tava gibi pişirme kaplarının üretiminde derin sıvama, en yaygın ve etkili metal şekillendirme yöntemlerinden biridir. Bu alanda kullanılan ürünler hem dayanıklı, hem estetik olarak çekici hem de kullanıcı sağlığına uygun olmalıdır. Derin sıvama, ince sac metalin kalıp içine kontrollü şekilde çekilerek, genellikle silindirik veya hafif konik formda, derin ve pürüzsüz yüzeyli mutfak ürünleri üretilmesini sağlar.
Derin Sıvamanın Mutfak Ekipmanlarındaki Rolü
Tencereler, tavalar, çaydanlıklar, kazanlar ve benzeri mutfak ürünleri, genellikle paslanmaz çelik, alüminyum veya bakır gibi malzemelerden yapılır. Derin sıvama sayesinde bu metaller, yüksek mukavemetlerini ve ısı iletkenlik özelliklerini koruyarak, istenilen şekle kolayca getirilir. Özellikle tencere ve tava gibi ürünlerde, düzgün yüzey kalitesi ve eşit duvar kalınlığı, kullanım ömrü ve ısı dağılımı açısından kritik öneme sahiptir.
Üretimde Kullanılan Malzemeler
- Paslanmaz çelik: Korozyona dayanıklılığı ve estetik parlaklığı nedeniyle tercih edilir.
- Alüminyum: Hafifliği ve yüksek ısı iletkenliği ile bilinir; genellikle iç yüzeyi kaplanarak kullanılır.
- Bakır: Isı iletkenliği en yüksek olan malzeme olup, çoğunlukla dış katmanlarda kullanılır.
Her malzeme türü, sıvama sırasında farklı davranışlar sergiler; bu nedenle pres parametreleri (basınç, hız, yastık kuvveti) malzemenin özelliklerine göre optimize edilir.
Teknik Özellikler ve Zorluklar
Derin sıvama sırasında, ürünün kenarlarında ve taban kısmında meydana gelen kalınlık incelmeleri ve buruşmalar en büyük üretim zorluklarıdır. Özellikle ince saclarda, bu problemler kaliteyi ve ürün dayanıklılığını olumsuz etkileyebilir. Bu nedenle:
- Kalıp tasarımı hassas şekilde yapılmalı, özellikle kenar yarıçapları dikkatle seçilmelidir.
- Sac üzerine uygulanan yastık kuvveti, malzemenin kontrollü akışını sağlamak için özenle ayarlanmalıdır.
- Yüzey yağlama ve uygun sürtünme koşulları sağlanmalıdır.
- Hidrolik presin basınç ve hareket hızları, malzeme tipine göre hassas biçimde kontrol edilmelidir.
Hidrolik Sıvama Preslerinin Avantajları
Mutfak ekipmanları üretiminde hidrolik sıvama presleri, güçlü fakat kontrollü kuvvet uygulaması yaparak sacın kalıp içine yumuşak ve buruşmasız akmasını sağlar. Bu, özellikle karmaşık ve derin formlu tencereler için son derece önemlidir. Ayrıca, presin ayarlanabilir hareket özellikleri sayesinde farklı ürün geometrilerine kolayca geçiş yapılabilir; böylece üretim esnekliği artar.
Seri Üretim ve Otomasyon
Tencere ve tava üretiminde yüksek adetli üretim gerekliliği, hidrolik sıvama preslerinin robotik besleme sistemleri, otomatik parça çıkarma ve kalite kontrol birimleri ile birlikte kullanılmasını gerektirir. Bu entegrasyon sayesinde üretim hızı artırılırken insan kaynaklı hata ve işçilik maliyetleri azaltılır.
Sonuç
Derin sıvama, mutfak ekipmanları ve tencere üretiminde hem ürün kalitesini hem de üretim verimliliğini artıran temel bir teknolojidir. Hidrolik sıvama presleri, bu süreçte sacın hassas biçimde şekillendirilmesini sağlayarak, uzun ömürlü, estetik ve fonksiyonel mutfak ürünlerinin ortaya çıkmasına olanak tanır. Günümüzde modern üretim tesislerinde, derin sıvama teknolojisi ile üretilen tencereler ve benzeri ekipmanlar, kullanıcı beklentilerini ve kalite standartlarını karşılamada önemli bir yere sahiptir.
Aydınlatma Sanayinde Derin Sıvama
Aydınlatma sektöründe, özellikle endüstriyel, mimari ve dekoratif aydınlatma ürünlerinin üretiminde derin sıvama teknolojisi önemli bir yer tutar. Metal malzemelerin hassas ve estetik biçimde şekillendirilmesini sağlayan derin sıvama, reflektörler, lamba gövdeleri, abajur çerçeveleri gibi birçok parçanın üretiminde tercih edilir. Bu yöntem sayesinde hafif, dayanıklı ve yüzey kalitesi yüksek ürünler elde edilir.
Derin Sıvamanın Aydınlatma Ürünlerindeki Rolü
Aydınlatma ekipmanlarının temel bileşenlerinden biri olan reflektör ve gövde parçaları, genellikle simetrik, silindirik veya kompleks eğrilere sahip yapılardır. Derin sıvama, ince sac metalin bu karmaşık üç boyutlu formlara dönüştürülmesini sağlar. Ürünlerin yüzeylerinin düzgün ve pürüzsüz olması, ışığın doğru şekilde yansıtılması için kritik önem taşır. Ayrıca derin sıvama, malzemenin kalınlık dağılımını dengeler ve böylece hem estetik hem de fonksiyonel kaliteyi artırır.
Kullanılan Malzemeler
Aydınlatma sanayinde genellikle alüminyum alaşımları, paslanmaz çelik ve galvanizli çelik saclar kullanılır.
- Alüminyum: Hafifliği ve iyi yansıtıcı özellikleri nedeniyle tercih edilir.
- Paslanmaz çelik: Dayanıklılığı ve korozyona karşı direnciyle öne çıkar.
- Galvanizli çelik: Ekonomik çözümler için yaygın kullanılır.
Malzeme seçimi, ürünün kullanım alanına, estetik beklentilere ve dayanıklılık gereksinimlerine göre yapılır.
Teknik Zorluklar
Derin sıvama işlemi sırasında, özellikle ince saclarda:
- Malzeme yırtılması,
- Buruşma,
- Kalınlık incelmesi,
- Yüzeyde çizik veya deformasyon oluşması gibi problemler yaşanabilir.
Bu zorluklar, kalıp tasarımı ve pres ayarlarının dikkatli optimize edilmesiyle minimize edilir. Kalıp köşe yarıçapları, sac tutma kuvveti ve yağlama sistemleri bu süreçte kritik rol oynar.
Hidrolik Sıvama Preslerinin Önemi
Hidrolik sıvama presleri, aydınlatma sektöründe kullanılan parçaların üretiminde yumuşak, kontrollü ve güçlü basınç uygulayarak sacın kalıp içinde eşit şekilde akmasını sağlar. Bu özellik, hassas geometrilere sahip reflektör ve gövde parçalarında yüksek kalite standardı yakalamayı mümkün kılar. Ayrıca basınç ve strok ayarlarının kolayca değiştirilebilmesi, farklı ürün tasarımlarına hızlı adaptasyon imkanı sunar.
Seri Üretim ve Otomasyon
Aydınlatma ürünleri genellikle orta ve yüksek adetlerde üretilir. Bu nedenle pres hatları, otomatik sac besleme, parça çıkarma ve kalite kontrol sistemleri ile entegre edilir. Robotik otomasyon, üretim hızını artırırken işçilik maliyetlerini ve hata oranlarını düşürür.
Sonuç
Derin sıvama teknolojisi, aydınlatma sanayinde estetik, fonksiyonel ve dayanıklı ürünlerin üretiminde kritik bir rol oynar. Hidrolik sıvama presleri ile yapılan hassas ve kontrollü şekillendirme, ışığın istenilen şekilde yansıtılması ve ürünlerin uzun ömürlü olması için gereklidir. Bu sayede aydınlatma sektöründe kalite ve verimlilik standartları yükselirken, üretim süreçleri daha esnek ve ekonomik hale gelir.
Havacılık ve Savunma Sanayinde Derin Sıvama
Havacılık ve savunma sanayileri, yüksek hassasiyet, dayanıklılık ve güvenlik standartlarının zorunlu olduğu sektörlerdir. Bu alanlarda kullanılan metal parçalar, çoğunlukla hafif, yüksek mukavemetli ve karmaşık geometrilere sahip olmak zorundadır. Derin sıvama, bu talepleri karşılamak için ideal bir metal şekillendirme yöntemi olarak öne çıkar. İnce sac metalin kontrollü biçimde kalıp içine çekilerek karmaşık, derin ve yüksek kaliteli parçalar oluşturulmasını sağlar.
Havacılık Sektöründe Derin Sıvama
Havacılık uygulamalarında, uçak gövde panelleri, yakıt tankları, iç yapısal elemanlar, kabin parçaları, motor muhafazaları ve çeşitli bağlantı parçaları derin sıvama ile üretilir. Bu parçalar yüksek mukavemet ve düşük ağırlık kombinasyonunu sağlamak amacıyla genellikle titanyum, alüminyum alaşımları, yüksek dayanımlı çelikler ve bazen kompozit malzeme destekli metallerden yapılır. Derin sıvama, bu malzemelerin mekanik özelliklerini koruyarak hassas ve dayanıklı formlar elde edilmesini mümkün kılar.
Savunma Sanayinde Derin Sıvama
Savunma uygulamalarında ise zırh panelleri, mühimmat muhafazaları, araç gövde parçaları, radar ve elektronik muhafazalar gibi kritik bileşenler sıvama yoluyla şekillendirilir. Bu parçalar, yüksek dayanıklılık, darbe direnci ve koruma işlevleri nedeniyle özellikle kalın ve sert metallerden üretilir. Derin sıvama işlemi burada genellikle yüksek basınç ve özel kalıp tasarımları gerektirir.
Kullanılan Malzemeler
- Titanyum ve Alaşımları: Yüksek mukavemet/ağırlık oranı nedeniyle özellikle havacılıkta tercih edilir.
- Alüminyum Alaşımları: Hafiflik ve işlenebilirlik avantajıyla yaygın kullanılır.
- Yüksek Mukavemetli Çelikler: Savunma sanayinde zırh ve dayanıklı parçalar için kullanılır.
- Paslanmaz Çelik ve Özel Alaşımlar: Korozyon direnci ve mekanik dayanım gereken alanlarda tercih edilir.
Teknik Zorluklar ve Çözümler
Havacılık ve savunma sanayinde kullanılan malzemeler genellikle zor şekillenen ve yüksek performans gerektiren türdendir. Derin sıvama işlemi sırasında:
- Malzemenin yırtılması ve çatlaması riski yüksektir.
- Malzeme kalınlığında kontrol zorunludur; incelme ve deformasyon önlenmelidir.
- Parçaların boyutsal toleransları çok sıkıdır.
- Yüzey kalitesi kritik olup, çizik ve buruşmalar kabul edilemez.
Bu zorlukları aşmak için gelişmiş kalıp tasarımları, yüksek hassasiyetli hidrolik sıvama presleri ve sıcak sıvama teknikleri kullanılır. Sıcak sıvama, özellikle titanyum ve bazı yüksek mukavemetli alaşımlarda, malzemenin şekillendirilebilirliğini artırmak için tercih edilir.
Hidrolik Sıvama Preslerinin Önemi
Hidrolik presler, yüksek basınç uygulama yetenekleri, yumuşak hareketleri ve parametrelerin hassas ayarlanabilmesi sayesinde havacılık ve savunma parçalarının üretiminde vazgeçilmezdir. Çok istasyonlu sıvama hatları, karmaşık geometrilerin aşamalı olarak oluşturulmasını sağlar. Ayrıca preslerin gelişmiş kontrol sistemleri, üretim sürecinde kaliteyi garanti eder.
Sonuç
Havacılık ve savunma sanayinde derin sıvama, yüksek teknoloji gerektiren ve zorlayıcı üretim koşullarına uyum sağlayan kritik bir üretim metodudur. Hidrolik sıvama presleri, yüksek mukavemetli ve karmaşık parçaların hassasiyetle üretilmesini mümkün kılarak, sektörlerin güvenlik ve performans standartlarını karşılamasında kilit rol oynar. Bu teknolojinin gelişimi, havacılık ve savunma ürünlerinde kalite ve dayanıklılığın artırılmasına doğrudan katkı sağlamaktadır.
Isıtma, Soğutma ve Havalandırma (HVAC) Sistemlerinde Derin Sıvama
Isıtma, soğutma ve havalandırma (HVAC) sistemleri, konforlu yaşam ve çalışma alanları yaratmak için kritik öneme sahip endüstriyel sistemlerdir. Bu sistemlerde kullanılan birçok metal parça, özellikle kanallar, fan gövdeleri, motor muhafazaları, difüzörler ve ısı değiştirici elemanlar, dayanıklı ve doğru şekilli olmaları için derin sıvama yöntemiyle üretilir. Derin sıvama, HVAC bileşenlerinin hem performansını hem de üretim verimliliğini artıran temel teknolojilerden biridir.
Derin Sıvamanın HVAC Sistemlerindeki Önemi
HVAC sistemlerinde kullanılan metal parçalar genellikle geniş yüzeyli, hacimli ve karmaşık geometrilere sahiptir. Bu parçaların düzgün ve pürüzsüz yüzeylere sahip olması, hava akışının optimize edilmesi ve sistem verimliliğinin artırılması açısından kritik önem taşır. Derin sıvama, ince sac metalin kalıp içine kontrollü şekilde çekilmesini sağlayarak bu özellikleri elde etmeyi mümkün kılar.
Örnek parçalar:
- Hava kanalları ve bağlantı elemanları
- Fan ve vantilatör gövdeleri
- Motor muhafazaları
- Difüzör ve menfez parçaları
- Isı değiştirici plakaları ve muhafazaları
Kullanılan Malzemeler
HVAC bileşenlerinde genellikle galvanizli çelik, alüminyum ve paslanmaz çelik saclar tercih edilir.
- Galvanizli çelik: Korozyona karşı dayanıklılığı nedeniyle yaygın kullanılır.
- Alüminyum: Hafifliği ve iyi korozyon direnci ile öne çıkar.
- Paslanmaz çelik: Özellikle nemli veya kimyasal etkilerin olduğu ortamlarda tercih edilir.
Teknik Zorluklar
Derin sıvama işlemi sırasında HVAC parçalarında karşılaşılan bazı zorluklar şunlardır:
- Malzemenin buruşması veya yırtılması riski, özellikle ince saclarda artar.
- Parçaların boyutsal hassasiyeti ve yüzey kalitesi üretim kalitesini doğrudan etkiler.
- Kanallar ve difüzörlerde hava akışını olumsuz etkileyebilecek deformasyonların önlenmesi gerekir.
Bu sorunlar, kalıp tasarımının optimize edilmesi, uygun sac kalınlığı ve malzeme seçimi ile pres parametrelerinin hassas ayarlanması yoluyla aşılır.
Hidrolik Sıvama Preslerinin Avantajları
Hidrolik sıvama presleri, HVAC bileşenlerinin üretiminde yüksek basınç uygulama, hareket kontrolü ve yastık kuvveti ayarı sayesinde sacın kontrollü akışını sağlar. Bu da ürünlerde buruşma ve çatlamayı önlerken, yüksek kaliteli ve dayanıklı parçaların üretilmesine olanak tanır. Ayrıca hidrolik preslerin esnekliği sayesinde farklı ürün geometrilerine hızlı geçiş yapılabilir.
Seri Üretim ve Otomasyon
HVAC bileşenleri genellikle yüksek adetlerde üretilir. Bu nedenle pres hatları, robotik besleme sistemleri, otomatik parça çıkarma ve kalite kontrol sistemleri ile entegre edilerek üretim verimliliği artırılır. Otomasyon, işçilik maliyetlerini azaltırken, üretim kalitesini ve tutarlılığını yükseltir.
Sonuç
Isıtma, soğutma ve havalandırma sistemlerinde derin sıvama, dayanıklı, yüksek performanslı ve estetik bileşenlerin üretiminde kritik rol oynar. Hidrolik sıvama presleri sayesinde bu sektörün gereksinimleri karşılanırken, üretim süreçleri esnek, ekonomik ve yüksek kaliteli hale gelir. Böylece HVAC sistemleri hem teknik hem de estetik açıdan üstün standartlara ulaşır.
Elektrik ve Elektronik Sektöründe Derin Sıvama
Elektrik ve elektronik sektöründe kullanılan birçok metal parça, cihazların işlevselliği, dayanıklılığı ve estetiği açısından kritik öneme sahiptir. Bu parçaların üretiminde derin sıvama teknolojisi, ince sac metalin hassas ve karmaşık şekillerde işlenmesini mümkün kılar. Özellikle muhafaza kasaları, bağlantı elemanları ve küçük elektronik bileşenlerin üretiminde derin sıvama, yüksek kalite ve düşük maliyet avantajları sağlar.
Derin Sıvamanın Elektrik ve Elektronik Ürünlerindeki Rolü
Elektrik ve elektronik cihazlarda kullanılan metal muhafazalar, devre kartı koruyucuları, priz ve anahtar gövdeleri, konektör kapakları gibi parçalar genellikle ince sacdan yapılır. Derin sıvama sayesinde bu parçalar, hem sağlamlık hem de hassas boyutsal toleranslarla üretilir. Ayrıca ürünlerin elektromanyetik girişimden (EMI) korunması için metal muhafazaların tam kapama sağlaması gerekir; bu da derin sıvama ile şekillendirilen parçaların kalitesine bağlıdır.
Kullanılan Malzemeler
Elektrik ve elektronik sektöründe çoğunlukla galvanizli çelik, alüminyum ve paslanmaz çelik kullanılır.
- Galvanizli çelik: Korozyona karşı dayanıklılığı ile tercih edilir.
- Alüminyum: Hafifliği ve iyi elektriksel iletkenliği sebebiyle yaygındır.
- Paslanmaz çelik: Mekanik dayanıklılık ve estetik için kullanılır.
Teknik Zorluklar
Bu sektörde derin sıvama sırasında karşılaşılan zorluklar şunlardır:
- İnce saclarda malzeme yırtılması ve buruşma riski.
- Parçaların hassas boyutlarda olması gerektiği için kalıp toleranslarının sıkı tutulması.
- Yüzey kalitesinin yüksek olması, çizik ve deformasyonların minimumda tutulması.
- Seri üretimde tutarlılığın sağlanması.
Bu zorluklar, modern kalıp tasarımları, ileri pres kontrol sistemleri ve uygun malzeme seçimi ile aşılır.
Hidrolik Sıvama Preslerinin Avantajları
Hidrolik sıvama presleri, elektrik ve elektronik sektöründe özellikle ince sacların hassas şekillendirilmesinde üstünlük sağlar. Basınç ve hareket kontrolü sayesinde malzemenin kalıp içinde düzgün akışı sağlanır, yırtılma ve buruşma riski minimize edilir. Ayrıca hızlı parametre ayarlamaları, farklı ürün tiplerine kolayca adapte olunmasını mümkün kılar.
Seri Üretim ve Otomasyon
Elektrik ve elektronik sektöründe yüksek adetli üretim yapıldığından, pres hatları genellikle robotik besleme, otomatik parça çıkarma ve kalite kontrol sistemleri ile donatılır. Bu sayede üretim hızı artar, hata oranı azalır ve maliyetler düşer.
Sonuç
Elektrik ve elektronik sektöründe derin sıvama, hem ürün kalitesi hem de üretim verimliliği açısından kritik bir rol oynar. Hidrolik sıvama presleri, bu sektördeki ince ve hassas metal parçaların yüksek hassasiyetle ve ekonomik olarak üretilmesini sağlar. Böylece ürünler hem fonksiyonel hem de estetik açıdan yüksek standartları karşılar.
Medikal ve Laboratuvar Ürünlerinde Derin Sıvama
Medikal ve laboratuvar ekipmanlarının üretiminde, yüksek hijyen standartları, dayanıklılık, hassas boyutlar ve estetik görünüm ön plandadır. Bu sektörlerde kullanılan birçok metal parça, ince sac metalin derin sıvama yöntemiyle şekillendirilmesiyle elde edilir. Derin sıvama, paslanmaz çelik gibi zor şekillenen malzemelerin bile hassas ve kaliteli biçimde işlenmesini mümkün kılarak, medikal ve laboratuvar cihazlarının güvenilirliğini artırır.
Derin Sıvamanın Medikal ve Laboratuvar Ürünlerindeki Önemi
Cerrahi alet gövdeleri, steril kaplar, implant muhafazaları, analiz cihazlarının metal kasaları ve çeşitli laboratuvar aparatları, genellikle yüksek kaliteli paslanmaz çelik veya alüminyum alaşımlarından yapılır. Derin sıvama yöntemi, bu parçaların pürüzsüz yüzeylere, kesin boyutlara ve sterilize edilebilir yapılarına sahip olmasını sağlar. Ayrıca ürünlerin kimyasal ve ısı dayanımları da sıvama işleminde kullanılan malzemenin özelliklerine bağlı olarak optimize edilir.
Kullanılan Malzemeler
- Paslanmaz çelik (özellikle 316L ve 304 kaliteleri): Korozyona karşı üstün direnç ve sterilizasyon dayanımı sağlar.
- Alüminyum alaşımları: Hafif ve biyouyumlu seçenekler için tercih edilir.
- Titanyum ve özel alaşımlar: Özellikle implant ve ileri medikal uygulamalarda kullanılır.
Teknik Zorluklar
Medikal ve laboratuvar ürünlerinde derin sıvama sırasında:
- Malzemenin yırtılması ve buruşması olmamalı, yüksek yüzey kalitesi korunmalıdır.
- Parça toleransları çok sıkı olduğundan, kalıp ve proses kontrolü titizlikle yapılmalıdır.
- Yüzeyde çizik, çatlak veya deformasyon kesinlikle kabul edilemez.
- İşlem sırasında kullanılan yağlayıcıların medikal standartlara uygun olması gerekir.
Bu zorlukları aşmak için ileri kalıp teknolojileri, hassas hidrolik sıvama presleri ve yüksek kaliteli malzeme kullanımı şarttır.
Hidrolik Sıvama Preslerinin Rolü
Hidrolik sıvama presleri, malzemenin yumuşak ve kontrollü şekilde şekillendirilmesini sağlayarak medikal ürünlerde yüksek kalite ve tutarlılık sağlar. Basınç ve hareketin hassas kontrolü, malzemenin kalıp içinde düzgün akmasına, dolayısıyla homojen kalınlık ve kusursuz yüzey elde edilmesine yardımcı olur.
Seri Üretim ve Kalite Kontrol
Medikal sektöründe seri üretim çoğu zaman yüksek standartlarda kalite kontrol sistemleri ile desteklenir. Robotik besleme, otomatik parça çıkarma ve sonrasında detaylı yüzey ve boyut kontrolleri, hatalı ürünlerin ayıklanmasını sağlar.
Sonuç
Derin sıvama teknolojisi, medikal ve laboratuvar ekipmanlarının üretiminde hassasiyet, dayanıklılık ve sterilizasyon gereksinimlerini karşılamak için vazgeçilmezdir. Hidrolik sıvama presleri ile gerçekleştirilen bu işlem, sektörde güvenilir, kaliteli ve uzun ömürlü ürünlerin ortaya çıkmasını mümkün kılarak sağlık alanında kritik bir rol oynar.
Derin Sıvama Preslerinde Modern Teknolojik Özellikler ve Otomasyon
Günümüzde derin sıvama presleri, sadece güçlü mekanik kuvvet uygulayan makineler olmanın ötesine geçmiş; gelişmiş teknoloji ve otomasyon sistemleriyle donatılarak üretim verimliliğini, kaliteyi ve esnekliği üst seviyelere taşımaktadır. Modern derin sıvama presleri, karmaşık parçaların hassas, hızlı ve tekrarlanabilir şekilde üretilmesini mümkün kılan pek çok yenilikçi özellikle donatılmıştır.
1. Bilgisayar Kontrollü (CNC) Pres Sistemleri
Modern sıvama presleri, bilgisayar destekli kontrol üniteleriyle donatılmıştır. Bu sayede:
- Basınç, hız, strok uzunluğu ve yastık kuvveti gibi parametreler hassas şekilde programlanabilir.
- Proses parametreleri gerçek zamanlı olarak izlenip otomatik olarak ayarlanabilir.
- Farklı ürünlere hızlı geçiş için parametre setleri saklanabilir ve çağrılabilir.
Bu özellikler üretim esnekliğini artırırken, parça kalitesinin tutarlı olmasını sağlar.
2. Sensör ve İzleme Sistemleri
Derin sıvama preslerinde; basınç sensörleri, hareket algılayıcılar, sıcaklık ve vibrasyon sensörleri gibi ileri seviye sensörler kullanılır. Bu sayede:
- Üretim sırasında olası sorunlar anlık olarak tespit edilir.
- Malzeme davranışları ve pres performansı detaylı analiz edilir.
- Bakım ihtiyaçları önceden belirlenerek planlanabilir (önleyici bakım).
Bu sistemler arıza sürelerini azaltır ve üretim kalitesini yükseltir.
3. Hidrolik ve Elektronik Entegrasyon
Modern derin sıvama preslerinde hidrolik sistemler elektronik kontrol üniteleriyle entegre edilmiştir. Bu sayede:
- Kuvvet ve hız kontrolü çok daha hassas yapılabilir.
- Pres hareketleri yumuşak ve optimize edilmiş olur, malzemenin kalıp içinde daha düzgün akışı sağlanır.
- Enerji verimliliği artırılır.
4. Otomatik Besleme ve Parça Çıkarma Sistemleri
Derin sıvama proseslerinin otomasyonu; robotik kol, konveyör sistemleri ve özel aparatlarla desteklenir.
- Sac malzeme otomatik olarak pres içine beslenir.
- Sıvama işlemi tamamlanan parçalar robotlar tarafından alınarak sonraki işleme veya paketlemeye yönlendirilir.
- Bu sistemler insan müdahalesini azaltır, üretim hızını artırır ve iş güvenliğini iyileştirir.
5. Proses Simülasyonu ve Dijital İkiz Teknolojisi
Günümüzde üretim öncesinde proses simülasyonu yazılımları (AutoForm, DynaForm vb.) kullanılarak:
- Malzemenin kalıp içindeki davranışı önceden analiz edilir.
- Olası sorunlar (çatlama, buruşma, kalınlık incelmesi) önceden tespit edilip tasarım optimize edilir.
- Dijital ikiz teknolojisi ile gerçek presin sanal bir modeli oluşturulur; bu model üzerinden proses optimizasyonu ve uzaktan kontrol yapılabilir.
6. Enerji Verimliliği ve Çevre Dostu Tasarımlar
Modern derin sıvama preslerinde enerji tasarrufunu artırmak amacıyla servo-hidrolik sistemler, değişken hız kontrollü pompalar ve akıllı enerji yönetim sistemleri kullanılır. Bu sayede:
- Enerji tüketimi önemli ölçüde azalır.
- Daha çevreci ve sürdürülebilir üretim mümkün olur.
7. Yüksek Hız ve Döngü Süresi Optimizasyonu
Otomasyon ve gelişmiş kontrol sistemleri sayesinde preslerin döngü süreleri optimize edilir, bu da daha yüksek üretim kapasiteleri anlamına gelir. Aynı zamanda, hassas kontrollü yumuşak hareketler, malzeme üzerindeki stresleri azaltarak ürün kalitesini artırır.
Sonuç olarak, derin sıvama preslerinde modern teknolojik özellikler ve otomasyon sistemleri, üretim süreçlerini daha esnek, verimli ve kaliteli hale getirmektedir. Bu gelişmeler sayesinde, karmaşık geometrilere sahip parçalar hızlı, hatasız ve ekonomik şekilde üretilebilmekte, aynı zamanda iş güvenliği ve enerji verimliliği standartları da yükselmektedir. Gelecekte de dijitalleşme ve yapay zeka entegrasyonlarıyla derin sıvama presleri daha akıllı ve otonom sistemlere dönüşmeye devam edecektir.
Malzeme Uyumluğu ve Kalıp Sistemleri
Derin sıvama işleminin başarısı, büyük ölçüde kullanılan malzemenin özellikleri ile kalıp sistemlerinin uyumuna bağlıdır. Malzeme ve kalıp arasındaki doğru etkileşim, kaliteli, dayanıklı ve ölçüsel olarak hassas parçalar üretilmesini sağlar. Bu nedenle malzeme seçimi ve kalıp tasarımı süreçleri birbiriyle entegre şekilde planlanmalıdır.
1. Malzeme Uyumluğu
Derin sıvama işleminde kullanılan malzemeler genellikle ince sac formundadır ve çeşitli mekanik ve kimyasal özelliklere sahiptir. Malzeme uyumluluğu, işlemin sorunsuz ve verimli gerçekleşmesi için kritik öneme sahiptir.
- Malzeme Türü: Çelik (galvanizli, paslanmaz), alüminyum, bakır, titanyum gibi malzemeler farklı şekillendirme davranışları gösterir.
- Akma Mukavemeti ve Sertlik: Yüksek akma mukavemetine sahip malzemeler daha yüksek basınç ve kontrollü proses gerektirir.
- Plastik Akma Kabiliyeti: Malzemenin kalıp içinde kolayca akması, yırtılma ve buruşma riskini azaltır.
- Kalınlık ve Homojenlik: Sac kalınlığı ve yüzey düzgünlüğü, form verme kalitesini etkiler. İnce ve homojen malzemeler daha başarılı sonuç verir.
- Yüzey Özellikleri: Yağlama, korozyon dayanımı ve yüzey pürüzlülüğü gibi faktörler malzeme-kalıp sürtünmesini etkiler.
Malzeme ve kalıp uyumu sağlanmazsa, çatlama, buruşma, yüzey kusurları ve ölçü hataları meydana gelir.
2. Kalıp Sistemleri
Derin sıvama kalıpları, malzemenin şekillendiği, yüksek mukavemetli ve hassas tasarlanmış araçlardır. Kalıp sistemlerinin yapısı ve özellikleri, sıvama işleminin kalitesini doğrudan belirler.
- Kalıp Tasarımı: Parçanın geometrisi, malzeme özellikleri ve üretim hacmi dikkate alınarak optimize edilir. Köşe yarıçapları, kalıp derinliği, kenar tutma bölgeleri dikkatle seçilir.
- Kalip Malzemesi: Genellikle yüksek sertlikte çelik alaşımları (örneğin P20, H13) tercih edilir; aşınmaya ve darbelere dayanıklı olmalıdır.
- Kalıp Yastığı (Blank Holder): Sac kenarlarını sabitleyerek buruşmayı önler ve malzemenin kontrollü akışını sağlar. Yastığın kuvveti ayarlanabilir olmalıdır.
- Yağlama Sistemleri: Kalıp ve malzeme arasındaki sürtünmeyi azaltmak için uygun yağlama uygulanır; bu hem malzeme ömrünü hem de kalıp dayanıklılığını artırır.
- Soğutma ve Isıtma Kanalları: Kalıplarda ısının dengeli dağılması için tasarlanmış kanallar, işlem kalitesini yükseltir ve proses süresini kısaltır.
- Modüler ve Çok Aşamalı Kalıplar: Karmaşık parçalar için modüler kalıp sistemleri ve çok aşamalı sıvama kalıpları kullanılır. Böylece farklı işlemler art arda aynı pres hattında yapılabilir.
3. Malzeme-Kalıp Etkileşimi ve Optimizasyon
Malzeme ile kalıp arasındaki sürtünme, basınç ve hareket optimizasyonu, başarılı bir derin sıvama için gereklidir. Bu uyum:
- Malzemenin kalıp içinde buruşmadan, yırtılmadan şekillenmesini sağlar.
- Üretim hızını artırır ve hatalı ürün oranını düşürür.
- Kalıp ve malzeme ömrünü uzatır.
Bu nedenle, malzeme özellikleri üretim öncesinde analiz edilerek kalıp tasarımına yansıtılır; bilgisayar destekli simülasyonlarla ideal parametreler belirlenir.
Sonuç olarak, derin sıvama işlemlerinde malzeme uyumluluğu ve kalıp sistemleri birbirini tamamlayan iki temel unsurdur. Doğru malzeme seçimi ile optimize edilmiş kalıp tasarımı, yüksek kaliteli, dayanıklı ve ölçüsel hassasiyette ürünler elde edilmesini sağlar. Modern üretim tesislerinde, bu uyumu sağlamak için gelişmiş malzeme testleri, simülasyonlar ve hassas kalıp mühendisliği uygulanmaktadır.
Derin Sıvama Kalıpları
Derin sıvama kalıpları, ince sac metalin istenilen üç boyutlu şekle dönüştürülmesi sırasında malzemenin şekillendiği ve yönlendirildiği kritik araçlardır. Kalıp tasarımı ve yapısı, derin sıvama işleminin başarısını doğrudan etkiler. Kalıplar, sacın kontrollü akışını sağlarken malzemenin buruşmasını, yırtılmasını ve diğer deformasyonları önlemeye yardımcı olur.
Derin Sıvama Kalıplarının Temel Bileşenleri
- Ana Kalıp (Punch / Piston):
Sacı kalıp içine iten veya çeken parça. Genellikle sacın nihai formunu alan şekle sahiptir. Bu parça, sacın istenilen geometrisini oluşturmak için malzemeye kuvvet uygular. - Kalıp Gövdesi (Die):
Punch ile birlikte çalışan kalıp boşluğu ve destek elemanlarından oluşur. Sacın punch tarafından şekillendirilirken doğru yönlendirilmesini ve desteklenmesini sağlar. - Yastık (Blank Holder / Pressure Pad):
Sacın kenarlarını sıkıca tutarak malzemenin kalıp boşluğu içinde buruşmasını engeller. Yastık kuvveti, malzemenin kontrollü akışında kritik öneme sahiptir. Yastık, hidrolik, mekanik veya pnömatik sistemlerle ayarlanabilir. - Kalıp Sac Besleme Mekanizması:
Bazı sistemlerde sac malzemenin kalıba düzgün şekilde beslenmesini sağlar ve pozisyonlamayı garanti eder.
Derin Sıvama Kalıplarının Tasarım Özellikleri
- Köşe Radyusları:
Kalıp köşelerinin uygun yarıçapta tasarlanması, sacın yırtılmadan ve buruşmadan akmasını sağlar. Çok küçük radyuslar malzemede gerilme birikimine ve çatlamaya yol açabilir. - Kalıp Boşluğu:
Sacın sıkışmadan ve aşırı deformasyona uğramadan şekillenmesi için boşluklar doğru hesaplanmalıdır. - Yastık Kuvvetinin Ayarlanabilirliği:
Her malzeme ve ürün tipi için optimum yastık kuvveti farklıdır. Kalıplarda bu kuvvetin hassas ayarlanabilir olması gerekir. - Soğutma ve Yağlama Kanalları:
Kalıp yüzeyinin ısısını dengelemek ve sürtünmeyi azaltmak için özel kanallar ve sistemler entegre edilir.
Kalıp Çeşitleri
- Tek Aşamalı Kalıplar:
Tek bir işlemde parçayı şekillendirir. Basit ve seri üretim için uygundur. - Çok Aşamalı (İstasyonlu) Kalıplar:
Parçanın karmaşık geometrilerde aşamalı olarak şekillendirilmesi için kullanılır. Birden fazla iş istasyonu içerir. - Modüler Kalıplar:
Farklı ürünler için değiştirilebilir kalıp parçalarına sahip sistemlerdir; esnek üretim imkanı sağlar.
Malzeme ve İşleme Kalitesi
Derin sıvama kalıpları genellikle yüksek sertlik ve aşınma direncine sahip özel çelik alaşımlarından (örneğin H13, P20) üretilir. Yüzey işlemleri (parlatma, kaplama) kalıp ömrünü ve parçanın yüzey kalitesini artırır.
Sonuç
Derin sıvama kalıpları, malzemenin istenilen şekle hassas ve sorunsuz şekilde ulaşması için tasarlanmış karmaşık ve kritik bileşenlerdir. Kalıp tasarımı, malzeme seçimi ve proses parametreleri bir arada optimize edilerek yüksek kaliteli, ölçüsel hassasiyette ve dayanıklı parçalar üretilebilir. Modern üretim süreçlerinde kalıp teknolojisi, derin sıvama işleminin başarısında temel rol oynar.
Derin sıvama kalıpları, ince sac metallerin istenilen şekle dönüştürülmesi sürecinde kritik bir rol oynar. Bu kalıplar, sacın kontrollü bir şekilde kalıp boşluğu içine akmasını sağlayarak, malzemenin buruşmasını, yırtılmasını ve deformasyonlarını engeller. Kalıbın temel bileşenleri arasında ana kalıp yani punch, kalıp gövdesi ve yastık (blank holder) yer alır. Punch, sacı şekillendiren parça olup, malzemeye gerekli basıncı uygulayarak onun nihai formunu oluşturur. Kalıp gövdesi ise punch ile birlikte çalışarak sacı destekler ve doğru pozisyonda tutar. Yastık ise sacın kenarlarını sıkıca tutarak, malzemenin kalıp içinde kontrollü bir şekilde akmasını sağlar ve buruşmayı önler.
Kalıp tasarımında en önemli unsurlardan biri, köşe yarıçaplarının uygun şekilde belirlenmesidir. Çok küçük köşe yarıçapları, malzemede gerilme birikimine neden olarak çatlama riskini artırabilirken, çok büyük yarıçaplar ise şekillendirme kalitesini düşürür. Kalıp boşluğu, sacın sıkışmadan ve sağlıklı bir şekilde şekillenebilmesi için doğru ölçüde olmalıdır. Ayrıca, yastık kuvvetinin ayarlanabilir olması, farklı malzeme türleri ve kalınlıkları için prosesin optimize edilmesini sağlar. Kalıpların yüzeyinde genellikle sürtünmeyi azaltmak ve ısının dengeli dağılmasını sağlamak amacıyla yağlama ve soğutma kanalları bulunur. Bu kanallar, kalıp ömrünü uzatırken, işlem kalitesini ve üretim hızını artırır.
Derin sıvama kalıpları, kullanım amaçlarına göre farklı türlerde olabilir. Tek aşamalı kalıplar, parçayı tek seferde şekillendirir ve genellikle basit geometrilere sahip ürünler için tercih edilir. Çok aşamalı ya da istasyonlu kalıplar ise karmaşık parçaların aşamalı olarak şekillendirilmesi için kullanılır. Bu kalıplar birden fazla işlem istasyonuna sahiptir ve her aşamada farklı şekillendirme işlemi gerçekleştirilir. Modüler kalıplar ise, üretimde esneklik sağlamak için farklı ürün tiplerine göre değiştirilebilir parçalardan oluşur.
Kalıplar, yüksek sertlik ve aşınma direnci gerektirdiğinden, genellikle özel alaşımlı çeliklerden üretilir. H13 ve P20 gibi çelik türleri, kalıpların uzun ömürlü olmasını sağlar. Ayrıca kalıp yüzeylerinin parlatılması veya kaplanması, hem parçanın yüzey kalitesini yükseltir hem de kalıbın aşınma direncini artırır.
Sonuç olarak, derin sıvama kalıpları, ince sac metalin karmaşık ve hassas şekillerde üretilebilmesi için vazgeçilmezdir. Kalıp tasarımının doğru yapılması, malzeme özelliklerine uygun kalıp seçimi ve proses parametrelerinin optimize edilmesiyle, yüksek kaliteli, dayanıklı ve ölçüsel hassasiyete sahip ürünler elde edilir. Modern üretim tesislerinde kalıp teknolojisi, derin sıvama işleminin başarısını doğrudan etkileyen temel unsurlardan biridir ve sürekli gelişim gösteren bir alandır.
Derin sıvama kalıplarının üretim süreci de son derece titizlik gerektirir. Kalıp üretiminde yüksek hassasiyetli CNC makineleri kullanılır ve kalıbın tüm yüzeyleri, parça tasarımına uygun şekilde işlenir. Kalıp parçalarının montajı ve ayarlanması, işlem sırasında optimal performans ve uzun kalıp ömrü için kritik öneme sahiptir. Ayrıca, kalıp tasarım aşamasında simülasyon programları kullanılarak sacın kalıp içinde nasıl hareket edeceği, hangi bölgelerde gerilme birikimi olacağı veya buruşma riski taşıyacağı önceden analiz edilir. Bu sayede kalıp ve proses tasarımı optimize edilerek, üretim sırasında hataların ve firelerin minimize edilmesi sağlanır.
Kalıpların bakımı ve onarımı da üretim verimliliği açısından önemli bir konudur. Düzenli bakım yapılmayan kalıplarda, aşınma ve deformasyonlar meydana gelir, bu da parça kalitesinin düşmesine ve üretim duruşlarına sebep olur. Modern üretim tesislerinde kalıp durumu sensörlerle takip edilir, aşınma tespit edildiğinde zamanında müdahale edilir. Bu yaklaşımla, kalıp ömrü maksimize edilir ve beklenmedik arızaların önüne geçilir.
Son yıllarda derin sıvama kalıplarında kullanılan malzeme ve kaplama teknolojileri de gelişmektedir. Örneğin, nitrürleme, PVD kaplamalar veya hard chrome kaplamalar kalıp yüzeylerinin sertliğini ve aşınma direncini artırmak için yaygın olarak uygulanmaktadır. Bu tür kaplamalar, hem kalıp performansını iyileştirir hem de kalıp yüzeyinde sürtünmeyi azaltarak işlem sırasında malzemenin daha kolay ve düzgün şekillenmesini sağlar.
Gelecekte, derin sıvama kalıplarında yapay zeka destekli tasarım ve üretim tekniklerinin daha fazla kullanılması beklenmektedir. Bu teknolojiler, kalıp tasarımında optimum geometrilerin otomatik olarak belirlenmesini, üretim süreçlerinin gerçek zamanlı izlenmesini ve hızlı müdahaleleri mümkün kılarak verimliliği artıracaktır.
Özetle, derin sıvama kalıpları, metal şekillendirme endüstrisinin en kritik ekipmanları arasında yer alır. Kalıp tasarımı, üretimi, bakımı ve teknolojik gelişmelerin sürekli takibi, yüksek kaliteli ve ekonomik üretimin temel taşlarındandır. İyi tasarlanmış ve bakımı düzenli yapılan kalıplar sayesinde, derin sıvama işlemi çok çeşitli sektörlerde güvenilir ve yüksek performanslı ürünlerin üretilmesine olanak tanır.
Derin sıvama kalıplarının önemi, sadece parçaların doğru formda üretilmesiyle sınırlı kalmaz; aynı zamanda üretim sürecinin ekonomikliği ve sürekliliği açısından da kritik bir rol oynar. Kalıp kalitesindeki bir düşüş, parça kalitesinde bozulmaya ve üretim hattında aksamalara yol açar. Bu nedenle, kalıp üretiminde yüksek kaliteli malzeme kullanımı ve ileri mühendislik teknikleri olmazsa olmazdır. Kalıp tasarımında kullanılan bilgisayar destekli mühendislik (CAE) ve bilgisayar destekli tasarım (CAD) programları sayesinde, kalıp performansı daha üretim başlamadan önce simüle edilerek olası problemler önceden belirlenir ve düzeltilir. Bu durum, zaman ve maliyet açısından büyük tasarruf sağlar.
Ayrıca, modern derin sıvama kalıplarında modülerlik giderek daha fazla önem kazanmaktadır. Modüler kalıp sistemleri, farklı parçaların üretimi için kalıp elemanlarının hızlı ve kolay değiştirilmesine olanak verir. Bu da özellikle çok ürünlü ve küçük serili üretimlerde büyük esneklik sağlar. Modüler kalıplar, yatırım maliyetlerini düşürürken, üretim sürekliliğini ve verimliliği artırır.
Teknolojideki gelişmeler, kalıp tasarımı ve üretiminde yeni malzeme ve kaplama yöntemlerinin kullanılmasını da beraberinde getirmiştir. Örneğin, seramik kaplamalar ve mikro yapılı yüzey işlemleri, kalıp yüzeylerinin aşınma direncini artırmakla kalmaz, aynı zamanda sac ile kalıp arasındaki sürtünmeyi azaltarak daha pürüzsüz yüzey kalitesi elde edilmesini sağlar. Bu gelişmeler, kalıp ömrünü uzatırken ürün kalitesinde de iyileşme sağlar.
Son olarak, endüstri 4.0 teknolojilerinin entegre edilmesiyle derin sıvama kalıpları artık sadece statik araçlar olmaktan çıkmış, akıllı sistemlerin parçası haline gelmiştir. Kalıplara yerleştirilen sensörler sayesinde sıcaklık, basınç ve deformasyon gibi parametreler anlık olarak izlenebilir ve analiz edilebilir. Bu sayede, üretim süreçleri daha iyi kontrol edilip optimize edilebilir, önleyici bakım stratejileri uygulanabilir ve olası arızalar önceden tespit edilerek üretim duruşları minimize edilir.
Tüm bu gelişmeler ışığında, derin sıvama kalıpları üretim sürecinde kalite, hız, ekonomik verimlilik ve esnekliği sağlayan temel unsurlar olarak önemini korumakta ve gelecekte de bu rolünü daha da güçlendirerek sürdürecektir.
Bakım, Güvenlik ve Operatör Eğitimi
Derin sıvama preslerinin verimli ve güvenli şekilde çalışması, düzenli bakım, doğru güvenlik uygulamaları ve iyi eğitimli operatörlerle mümkün olur. Bu üç unsur, hem üretim kalitesini artırır hem de iş kazalarının önüne geçerek iş sağlığı ve güvenliğini sağlar.
Bakım
Derin sıvama makinelerinin düzenli bakımı, makinenin ömrünü uzatır ve arızaları önler. Bakım programları; hidrolik sistemlerin yağ seviyelerinin kontrolü, filtrelerin temizliği, mekanik aksamların yağlanması ve kalibrasyon işlemlerini kapsar. Ayrıca kalıp yüzeylerinin ve yastık sistemlerinin durumu düzenli olarak incelenmeli, aşınma veya deformasyon durumunda gerekli müdahaleler yapılmalıdır. Proaktif bakım yaklaşımları sayesinde beklenmedik duruş süreleri minimize edilir.
Güvenlik
Preslerde iş güvenliği çok önemlidir. Makine çalışma alanlarında koruyucu bariyerler, acil durdurma butonları ve güvenlik sensörleri mutlaka bulunmalıdır. Operatörlerin pres hareketlerinden korunması için makine otomasyon sistemleri güvenlik standartlarına uygun tasarlanmalı ve periyodik olarak test edilmelidir. Ayrıca presin çalıştığı ortamın temiz, aydınlık ve ergonomik olması kaza riskini azaltır.
Operatör Eğitimi
Pres operatörleri, makinenin çalışma prensipleri, acil durum prosedürleri ve güvenlik kuralları konusunda kapsamlı bir şekilde eğitilmelidir. Eğitimler; makine kurulumu, parametre ayarları, malzeme besleme ve parça çıkarma, hata tespiti ve müdahale yöntemlerini içermelidir. Ayrıca operatörlerin, makineyi doğru ve verimli kullanabilmesi için düzenli olarak güncel teknik bilgi ve uygulama eğitimleri almaları sağlanmalıdır.
Sonuç
Derin sıvama preslerinde düzenli bakım, sıkı güvenlik önlemleri ve nitelikli operatör eğitimi, hem üretim verimliliğini hem de iş sağlığı ve güvenliğini artırır. Bu faktörler, makinelerin uzun ömürlü çalışmasını sağlarken, iş kazalarının önlenmesi ve kaliteli ürün elde edilmesinde temel rol oynar. Endüstride başarılı bir üretim süreci için bu unsurların bir bütün halinde ele alınması gereklidir.
Bakım süreçlerinde kullanılan ekipman ve yöntemlerin doğru seçilmesi de önem taşır. Hidrolik yağının kalitesi ve uygunluğu düzenli olarak kontrol edilmeli, gerektiğinde değiştirilmelidir. Kirli veya eski hidrolik yağları, sistemde tıkanmalara ve aşınmalara yol açarak pres performansını olumsuz etkiler. Mekanik parçalar için uygun yağlayıcıların kullanılması, hareketli bileşenlerin sorunsuz çalışmasını sağlar ve aşınmayı azaltır. Ayrıca kalıp yüzeylerinin temizliği, özellikle işlem sonrası kalıntıların ve yağ artıklarının giderilmesi, kalıp ömrünü artıran kritik bir adımdır.
Operatörlerin eğitimi, sadece başlangıç aşamasında değil, üretim sürecinin tüm aşamalarında devam ettirilmelidir. Teknolojik gelişmeler ve yeni makinelerle birlikte operatörlerin bilgi seviyesini güncel tutmak, verimliliği ve iş güvenliğini artırır. Operatörlerin, acil durumlarda hızlı ve doğru müdahale edebilmeleri için tatbikatlar ve simülasyonlarla desteklenen uygulamalı eğitimler düzenlenmelidir. Ayrıca iş güvenliği kültürünün yaygınlaştırılması ve sürekli hatırlatmalarla operatörlerin dikkatinin yüksek tutulması önemlidir.
Güvenlik açısından, derin sıvama preslerinde risk analizi yapılmalı ve riskler minimize edilmelidir. Presin hareketli kısımlarına erişim, sadece bakım ve onarım anlarında kontrollü şekilde sağlanmalı, normal çalışma sırasında operatörlerin bu bölgelere yaklaşması engellenmelidir. Makine güvenlik sistemleri düzenli aralıklarla test edilmeli, arızalar hemen giderilmelidir. Ayrıca kişisel koruyucu donanımların (KKD) kullanımı zorunlu hale getirilmeli ve operatörlerin bu donanımları doğru kullanmaları sağlanmalıdır.
Sonuç olarak, derin sıvama preslerinde etkin bakım uygulamaları, kapsamlı operatör eğitimi ve titiz güvenlik önlemleri bir araya geldiğinde, hem üretim kalitesi yükselir hem de iş yerinde kaza riskleri önemli ölçüde azalır. Bu faktörler, uzun vadede işletme verimliliği ve sürdürülebilirliği için temel unsurlardır ve kesinlikle göz ardı edilmemelidir.
Ayrıca, modern fabrikalarda bakım ve güvenlik süreçlerinde dijital teknolojilerin kullanımı giderek yaygınlaşmaktadır. Endüstri 4.0 yaklaşımı kapsamında, presler üzerinde yer alan sensörler ve IoT (Nesnelerin İnterneti) sistemleri sayesinde makinenin çalışma durumu gerçek zamanlı olarak izlenebilir. Bu sayede potansiyel arızalar önceden tespit edilerek önleyici bakım planları yapılabilir ve beklenmedik duruş süreleri minimize edilir. Ayrıca, operatörlerin makinelerle etkileşimi için gelişmiş kullanıcı arayüzleri ve dokunmatik ekranlar kullanılarak, makineyi daha kolay ve güvenli şekilde kontrol etmeleri sağlanır.
Operatör eğitimi açısından da sanal gerçeklik (VR) ve artırılmış gerçeklik (AR) teknolojileri ile simülasyon tabanlı eğitimler sunulmaya başlanmıştır. Bu yöntemler, operatörlerin gerçek makineyle temas etmeden önce süreçleri öğrenmelerine, olası tehlikeleri deneyimlemelerine ve müdahale becerilerini geliştirmelerine olanak tanır. Böylece iş güvenliği kültürü daha etkin şekilde benimsenir.
Güvenlik protokollerinin sürekli güncellenmesi ve işletme çalışanlarına düzenli olarak hatırlatılması da önemli bir uygulamadır. İş kazalarının önlenmesinde çalışanların bilinçlendirilmesi ve katılımı esastır. Bu nedenle, iş sağlığı ve güvenliği toplantıları, görsel uyarılar ve eğitim seminerleri düzenli olarak yapılmalıdır.
Sonuç olarak, derin sıvama preslerinde bakım, güvenlik ve operatör eğitimi; teknolojik gelişmelerle desteklendiğinde, işletmenin üretim kalitesini, çalışan güvenliğini ve operasyonel verimliliğini en üst seviyeye çıkarır. Bu üç unsurun bütünleşik ve disiplinli yönetimi, modern üretim tesislerinde sürdürülebilir başarı için vazgeçilmezdir.
Hidrolik Sıvama Presin çalışma prensibi
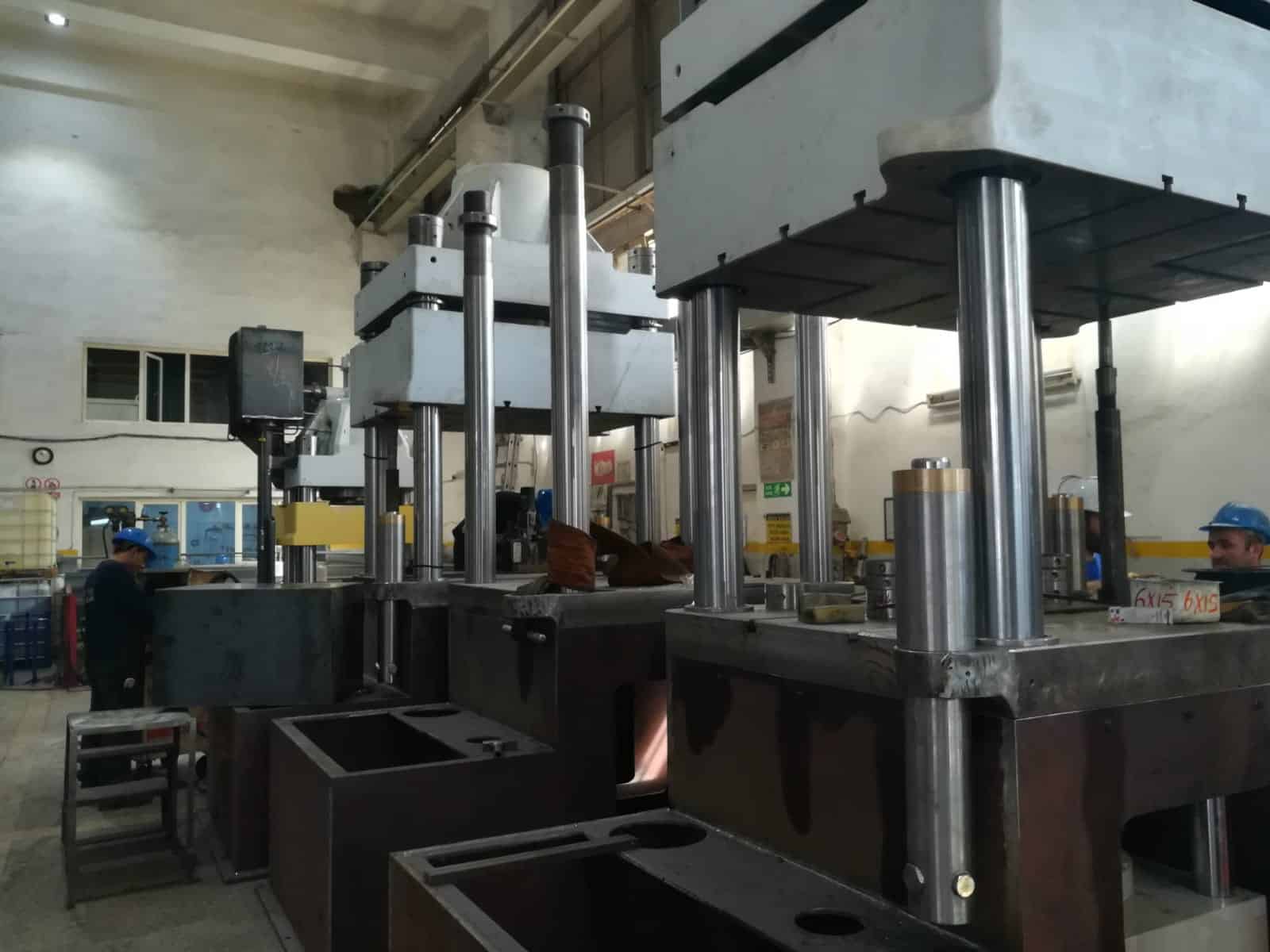
Hidrolik sıvama presi, ince sac metalin istenilen şekle dönüştürülmesi için hidrolik basınç kuvveti kullanan bir makinedir. Temel olarak, sac malzeme kalıp boşluğuna yerleştirilir ve hidrolik sistem tarafından kontrollü bir şekilde yüksek basınç uygulanarak malzeme kalıp içine doğru yumuşak ve kontrollü bir şekilde şekillendirilir. Bu prensip, malzemenin yırtılmadan, buruşmadan ve düzgün bir şekilde şekillenmesini sağlar.
Çalışma süreci genel olarak şu adımlardan oluşur: Öncelikle sac malzeme kalıp alanına yerleştirilir. Ardından, blank holder (yastık) olarak adlandırılan parça, sacın kenarlarını sıkıca tutar; bu, sacın kalıp içinde istenmeyen hareketler yapmasını önleyerek buruşmayı engeller. Daha sonra hidrolik piston devreye girer ve sıvı basıncı sayesinde sac üzerine kontrollü kuvvet uygular. Hidrolik basınç, sacın kalıp içindeki boşluğa yavaş ve eşit şekilde akmasını sağlayarak derin ve karmaşık şekillerin elde edilmesini mümkün kılar.
Hidrolik sıvama preslerinde basınç ve hareket hızı elektronik kontrol sistemleriyle hassas şekilde ayarlanabilir. Bu sayede, farklı malzeme türlerine ve ürün geometrilerine uygun parametreler kolayca uygulanabilir. Hidrolik sistemin sunduğu yumuşak ve kesintisiz güç aktarımı, mekanik preslere kıyasla daha az malzeme gerilmesi ve daha yüksek kalite sağlar.
Sonuç olarak, hidrolik sıvama presi çalışma prensibi; sac malzemenin kalıp içine kontrollü ve eşit basınç altında yumuşak şekilde itilmesi esasına dayanır. Bu prensip, derin sıvama işleminin temelini oluşturur ve hassas, kaliteli metal parçaların üretimini mümkün kılar.
Hidrolik sıvama presinde kullanılan hidrolik sistem, yüksek basınçlı sıvının pistonlara iletilmesiyle çalışır. Bu sıvı genellikle özel hidrolik yağdır ve basınç altında pistonları hareket ettirerek kalıp üzerindeki kuvveti oluşturur. Pistonun hareketi, pres tablası ve kalıbı üzerinden sac malzemeye aktarılır. Bu sayede sac, kalıbın şekline uygun olarak derinlemesine çekilir veya sıvanır.
Presin en önemli unsurlarından biri olan blank holder (yastık), sacın kenarlarını tutarken, aynı zamanda malzemenin kalıp içinde kontrollü bir şekilde akmasını sağlar. Yastık kuvveti, hidrolik veya mekanik sistemlerle ayarlanabilir; doğru kuvvet uygulanmazsa sac buruşabilir veya yırtılabilir. Bu nedenle yastık kuvvetinin hassas şekilde kontrolü, pres performansı için kritiktir.
Hidrolik sıvama preslerinde hareketler genellikle çok daha yumuşak ve kontrollüdür. Bu, malzemede oluşan gerilme ve deformasyonları azaltır, böylece ince sacların bile kolayca ve hasarsız şekillendirilmesini sağlar. Presin hareket hızı ve kuvveti üretim sırasında elektronik kontrol panelleri aracılığıyla programlanabilir; böylece farklı parça tasarımlarına hızlıca adapte olunabilir.
Bunun yanı sıra, hidrolik sıvama presleri enerji verimliliği açısından da avantaj sağlar. Hidrolik sistemler, gerektiği kadar basınç üretir ve bu sayede gereksiz enerji tüketimi önlenir. Ayrıca, hidrolik presler sessiz çalışır ve mekanik preslere kıyasla daha az titreşim üretir.
Özetle, hidrolik sıvama presinin çalışma prensibi; hidrolik basınçla malzemeye kontrollü, eşit ve yumuşak kuvvet uygulanarak sacın kalıp içine şekillendirilmesini sağlamaktır. Bu sayede hassas, karmaşık ve derin şekillendirme işlemleri yüksek kalite ve düşük hata oranıyla gerçekleştirilebilir.
Hidrolik sıvama preslerinde prosesin başarılı olması için basınç, hız ve pozisyon gibi parametrelerin dikkatli bir şekilde kontrol edilmesi gerekir. Basınç çok yüksek olursa malzeme yırtılabilir, çok düşük olursa ise istenilen şekil tam oluşmayabilir. Bu yüzden modern preslerde, işlem boyunca bu parametreler gerçek zamanlı olarak izlenir ve gerektiğinde otomatik olarak ayarlanır. Ayrıca presin strok uzunluğu, yani pistonun hareket mesafesi, kalıp ve ürün tasarımına göre programlanabilir; böylece malzeme kalıba tam olarak uyum sağlar.
Sıvama işlemi sırasında sac malzemenin kalıp içinde homojen şekilde akması, kalınlık farklarının ve yüzey kusurlarının minimumda tutulmasını sağlar. Hidrolik sıvama preslerinde, malzemenin bu şekilde akışı, geleneksel mekanik preslere kıyasla daha kontrollü ve hassastır. Bu da ince ve hassas sacların, çatlama veya buruşma olmadan derin şekiller almasına imkan verir.
İşlem sonunda, pres geri çekilir ve şekillenen parça kalıptan çıkarılır. Otomatik sistemlerde bu çıkarma işlemi robotlar veya pnömatik ekipmanlar yardımıyla hızlı ve güvenli bir şekilde yapılır. Böylece üretim hattının verimliliği artırılır ve operatörlerin iş güvenliği sağlanır.
Sonuç olarak, hidrolik sıvama presinin çalışma prensibi; hidrolik basınç ve hareketlerin kontrollü şekilde yönetilerek, malzemenin kalıp içinde istenilen formda ve yüksek kalitede şekillendirilmesini sağlamaktır. Bu prensip, metal şekillendirme sektöründe hassas ve karmaşık parçaların üretiminde önemli avantajlar sunar ve günümüzde birçok endüstride yaygın olarak kullanılmaktadır.
Hidrolik Pres
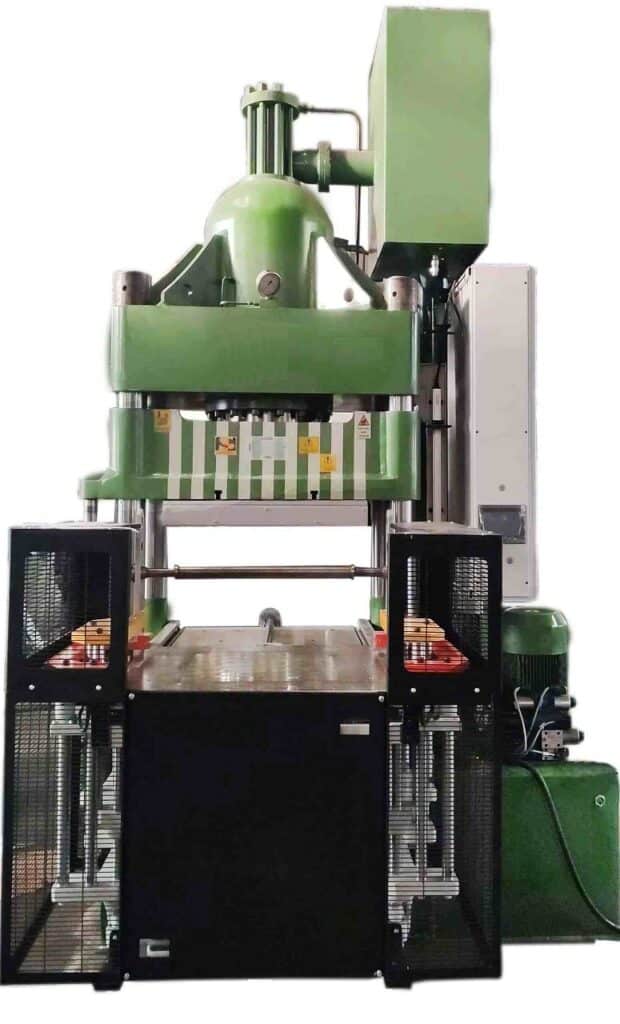
Hidrolik pres, sıvıların basınç iletme özelliğinden yararlanarak büyük kuvvetlerin elde edilmesini sağlayan bir makinedir. Temel prensibi, küçük bir alana uygulanan kuvvetin, basınç yoluyla daha büyük bir alana aktarılması ve böylece daha büyük bir kuvvet üretilmesidir. Bu prensip, Pascal Kanunu olarak bilinir ve hidrolik preslerin çalışma temelini oluşturur.
Hidrolik preslerde genellikle iki silindir bulunur; biri küçük çaplı piston ve diğeri büyük çaplı pistondur. Küçük pistona uygulanan kuvvet, hidrolik sıvı aracılığıyla büyük pistona aktarılır. Bu sayede, küçük bir kuvvetle, çok daha büyük kuvvetler elde edilir. Bu kuvvet, metal şekillendirme, presleme, bükme, kesme gibi birçok endüstriyel uygulamada kullanılır.
Hidrolik preslerin avantajları arasında yüksek kuvvet üretme kapasitesi, kuvvetin hassas kontrol edilebilmesi, çalışma sırasında sessiz ve yumuşak hareket sunması yer alır. Ayrıca, presin kuvveti ve hareket hızı elektronik olarak programlanabilir, bu da farklı işlem ihtiyaçlarına kolay adaptasyon sağlar.
Endüstride hidrolik presler; metal şekillendirme (sıvama, bükme, presleme), plastik şekillendirme, kauçuk işleme, kalıplama, montaj işlemleri ve geri dönüşüm gibi geniş bir yelpazede kullanılır. Dayanıklı yapısı ve esnek kullanım alanlarıyla birçok sektörde vazgeçilmez bir ekipmandır.
Özetle, hidrolik pres, sıvı basıncıyla büyük kuvvetler üreterek malzeme şekillendirme ve işleme işlemlerinde etkin ve kontrollü bir çözüm sunan makinedir. Geniş uygulama alanı ve teknoloji entegrasyonları sayesinde modern sanayinin temel makinalarından biri olarak kabul edilir.
Hidrolik pres, sıvıların basınç iletme özelliğinden yararlanarak büyük kuvvetlerin elde edilmesini sağlayan bir makinedir. Çalışma prensibi, Pascal Kanunu’na dayanır; bu kanuna göre kapalı bir sistemde bir noktaya uygulanan basınç, sistemdeki her noktaya eşit olarak iletilir. Hidrolik preslerde genellikle iki piston bulunur. Küçük pistona uygulanan kuvvet, hidrolik sıvı aracılığıyla büyük pistona aktarılır ve burada çok daha büyük bir kuvvet ortaya çıkar. Bu mekanizma sayesinde, nispeten düşük güçle yüksek kuvvetler elde edilerek metal şekillendirme, presleme, kesme, bükme gibi işlemler gerçekleştirilebilir.
Hidrolik preslerin en önemli avantajlarından biri, kuvvetin hassas ve kontrollü bir şekilde ayarlanabilmesidir. Presin kuvveti, basınç seviyesi ve piston hareket hızı elektronik kontrol sistemleriyle kolayca programlanabilir. Bu sayede farklı malzeme türlerine ve işlem gereksinimlerine hızlıca uyum sağlanır. Ayrıca hidrolik sistemler, mekanik preslere kıyasla daha yumuşak ve sessiz çalışır, bu da üretim sırasında oluşabilecek titreşim ve gürültüyü azaltır.
Endüstride hidrolik presler çok geniş bir kullanım alanına sahiptir. Metal şekillendirme proseslerinde, özellikle kalıplı işlemler, derin sıvama, bükme ve kesme işlemlerinde tercih edilir. Bunun yanı sıra plastik ve kauçuk parçaların şekillendirilmesinde, montaj işlemlerinde ve geri dönüşüm sektöründe de yaygın olarak kullanılır. Preslerin dayanıklı yapısı ve yüksek kuvvet kapasitesi, onları zorlu üretim koşullarında güvenilir kılar.
Modern hidrolik preslerde ayrıca enerji verimliliğini artıran ve bakım ihtiyaçlarını azaltan gelişmiş teknolojiler kullanılır. Servo-hidrolik sistemler ve değişken debili pompalar sayesinde enerji tüketimi optimize edilir. Bunun yanında, basınç, sıcaklık ve hareket parametrelerini izleyen sensörlerle donatılan presler, proses kontrolünü iyileştirir ve arıza risklerini azaltır.
Sonuç olarak, hidrolik presler büyük kuvvetlerin kontrollü ve hassas bir şekilde uygulanmasını sağlayan, çok yönlü ve güçlü makineler olarak endüstride önemli bir yer tutar. Teknolojik gelişmelerle birlikte giderek daha verimli, esnek ve kullanıcı dostu hale gelerek, modern üretim süreçlerinin vazgeçilmez ekipmanlarından biri olmaya devam etmektedir.
Hidrolik preslerin kullanımında güvenlik ve operatör eğitimi de büyük önem taşır. Operatörlerin, presin çalışma prensiplerini, güvenlik önlemlerini ve acil durum prosedürlerini iyi bilmeleri gerekir. Bu sayede iş kazalarının önüne geçilir ve makinenin verimli kullanımı sağlanır. Ayrıca düzenli bakım programlarının uygulanması, presin ömrünü uzatır ve üretim kalitesini artırır. Hidrolik sistemdeki yağ seviyelerinin kontrolü, filtrelerin temizliği ve mekanik parçaların düzenli yağlanması gibi işlemler, presin sorunsuz çalışması için gereklidir. Günümüzde birçok hidrolik pres, gelişmiş kontrol sistemleri ve sensörlerle donatılmış olup, bu sayede operasyon sırasında anlık veri takibi yapılabilir. Bu veriler operatörlere, bakım ekiplerine ve üretim yöneticilerine gerçek zamanlı geri bildirim sağlayarak, olası sorunların önceden tespit edilmesine olanak tanır. Böylece hem üretim kayıpları azaltılır hem de iş güvenliği artırılır. Teknolojinin ilerlemesiyle hidrolik preslerde otomasyon ve dijitalleşme giderek artmakta, bu da hem üretim verimliliğini hem de operasyonel güvenliği üst seviyeye taşımaktadır. Genel olarak hidrolik presler, sanayinin pek çok alanında vazgeçilmez makineler olup, doğru kullanıldığında yüksek performans ve uzun ömür sunar.
Hidrolik preslerin endüstride bu kadar yaygın kullanılmasının bir diğer sebebi de esneklik ve uyarlanabilirlik özellikleridir. Farklı büyüklükte ve kalınlıkta malzemelerin işlenebilmesi için presin basınç kapasitesi ve strok mesafesi kolayca ayarlanabilir. Bu sayede, aynı makine üzerinde farklı ürünlerin üretimi mümkün olur. Ayrıca, hidrolik sistemlerin yapısı gereği ani duruş ve geri dönüş hareketleri oldukça kontrollüdür; bu da hem malzemenin zarar görmesini engeller hem de operatör için güvenli bir çalışma ortamı yaratır. Üretim hatlarında hidrolik preslerin robotlarla entegrasyonu, otomatik besleme ve boşaltma sistemleri ile desteklenerek, yüksek verimlilik ve düşük işçilik maliyeti sağlanır. Böylelikle hem seri üretim hem de küçük seriler için uygun çözümler sunulur. Günümüzde, hidrolik pres teknolojisi sürekli gelişmekte ve enerji tasarrufu, çevre dostu çalışma ve dijital kontrol sistemleri gibi yeniliklerle endüstrinin ihtiyaçlarına cevap vermeye devam etmektedir. Bu özellikler hidrolik presleri, modern üretim tesislerinin vazgeçilmez makineleri haline getirmektedir.
Hidrolik presler, modern sanayide metal şekillendirme başta olmak üzere birçok üretim sürecinde temel ekipmanlardan biri olarak yer alır. Bu makinelerin temel avantajlarından biri, yüksek kuvvet üretme kapasitesi ve bu kuvvetin hassas bir şekilde kontrol edilebilmesidir. Hidrolik sistemler, sıvıların basınç iletme özelliğini kullanarak küçük bir giriş kuvvetini büyük bir çıkış kuvvetine dönüştürür. Bu mekanizma, ağır ve dayanıklı malzemelerin kolaylıkla şekillendirilmesine, kesilmesine, bükülmesine ve preslenmesine olanak sağlar. Hidrolik presler, özellikle büyük boyutlu ve kalın metal parçaların işlenmesinde mekanik preslere kıyasla daha etkili ve esnek çözümler sunar.
Presin çalışma prensibi, Pascal Kanunu üzerine kuruludur. Kapalı bir sistemde basınç, sistemin her noktasına eşit olarak iletilir. Hidrolik preslerde, küçük çaplı piston üzerine uygulanan kuvvet, hidrolik sıvı aracılığıyla daha büyük çaplı pistona iletilir ve burada kuvvet katlanarak artar. Bu sayede, operatörün uyguladığı küçük bir kuvvet, metal üzerinde binlerce kilogramlık basınca dönüşür. Bu kuvvet sayesinde, sac ve metal parçalar istendiği gibi şekillendirilebilir. Hidrolik preslerde piston hareketi hidrolik sıvının basıncıyla sağlanır ve bu hareket oldukça yumuşak ve kontrollüdür. Bu kontrol, özellikle hassas ve karmaşık şekillendirme işlemlerinde çok önemlidir.
Teknolojik gelişmelerle birlikte, hidrolik preslerin kontrol sistemleri de büyük ölçüde ilerlemiştir. Günümüzde presler, gelişmiş elektronik kontrol üniteleri ve sensörlerle donatılarak, kuvvet, hız, pozisyon ve basınç gibi parametreler gerçek zamanlı izlenir ve ayarlanabilir. Bu sayede farklı malzeme türlerine ve işlem gereksinimlerine hızlıca adapte olunabilir. Otomasyon sistemleri ile entegre edilen hidrolik preslerde, üretim süreçleri daha verimli hale gelirken, insan hatası riski de minimize edilir. Ayrıca bu sistemler, enerji tüketimini optimize etmek ve bakım gereksinimlerini azaltmak için de kullanılır.
Endüstride hidrolik presler, otomotivden havacılığa, mobilya üretiminden beyaz eşyaya kadar geniş bir alanda kullanılır. Metal parçaların preslenmesi, bükülmesi, kesilmesi, şekillendirilmesi ve montaj işlemlerinde vazgeçilmezdirler. Özellikle derin sıvama gibi karmaşık şekillendirme proseslerinde hidrolik presler, malzemenin kontrollü ve eşit şekilde kalıp içine akmasını sağlar. Böylece yüksek kaliteli, hassas ve dayanıklı ürünler elde edilir. Ayrıca hidrolik presler, plastik enjeksiyon kalıplama ve kauçuk şekillendirme gibi işlemlerde de sıklıkla tercih edilir.
Hidrolik preslerin kullanımında iş güvenliği ve operatör eğitimi çok önemlidir. Presler yüksek kuvvet ürettiğinden, çalışma sırasında olası kazaları önlemek için güvenlik donanımları ve koruyucular mutlaka kullanılmalıdır. Operatörlerin presin çalışma prensiplerini, acil durum prosedürlerini ve güvenlik önlemlerini iyi bilmeleri gerekir. Ayrıca düzenli bakım ve kontroller, presin uzun ömürlü ve verimli çalışmasını sağlar. Hidrolik sistemin yağ seviyeleri ve filtreleri düzenli olarak kontrol edilmeli, aşınan parçalar zamanında değiştirilmelidir. Bu bakımlar sayesinde, beklenmedik arızalar önlenir ve üretim sürekliliği sağlanır.
Son yıllarda hidrolik pres teknolojisinde enerji verimliliği ve çevre dostu uygulamalar ön plana çıkmaktadır. Servo motorlu hidrolik sistemler ve değişken debili pompalar kullanılarak, enerji tüketimi önemli ölçüde azaltılmaktadır. Aynı zamanda, daha az yağ kullanımı ve atık yağ yönetimi gibi çevresel etkileri minimize eden yöntemler geliştirilmektedir. Bu gelişmeler, hem işletmelerin maliyetlerini düşürür hem de sürdürülebilir üretim hedeflerine katkı sağlar.
Gelecekte hidrolik preslerde yapay zeka ve makine öğrenimi tabanlı sistemlerin entegrasyonunun artması beklenmektedir. Bu teknolojiler, üretim verilerini analiz ederek süreçleri optimize edecek, bakım ihtiyacını önceden tahmin edecek ve üretim kalitesini daha da artıracaktır. Ayrıca, sanal gerçeklik ve artırılmış gerçeklik destekli eğitim sistemleri ile operatörlerin makineleri daha güvenli ve etkili kullanmaları sağlanacaktır.
Özetle, hidrolik presler yüksek kuvvet gerektiren işlemlerde esneklik, hassasiyet ve güvenilirlik sunan makineler olarak endüstride vazgeçilmezdir. Teknolojik gelişmelerle birlikte giderek daha akıllı, verimli ve çevre dostu hale gelerek, modern üretimin temel taşlarından biri olmaya devam edecektir.
Hidrolik preslerin endüstriyel üretimde sağladığı avantajlar, onları farklı sektörlerde vazgeçilmez kılmaktadır. Özellikle metal şekillendirme alanında, kalınlık ve boyut açısından geniş bir aralığa sahip malzemelerin işlenebilmesi, hidrolik preslerin en büyük üstünlüklerinden biridir. Geleneksel mekanik preslerle karşılaştırıldığında, hidrolik presler çok daha yüksek kuvvetleri daha düşük enerji tüketimi ve daha hassas kontrolle uygulayabilir. Bu özellik, üretim kalitesinin artmasını sağlarken, malzeme israfını ve üretim hatalarını da minimuma indirir. Ayrıca hidrolik preslerin esnek yapısı sayesinde, aynı makine üzerinde farklı üretim parametreleri kolaylıkla değiştirilebilir. Bu da onları seri üretimin yanı sıra küçük ve orta ölçekli üretimlerde de ekonomik ve pratik bir çözüm haline getirir.
Hidrolik preslerin çalışma mekanizması temel olarak Pascal Kanunu’na dayansa da, modern makinelerde kullanılan gelişmiş elektronik kontrol sistemleri sayesinde süreç çok daha karmaşık ve hassas şekilde yönetilir. Basınç, hız, piston pozisyonu ve uygulanan kuvvet gibi parametreler gerçek zamanlı olarak izlenir ve ayarlanır. Bu sayede üretim esnasında ortaya çıkabilecek problemler anında tespit edilerek müdahale edilir. Örneğin, sac metalin kalıp içine doğru akışı sırasında malzemenin gerilme sınırlarını aşmaması için kuvvet ve hız ayarları sürekli kontrol edilir. Bu tür kontrollü proses yönetimi, özellikle ince sacların ve karmaşık geometrilere sahip parçaların üretiminde kritik öneme sahiptir. Aynı zamanda, bu hassasiyet üretim verimliliğini artırır ve fire oranlarını azaltır.
Hidrolik preslerin kullanım alanları oldukça geniştir. Otomotiv sektöründe motor parçalarının, şasi elemanlarının ve kaporta panellerinin üretiminde sıkça kullanılır. Mobilya ve beyaz eşya üretiminde metal aksamların şekillendirilmesi ve montaj işlemlerinde önemli rol oynar. Havacılık ve savunma sanayinde ise yüksek mukavemet gerektiren metal parçaların üretiminde tercih edilir. Ayrıca plastik ve kauçuk sektörlerinde kalıplama işlemlerinde, ambalaj endüstrisinde ise şekillendirme ve kesme işlemlerinde yaygın şekilde kullanılır. Bu çeşitlilik, hidrolik preslerin çok yönlülüğünü ve endüstrideki vazgeçilmez konumunu ortaya koyar.
İş güvenliği ve operatör eğitimi hidrolik preslerin sağlıklı ve verimli kullanımında hayati önem taşır. Yüksek kuvvetlerin kontrolsüz kullanımı, ciddi iş kazalarına neden olabilir. Bu nedenle makinelerde mutlaka acil durdurma sistemleri, koruyucu kapaklar ve sensörler bulunmalıdır. Operatörlerin de bu güvenlik donanımlarını etkin şekilde kullanabilmeleri için düzenli ve kapsamlı eğitimler almaları gerekir. Eğitimlerde makinenin çalışma prensiplerinin yanı sıra olası riskler ve acil müdahale prosedürleri detaylı şekilde anlatılmalıdır. Böylece hem iş kazalarının önüne geçilir hem de üretim sırasında ortaya çıkabilecek hatalar minimize edilir.
Bakım süreçleri de hidrolik preslerin verimli çalışması için kritik önemdedir. Hidrolik sistemlerin düzenli olarak kontrol edilmesi, yağ seviyelerinin ve filtrenin temiz tutulması presin sorunsuz çalışmasını sağlar. Mekanik aksamların yağlanması ve aşınan parçaların zamanında değiştirilmesi, beklenmedik arızaların önüne geçer. Ayrıca kalıp yüzeylerinin düzenli temizlenmesi, parçaların kalitesini doğrudan etkiler. Bakım programlarının dikkatle uygulanması, preslerin ömrünü uzatırken işletme maliyetlerini de azaltır.
Son yıllarda hidrolik pres teknolojisinde önemli gelişmeler yaşanmaktadır. Enerji verimliliğini artırmak amacıyla servo-hidrolik sistemler yaygınlaşmaktadır. Bu sistemler, ihtiyaca göre değişken debi ve basınç sağlayarak enerji tasarrufu sağlar. Ayrıca dijitalleşme ve otomasyon teknolojilerinin entegrasyonu ile presler, üretim hattının akıllı ve esnek bir parçası haline gelmiştir. Makine öğrenimi ve yapay zeka algoritmaları, üretim süreçlerinin optimize edilmesine ve bakım ihtiyaçlarının önceden tahmin edilmesine olanak tanır. Sanal ve artırılmış gerçeklik tabanlı eğitim programları ise operatörlerin yetkinliklerini artırarak iş güvenliğini destekler.
Hidrolik presler, günümüzde sadece kuvvet uygulayan makinalar olmaktan çıkıp, üretim süreçlerinin ayrılmaz bir parçası haline gelmiştir. Gelişen teknoloji ve artan otomasyon sayesinde, üretim hatlarının verimliliği, esnekliği ve güvenliği büyük ölçüde artırılmıştır. Gelecekte bu trendlerin devam etmesi, hidrolik preslerin endüstriyel üretimdeki önemini daha da artıracaktır. Yeni nesil presler, hem çevresel sürdürülebilirlik hedeflerine uygun enerji tasarruflu çalışacak hem de yüksek hassasiyetli ve kompleks üretim taleplerini karşılayabilecek donanımlara sahip olacaktır. Böylece hidrolik presler, modern üretimin vazgeçilmez teknolojik altyapılarından biri olarak kalmaya devam edecektir.
Hidrolik Derin Sıvama Presi
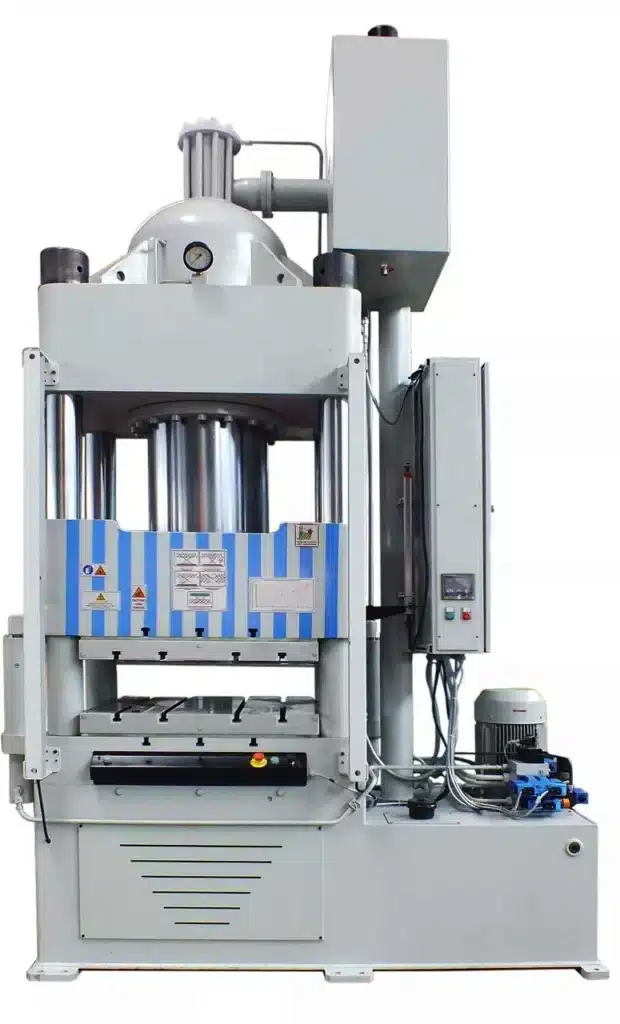
Hidrolik derin sıvama presi, ince sac metalin kalıp yardımıyla derinlemesine ve karmaşık şekillerde şekillendirilmesini sağlayan özel bir hidrolik pres türüdür. Derin sıvama işlemi, sac malzemenin kalıp içinde kontrollü ve yumuşak bir şekilde şekillendirilmesini temel alır. Bu sayede, yırtılma, buruşma veya kalınlık değişimlerinin minimum seviyede olduğu yüksek kaliteli parçalar elde edilir. Hidrolik sistemin sunduğu kesintisiz ve ayarlanabilir basınç sayesinde, özellikle otomotiv, beyaz eşya, aydınlatma ve havacılık gibi sektörlerde karmaşık ve hassas sac parça üretimi için ideal çözümler sunar.
Çalışma prensibi, hidrolik basıncın sac malzemeye kontrollü bir şekilde uygulanmasına dayanır. Sac, kalıp boşluğuna yerleştirilir ve blank holder adı verilen parça, sacın kenarlarını sıkıca tutarak malzemenin kalıp içinde sabit kalmasını sağlar. Daha sonra hidrolik piston, sıvama kuvvetini yumuşak ve eşit bir şekilde sac üzerine aktarır. Bu kuvvet, sacın kalıp içinde düzgün şekilde akmasını sağlar ve derin, karmaşık formların oluşmasına olanak tanır. Hidrolik preslerdeki bu yumuşak güç uygulaması, mekanik preslere göre daha az malzeme yıpranması ve daha uzun kalıp ömrü anlamına gelir.
Hidrolik derin sıvama presleri, farklı sac kalınlıkları ve alaşımlar için kolayca ayarlanabilir basınç ve hız parametreleri sayesinde geniş bir uygulama yelpazesine sahiptir. Bu makineler, özellikle ince ve hassas malzemelerin işlenmesinde yüksek verimlilik ve kalite sağlar. Ayrıca, proses parametrelerinin elektronik olarak kontrol edilmesi, üretim sürekliliğini artırır ve operatör hatalarını minimize eder.
Endüstride hidrolik derin sıvama presleri, otomotiv sektöründe kaporta parçalarının üretiminde, beyaz eşya sektöründe buzdolabı ve çamaşır makinesi dış panellerinde, aydınlatma sektöründe lambader ve avize parçalarında, havacılık ve savunma sanayinde yüksek dayanımlı metal bileşenlerin üretiminde yaygın olarak kullanılır. Bu presler, karmaşık geometrilere sahip parçaların yüksek hassasiyetle ve minimum fireyle üretilmesini mümkün kılar.
Modern hidrolik derin sıvama preslerinde, enerji verimliliğini artıran servo-hidrolik sistemler ve proses kontrolünü sağlayan gelişmiş elektronik kontrol üniteleri kullanılmaktadır. Ayrıca, kalıp yüzeylerinin aşınmasını azaltmak için özel kaplamalar ve bakım programları uygulanır. Operatörlerin eğitimli olması ve güvenlik standartlarına uygun çalışma ortamlarının sağlanması, üretimin kesintisiz ve güvenli olmasını destekler.
Sonuç olarak, hidrolik derin sıvama presi, hassas, kaliteli ve karmaşık metal parçaların üretiminde üstün performans sunan, esnek ve güvenilir bir teknoloji olarak sanayideki yerini sağlamlaştırmıştır. Teknolojinin gelişmesiyle birlikte, bu preslerin otomasyon ve dijitalleşme entegrasyonları artacak, üretim süreçlerinde verimlilik ve kalite standartları daha da yükselecektir.
Hidrolik derin sıvama presi, modern metal şekillendirme teknolojilerinin en önemli ve yaygın kullanılan ekipmanlarından biridir. İnce sacların karmaşık ve derin şekillerde deformasyonunu sağlamak üzere tasarlanmış bu makineler, yüksek hassasiyet, kontrol ve esneklik sunar. Derin sıvama işlemi, sac metalin kalıp içinde kontrollü bir şekilde akmasını ve kalıp formunu almasını sağlar. Bu süreçte malzemenin elastik ve plastik deformasyon sınırları dikkatlice yönetilir; böylece yırtılma, buruşma ya da malzeme kalınlığında istenmeyen incelmeler engellenir. Hidrolik sistemin sağladığı yumuşak ve sürekli kuvvet uygulaması, sac metalin kalıp içinde sorunsuz hareket etmesine olanak tanır.
Hidrolik derin sıvama presinin çalışma prensibi, hidrolik sıvının basınç yoluyla büyük kuvvetleri kontrollü şekilde aktarmasıdır. Bu prensip, özellikle karmaşık geometrilere sahip parçaların üretilmesinde kritik bir avantaj sağlar. Sac malzeme, blank holder adı verilen tutucu yardımıyla kalıp içinde sabitlenirken, hidrolik piston kontrollü basınç uygular ve sacın kalıp içine akışı sağlanır. Bu sayede, parçanın yüzey kalitesi yüksek olur ve üretim sırasında oluşabilecek kusurlar minimuma iner. Blank holder kuvveti ise malzemenin buruşmasını önlemek ve düzgün bir şekillendirme sağlamak için hassas şekilde ayarlanır.
Teknolojik gelişmeler, hidrolik derin sıvama preslerinin performansını ve kullanım alanlarını genişletmiştir. Günümüzde bu presler, yüksek hassasiyetli elektronik kontrol sistemleriyle donatılmıştır. Bu sayede basınç, hız, pozisyon gibi parametreler gerçek zamanlı olarak izlenir ve optimize edilir. Ayrıca, servo-hidrolik sistemler sayesinde enerji tüketimi azaltılırken, proses esnekliği artırılır. Bu gelişmeler, özellikle otomotiv ve beyaz eşya gibi sektörlerdeki üretim taleplerinin artmasıyla önem kazanmıştır. Çünkü bu sektörlerde üretilen parçalar hem karmaşık geometrik yapılara sahiptir hem de yüksek üretim hızları ve kalite standartları gerektirir.
Hidrolik derin sıvama presleri, otomotiv endüstrisinde kaporta parçalarının üretiminde kritik bir rol oynar. Araçların dış yüzeyleri ve yapısal elemanları, bu presler sayesinde dayanıklı ve estetik şekilde şekillendirilir. Aynı zamanda beyaz eşya sektöründe buzdolabı kapakları, çamaşır makinesi panelleri ve benzeri büyük sac parçaların üretiminde kullanılır. Aydınlatma sektöründe ise karmaşık şekilli metal reflektörler ve kaplamalar hidrolik derin sıvama ile üretilir. Havacılık ve savunma sanayinde, yüksek mukavemet ve hassasiyet gerektiren metal bileşenlerin üretimi için bu presler vazgeçilmezdir. Bu alanlarda kullanılan malzemeler genellikle özel alaşımlar olup, şekillendirme sırasında malzemenin yapısal bütünlüğünün korunması hayati öneme sahiptir.
Üretim süreçlerinde hidrolik derin sıvama preslerinin kullanımı, kalite kontrolü ve iş güvenliği açısından da önemli katkılar sağlar. Operatörlerin eğitimli olması, makinenin doğru ve güvenli kullanılmasını temin eder. Düzenli bakım programları ise presin performansını ve kalıp ömrünü artırır. Hidrolik sistemdeki yağ seviyelerinin ve filtrelerin düzenli kontrolü, aşınma durumlarının takibi gibi işlemler arızaların önüne geçer ve üretim sürekliliğini sağlar. Modern preslerde bulunan sensörler, anlık performans verileri sağlayarak bakım ihtiyaçlarını önceden belirlemeye yardımcı olur.
Enerji verimliliği, günümüzde hidrolik derin sıvama preslerinde öncelikli konulardan biridir. Servo motor destekli hidrolik pompalar ve değişken debili sistemler, enerji tüketimini optimize eder. Bu da hem işletme maliyetlerini düşürür hem de çevresel sürdürülebilirliğe katkıda bulunur. Ayrıca, makine tasarımlarındaki gelişmelerle birlikte, preslerin boyutları küçülürken güç kapasiteleri artırılmaktadır. Bu sayede daha az alan kaplayan, ancak daha yüksek performans sunan makineler üretilebilmektedir.
Gelecekte hidrolik derin sıvama preslerinin dijitalleşme ve otomasyon ile entegrasyonunun artması beklenmektedir. Yapay zeka ve makine öğrenimi algoritmaları, proseslerin optimize edilmesinde ve üretim kalitesinin artırılmasında etkin rol oynayacaktır. Sensörlerden toplanan verilerin analiziyle, proses parametreleri gerçek zamanlı olarak ayarlanacak, böylece ürün kalitesi en üst seviyeye çıkarılacaktır. Ayrıca artırılmış gerçeklik ve sanal gerçeklik destekli eğitimlerle, operatörlerin makineleri daha etkin ve güvenli kullanmaları sağlanacaktır.
Sonuç olarak, hidrolik derin sıvama presi; hassasiyet, güç, esneklik ve verimlilik gibi özellikleri bir arada sunarak metal şekillendirme süreçlerinin vazgeçilmez bir parçası haline gelmiştir. Teknolojik gelişmelerle birlikte makineler daha akıllı, enerji tasarruflu ve kullanıcı dostu hale gelirken, endüstrinin değişen ihtiyaçlarına cevap verme kapasitesi her geçen gün artmaktadır. Bu sayede, hidrolik derin sıvama presleri, modern üretim tesislerinin temel taşlarından biri olmaya devam edecektir.
Hidrolik derin sıvama presleri, metal şekillendirme teknolojisinin en karmaşık ve hassas uygulamalarından biri olan derin sıvama işlemini gerçekleştirmek için özel olarak tasarlanmıştır. Bu makineler, ince sacların kalıp içinde kontrollü bir biçimde şekillendirilmesini sağlayarak, yüksek kaliteli, karmaşık geometrilere sahip metal parçaların üretimini mümkün kılar. Derin sıvama işlemi, özellikle otomotiv, beyaz eşya, havacılık ve medikal sektörlerde büyük önem taşır. Çünkü bu sektörlerde kullanılan parçalar, yüksek dayanıklılık ve mükemmel yüzey kalitesi gerektirir. Hidrolik derin sıvama presleri, bu beklentileri karşılayabilmek için hem kuvvet hem de hassasiyet açısından üstün performans sergiler.
Bu preslerin çalışma prensibi, hidrolik sistemin sağladığı yüksek basıncın sac malzemeye yumuşak ve eşit olarak uygulanmasıdır. Sac, kalıp boşluğuna yerleştirildikten sonra, blank holder yardımıyla kenarları sabitlenir ve buruşma engellenir. Ardından hidrolik piston yavaşça ve kontrollü şekilde hareket ederek sacı kalıp içine doğru iter. Bu süreçte basınç ve hareket hızı titizlikle kontrol edilir; böylece malzemenin plastik deformasyon sınırları aşılmadan, malzemenin kalıp içinde düzgün bir şekilde akması sağlanır. Böylece malzeme üzerinde çatlama, buruşma veya aşırı incelme gibi kusurlar oluşmaz.
Teknolojik gelişmelerle birlikte hidrolik derin sıvama presleri, çok daha gelişmiş kontrol sistemleriyle donatılmıştır. Elektronik sensörler sayesinde basınç, hız ve pozisyon parametreleri anlık olarak izlenir ve otomatik olarak optimize edilir. Servo hidrolik sistemler, enerji tasarrufu sağlayarak işletme maliyetlerini düşürürken, üretim esnekliğini artırır. Aynı zamanda, proses verilerinin dijital ortamda toplanması ve analiz edilmesi, kalite kontrol ve önleyici bakım süreçlerinin etkinliğini artırır.
Endüstride hidrolik derin sıvama presleri çok çeşitli uygulamalara sahiptir. Otomotiv sektöründe, kaporta parçaları, yakıt tankları ve iç dizayn elemanları gibi çok sayıda bileşenin üretiminde kullanılır. Beyaz eşya sektöründe ise buzdolabı, çamaşır makinesi ve fırın gibi ürünlerin metal kapakları ve iç kısımları bu preslerle şekillendirilir. Havacılık ve savunma sanayinde yüksek mukavemet gerektiren parçaların üretiminde tercih edilirken, medikal sektörde hassas metal bileşenlerin üretiminde kullanılır. Ayrıca aydınlatma sektörü gibi estetik ve dayanıklılığın bir arada olması gereken alanlarda da hidrolik derin sıvama presleri önemli rol oynar.
Bu preslerin verimli ve güvenli çalışması için operatörlerin kapsamlı eğitim alması şarttır. Operatörler, makinenin çalışma prensiplerini, güvenlik önlemlerini ve acil durum prosedürlerini iyi bilmelidir. İş sağlığı ve güvenliği standartlarına uygun çalışma ortamı oluşturulmalı, koruyucu ekipmanların kullanımı zorunlu hale getirilmelidir. Ayrıca, hidrolik sistemin yağ seviyesi, filtreler ve mekanik parçaların düzenli bakımı yapılmalıdır. Bu bakım süreçleri, presin ömrünü uzatır, arızaları önler ve üretimin sürekliliğini sağlar.
Enerji verimliliği ve çevresel sürdürülebilirlik günümüzde hidrolik derin sıvama preslerinde öncelikli konular arasındadır. Servo-hidrolik sistemler ve değişken debili pompalar kullanılarak enerji tüketimi minimize edilir. Aynı zamanda, hidrolik yağların çevre dostu olanları tercih edilir ve atık yağ yönetimi titizlikle uygulanır. Bu gelişmeler, işletmelerin hem maliyetlerini düşürmelerini sağlar hem de çevre üzerindeki olumsuz etkileri azaltır.
Geleceğe yönelik olarak hidrolik derin sıvama preslerinde yapay zeka ve makine öğrenimi uygulamalarının yaygınlaşması beklenmektedir. Bu teknolojiler, üretim verilerini analiz ederek proses optimizasyonu yapacak, bakım gereksinimlerini önceden tahmin edecek ve hata oranlarını minimize edecektir. Ayrıca, artırılmış gerçeklik ve sanal gerçeklik destekli eğitim platformları, operatörlerin makineleri daha etkin ve güvenli kullanmalarını sağlayacaktır.
Sonuç olarak, hidrolik derin sıvama presleri, modern endüstrinin yüksek hassasiyet ve kalite taleplerini karşılayan, güçlü ve esnek makineler olarak öne çıkar. Teknolojik yenilikler ve otomasyon sistemleriyle desteklenen bu presler, üretim verimliliğini artırırken, enerji tasarrufu ve çevresel sürdürülebilirlik hedeflerine de katkıda bulunur. Böylece, hidrolik derin sıvama presleri, geleceğin akıllı üretim tesislerinin temel unsurlarından biri olmaya devam edecektir.
Hidrolik derin sıvama preslerinin endüstriyel uygulamalarda giderek artan önemi, hem üretim teknolojilerinin gelişmesi hem de ürün kalitesi ve çeşitliliği taleplerinin yükselmesiyle doğrudan ilişkilidir. Günümüz sanayisinde, özellikle otomotiv, beyaz eşya, havacılık, savunma ve medikal gibi sektörlerde kullanılan metal parçalar, önceki yıllara kıyasla çok daha karmaşık, ince ve hassas olmaktadır. Bu da üretim süreçlerinde kullanılan ekipmanlardan yüksek performans, hassasiyet ve esneklik beklentisini artırmaktadır. Hidrolik derin sıvama presleri, sundukları yumuşak ve kontrollü kuvvet uygulaması sayesinde, bu beklentileri karşılayabilecek en uygun makinelerdir.
Derin sıvama işlemi, sac metalin kalıp içine derinlemesine ve formuna uygun şekilde akışını sağlamak üzere geliştirilmiş bir şekillendirme yöntemidir. Bu süreçte malzemenin hem elastik hem de plastik deformasyon sınırları dikkatle yönetilir. Hidrolik derin sıvama presleri, bu hassas kontrolü sağlamak için yüksek performanslı hidrolik sistemler, gelişmiş elektronik kontrol birimleri ve sensörlerle donatılmıştır. Piston hareketleri, basınç ve hız parametreleri en ince detayına kadar ayarlanabilir; böylece malzeme üzerinde çatlak, buruşma ya da kalınlıkta aşırı incelme gibi olumsuzluklar engellenir.
Teknolojinin ilerlemesiyle birlikte, bu preslerde kullanılan servo-hidrolik sistemler enerji tüketimini optimize ederken, süreçlerin esnekliğini de artırmaktadır. Servo motorlar, hidrolik pompaların ihtiyaca göre değişken debide çalışmasını sağlayarak hem enerji tasarrufu sağlar hem de daha hassas hareket kontrolü sunar. Bunun yanı sıra, proses sırasında elde edilen verilerin dijital ortamda toplanması ve yapay zeka destekli analizlerle değerlendirilmesi, üretim kalitesinin sürekli iyileştirilmesine imkan tanır. Böylece operatör müdahalesine gerek kalmadan otomatik ayarlamalar yapılabilir, bu da üretim verimliliğini ve ürün tutarlılığını artırır.
Hidrolik derin sıvama preslerinin endüstrideki geniş uygulama alanları, bu makinelerin ne kadar çok yönlü olduğunu gösterir. Otomotiv sektöründe motor kapakları, yakıt depoları, iç ve dış kaportalar gibi parçaların üretiminde önemli yer tutar. Bu parçaların dayanıklılığı, hafifliği ve estetik görünümü, preslerin hassas şekillendirme kabiliyetleri sayesinde mümkün olur. Beyaz eşya sektöründe ise soğutucu kapakları, çamaşır makinesi tamburları ve benzeri sac bileşenler hidrolik derin sıvama ile şekillendirilir. Havacılık ve savunma sanayinde ise daha yüksek standartlarda, genellikle alüminyum ve titanyum gibi alaşımlarla çalışılır ve bu alaşımların form verilirken mekanik özelliklerinin korunması preslerin kritik önemini artırır. Ayrıca medikal sektördeki implantlar ve hassas ekipmanlar da hidrolik derin sıvama presleri sayesinde üretilebilir.
İş güvenliği, operatör eğitimi ve bakım süreçleri, hidrolik derin sıvama preslerinin sağlıklı ve verimli kullanımı açısından hayati önem taşır. Operatörlerin makinenin çalışma prensiplerini ve güvenlik donanımlarını iyi bilmeleri gerekir. Ayrıca makinelerde acil durdurma butonları, koruyucu bariyerler ve sensörler gibi güvenlik önlemleri eksiksiz bulunmalıdır. Düzenli bakım programları kapsamında hidrolik yağının kontrolü, filtre temizliği, mekanik parçaların yağlanması ve kalıp yüzeylerinin bakımı gibi işlemler düzenli olarak yapılmalıdır. Bu uygulamalar, presin ömrünü uzatır, arızaları minimize eder ve üretim sürekliliğini sağlar.
Enerji verimliliği ve çevresel sürdürülebilirlik alanında da hidrolik derin sıvama presleri önemli gelişmeler göstermektedir. Yeni nesil servo-hidrolik sistemler, ihtiyaç dışı enerji tüketimini azaltarak işletme maliyetlerini düşürür. Ayrıca çevre dostu hidrolik yağların kullanımı ve atık yönetimiyle, makine çalışırken çevresel etkiler minimize edilir. Bu durum, özellikle günümüzün sürdürülebilir üretim ve çevre duyarlılığı odaklı yaklaşımına uyum sağlar.
Gelecekte hidrolik derin sıvama preslerinin dijitalleşme ve otomasyon entegrasyonunun daha da artması beklenmektedir. Makine öğrenimi algoritmaları, üretim parametrelerini optimize ederek ürün kalitesini üst seviyeye çıkaracak; sensörlerden alınan verilerle bakım ihtiyaçları önceden tespit edilerek arızalar önlenecektir. Ayrıca, artırılmış gerçeklik ve sanal gerçeklik teknolojileri, operatör eğitimlerinde kullanılacak ve makinelerin daha etkin, hızlı ve güvenli çalışmasını destekleyecektir. Bu gelişmeler, üretim hatlarının daha esnek, hızlı ve yüksek kaliteli ürünler ortaya koymasını sağlayacak.
Özetle, hidrolik derin sıvama presleri, yüksek kuvvet ve hassasiyet gerektiren metal şekillendirme işlemlerinde vazgeçilmez makinelerdir. Sağladıkları esneklik, enerji verimliliği ve gelişmiş kontrol imkanları ile endüstrideki yerleri giderek güçlenmektedir. Teknolojik yeniliklerle birlikte, bu presler modern üretim tesislerinin kalbinde yer alarak, sektörlerin gelişimine önemli katkılar sunmaya devam edecektir.
Hidrolik Yatay Pres
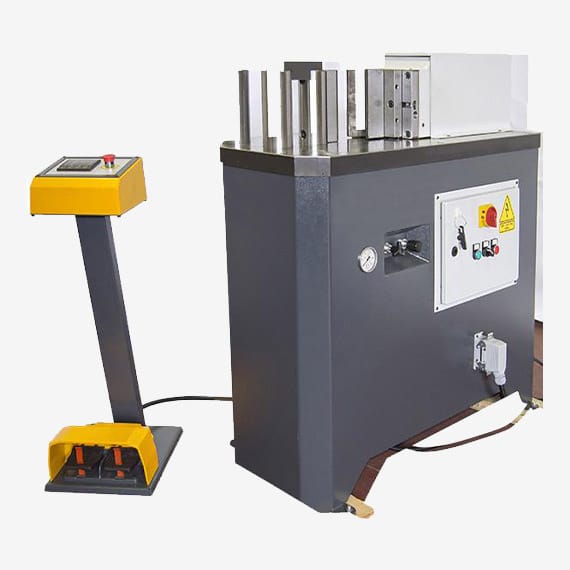
Hidrolik yatay pres, genellikle sac metal işleme, kalıplama, presleme, şekillendirme ve montaj işlemlerinde kullanılan, kuvvet uygulamasını yatay eksende gerçekleştiren bir hidrolik pres türüdür. Bu presler, özellikle büyük ve uzun parçaların işlenmesi gerektiğinde, yatay düzlemde kuvvet uygulama avantajı sunar. Hidrolik sistem sayesinde yüksek kuvvetler hassas ve kontrollü bir biçimde uygulanabilir. Yatay presler, endüstride çeşitli uygulamalarda yaygın olarak kullanılır ve esnek tasarımları sayesinde birçok farklı üretim sürecine uyarlanabilir.
Hidrolik yatay preslerin temel çalışma prensibi, basınçlı hidrolik sıvının piston ve silindirler aracılığıyla kuvvet oluşturmasıdır. Sistem, sıvının basınç altında hareket ettirilmesiyle, yatay eksende hareket eden pistonun kuvvetli bir şekilde iş parçasına etki etmesini sağlar. Bu kuvvet, sac metalin kesilmesi, bükülmesi, şekillendirilmesi veya montaj işlemlerinde kullanılır. Yatay preslerde, piston hareketinin yatay olması, özellikle uzun ve ince iş parçalarında daha kolay ve dengeli işlem yapılmasını sağlar. Bu sayede malzeme üzerinde deformasyon daha kontrollü gerçekleşir.
Endüstride hidrolik yatay presler, otomotiv sektörü, beyaz eşya üretimi, mobilya, elektronik, ambalaj ve metal işleme alanlarında yaygın olarak kullanılır. Örneğin, otomotiv sektöründe motor ve şasi parçalarının montajı, beyaz eşyada metal parçaların şekillendirilmesi ve elektronik sektörde hassas montaj işlemleri bu presler yardımıyla gerçekleştirilir. Ayrıca kalıplama ve kesme işlemlerinde yatay preslerin sağlamış olduğu kuvvet ve hareket avantajı sayesinde yüksek hassasiyet elde edilir.
Teknolojik gelişmelerle birlikte hidrolik yatay presler, gelişmiş elektronik kontrol sistemleriyle donatılmıştır. Bu sistemler, basınç, hız ve piston pozisyonunun hassas şekilde ayarlanmasını sağlar. Otomasyon ve robotik entegrasyonlarla birlikte, üretim hatlarında yüksek verimlilik ve tekrarlanabilirlik elde edilir. Ayrıca enerji verimliliği sağlayan servo-hidrolik sistemler sayesinde işletme maliyetleri azaltılır.
Güvenlik açısından, hidrolik yatay preslerde operatörlerin korunması için çeşitli önlemler alınmıştır. Acil durdurma sistemleri, koruyucu kapaklar ve sensörler, iş güvenliğini artırmak üzere standart olarak bulunur. Operatörlerin presin çalışma prensipleri ve güvenlik önlemleri konusunda kapsamlı eğitim almaları gerekir. Ayrıca düzenli bakım ve kontrol programları, presin uzun ömürlü ve sorunsuz çalışmasını sağlar.
Hidrolik yatay presler, endüstriyel üretim süreçlerinde esneklik, yüksek kuvvet ve hassasiyet gerektiren işlemler için ideal çözümler sunar. Yatay eksende kuvvet uygulama özelliği sayesinde, büyük boyutlu ve karmaşık parçaların işlenmesini mümkün kılar. Gelişen teknoloji ve otomasyon entegrasyonları ile birlikte, hidrolik yatay presler gelecekte de üretim tesislerinin vazgeçilmez makineleri arasında yer almaya devam edecektir.
Hidrolik yatay presler, endüstriyel üretim süreçlerinde önemli bir yer tutan, yüksek kuvvet uygulayabilen ve yatay eksende çalışan makineler olarak dikkat çeker. Bu makineler, özellikle uzun, geniş ve karmaşık iş parçalarının şekillendirilmesi, montajı, kesimi veya preslenmesi gibi işlemlerde tercih edilir. Hidrolik sistemin sağladığı yüksek basınç ve kontrollü hareket kabiliyeti sayesinde, hidrolik yatay presler hem dayanıklı hem de hassas üretim süreçlerine olanak tanır. Bu özellikleriyle otomotiv, beyaz eşya, metal işleme, mobilya, elektronik ve daha pek çok sektörde yaygın olarak kullanılır.
Hidrolik yatay preslerin çalışma prensibi, kapalı bir hidrolik sistemde basınçlı sıvının piston veya silindir yardımıyla yatay eksende kuvvet uygulamasına dayanır. Hidrolik sıvı, pompa aracılığıyla yüksek basınca ulaşır ve bu basınç, silindir içinde bulunan pistonun hareketini sağlar. Pistonun yatay doğrultuda iş parçasına uyguladığı kuvvet, metalin veya işlenen malzemenin deformasyonunu gerçekleştirir. Bu mekanizma, hem yüksek kuvvet uygulanmasını hem de hareketin hassas şekilde kontrol edilmesini mümkün kılar. Ayrıca hidrolik sistemlerin esnekliği, kuvvetin ayarlanabilmesi ve hızlı duruş gibi özellikler, üretim kalitesini artırır.
Hidrolik yatay preslerin kullanım alanları oldukça geniştir. Otomotiv sektöründe, motor ve şasi parçalarının montajı, kaporta işçiliği ve diğer metal şekillendirme işlemlerinde önemli rol oynar. Beyaz eşya üretiminde ise buzdolabı kapakları, çamaşır makinesi parçaları gibi geniş sac malzemelerin şekillendirilmesinde kullanılır. Elektronik sektöründe hassas montaj ve şekillendirme uygulamalarına imkan verirken, mobilya sektöründe metal aksamların preslenmesi ve montajı için tercih edilir. Ayrıca ambalaj sanayinde metal kutu üretiminde ve metal işleme atölyelerinde kesme, bükme, delme gibi işlemlerde de yaygın olarak kullanılır.
Teknolojik açıdan hidrolik yatay presler, gelişmiş elektronik kontrol sistemleri ve otomasyon teknolojileriyle desteklenmektedir. Günümüz makinelerinde basınç, piston hızı, hareket mesafesi ve kuvvet gibi parametreler elektronik sensörler sayesinde sürekli izlenir ve gerektiğinde otomatik olarak ayarlanır. Bu özellik, üretim süreçlerinin daha stabil, tekrarlanabilir ve yüksek kaliteli olmasını sağlar. Ayrıca, servo motor teknolojisinin entegrasyonu ile enerji tüketimi optimize edilir, gereksiz enerji harcamalarının önüne geçilir. Böylelikle hem maliyetler düşer hem de çevresel sürdürülebilirlik hedeflerine katkı sağlanır.
Güvenlik ve işçi sağlığı, hidrolik yatay preslerde öncelikli konulardandır. Yüksek kuvvetlerin kullanıldığı bu makinelerde, operatörlerin korunması için birçok önlem alınır. Acil durdurma butonları, güvenlik bariyerleri, ışık perdeleri ve sensörler sayesinde olası kazalar engellenir. Operatörlerin makineyi güvenli ve verimli kullanabilmesi için kapsamlı eğitim programları uygulanır. Ayrıca makinelerin düzenli bakımı, hidrolik yağlarının kontrolü ve mekanik parçaların periyodik olarak yağlanması, makinenin sorunsuz çalışmasını sağlar ve arızaların önüne geçer.
Hidrolik yatay preslerin avantajlarından biri de yüksek esneklik ve uyarlanabilirlik sunmasıdır. Pres üzerindeki kuvvet, hareket hızı ve piston strok mesafesi, iş parçasının türüne ve işlem gereksinimlerine göre kolayca ayarlanabilir. Bu sayede aynı makine farklı ürünler için kullanılabilir ve üretim hatlarında hızlı değişiklikler yapılabilir. Ayrıca, otomasyon sistemleri ile entegre edildiğinde, otomatik malzeme besleme ve çıkarma sistemleri sayesinde üretim hızları artırılır, işçilik maliyetleri düşürülür.
Enerji verimliliği açısından, modern hidrolik yatay preslerde servo-hidrolik sistemler yaygınlaşmıştır. Bu sistemler, enerji tüketimini ihtiyaç duyulan seviyeye göre ayarlayarak gereksiz harcamaların önüne geçer. Ayrıca bu makineler, çevre dostu hidrolik yağları kullanabilir ve atık yönetimi süreçlerine uygun şekilde tasarlanabilir. Bu gelişmeler, sürdürülebilir üretim anlayışını benimseyen işletmeler için önemli bir avantajdır.
Gelecekte hidrolik yatay preslerin dijitalleşme ve yapay zeka teknolojileri ile daha da akıllı hale gelmesi beklenmektedir. Sensörler ve veri analiz sistemleri sayesinde prosesler daha verimli yönetilecek, bakım ihtiyaçları önceden tahmin edilerek arıza riski minimize edilecektir. Ayrıca, artırılmış gerçeklik destekli operatör eğitimleri, makine kullanımını daha güvenli ve etkin hale getirecektir. Bu sayede hidrolik yatay presler, üretim tesislerinin olmazsa olmazı olarak kalmaya devam edecektir.
Sonuç olarak, hidrolik yatay presler yüksek kuvvet, esneklik ve hassasiyet gerektiren işlemlerde endüstriyel üretimin temel makineleri arasında yer alır. Sağladıkları kontrol, otomasyon ve enerji verimliliği avantajları ile farklı sektörlerde geniş uygulama alanına sahiptir. Teknolojideki yeniliklerle beraber, bu makinelerin performansı ve kullanım kolaylığı artmaya devam edecek, modern sanayinin önemli bir parçası olarak konumlarını güçlendireceklerdir.
Hidroform Presi
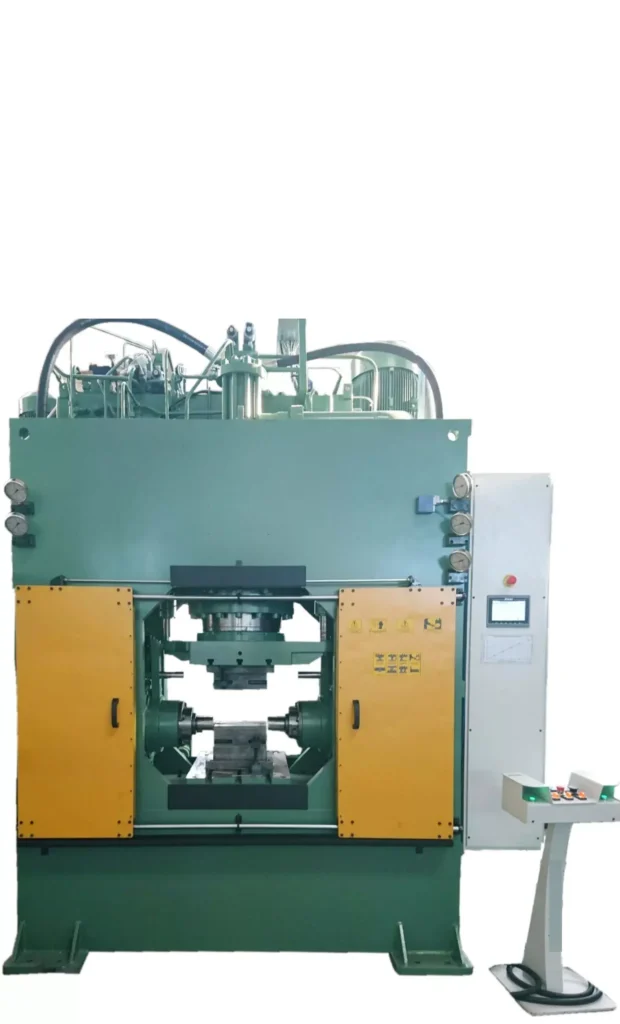
Hidroform presi, metal şekillendirme teknolojileri arasında özel bir yere sahip olan ve özellikle karmaşık, hafif ve dayanıklı metal parçaların üretiminde kullanılan ileri bir şekillendirme makinesidir. Adını “hidroform” yani “sıvı ile şekillendirme” prensibinden alır. Bu pres tipi, metal boru, profil veya ince sacların yüksek basınçlı sıvı yardımıyla kalıp içine doğru şekillendirilmesini sağlar. Hidroform işlemi, özellikle otomotiv, havacılık, bisiklet ve mobilya gibi sektörlerde karmaşık ve hafif yapısal parçaların üretiminde tercih edilir.
Hidroform presinin çalışma prensibi, iç basıncın sıvı aracılığıyla malzemeye uygulanmasıdır. İşlem genellikle kapalı bir kalıp sistemi içinde gerçekleştirilir. Metal boru veya profil, kalıp boşluğuna yerleştirilir ve iç kısmı yüksek basınçlı hidrolik sıvı ile doldurulur. Bu yüksek basınç, malzemenin kalıp yüzeyine doğru genişlemesini sağlar. Bu şekilde malzeme, kalıbın şekline tam olarak uyacak biçimde şekillenir. Bu yöntem, geleneksel mekanik presleme tekniklerine göre çok daha karmaşık ve hassas formlar elde edilmesine imkan verirken, malzemenin dayanıklılığını da artırır.
Hidroform preslerinin en önemli avantajlarından biri, malzemenin şekillendirilirken kesintisiz bir basınç uygulanması sayesinde gerilme dağılımının homojen olmasıdır. Bu durum, ürünlerde çatlama, buruşma veya malzeme zayıflaması gibi sorunların önüne geçer. Ayrıca, hidroform sayesinde daha ince malzemelerle daha dayanıklı parçalar üretmek mümkün olur. Bu da ağırlık tasarrufu gerektiren uygulamalarda özellikle önemlidir. Otomotiv sektöründe, aracın hafifletilmesi yakıt verimliliği ve performans açısından büyük avantaj sağlar.
Endüstride hidroform presleri, motor bileşenleri, şasi parçaları, egzoz sistemleri, bisiklet çerçeveleri, mobilya bağlantı elemanları ve havacılık parçaları gibi birçok alanda kullanılır. Bu presler sayesinde karmaşık, eğimli ve içi boş yapılar yüksek hassasiyetle üretilebilir. Ayrıca, hidroform işlemi sayesinde kaynak ve montaj gibi ekstra işlemlere olan ihtiyaç azalır; böylece üretim süresi kısalır ve maliyetler düşer.
Teknolojik açıdan hidroform preslerinde yüksek basınç üreten hidrolik sistemler ve basınç kontrol üniteleri kritik öneme sahiptir. Basınç, sıcaklık ve akış hızı gibi parametreler elektronik olarak sürekli izlenir ve optimize edilir. Bu sayede üretim sürecinin stabilitesi ve tekrarlanabilirliği sağlanır. Ayrıca, modern hidroform preslerinde kullanılan otomasyon sistemleri, üretim hızını artırırken iş güvenliğini de üst seviyeye çıkarır.
Hidroform preslerinin bakımı, doğru yağ seviyelerinin korunması, hidrolik sistemlerin temizliği ve kalıp yüzeylerinin düzenli kontrolü gibi işlemleri içerir. Bu bakımlar, presin uzun ömürlü ve yüksek performansla çalışmasını sağlar. Ayrıca, operatörlerin işlem prensipleri, güvenlik protokolleri ve acil durum müdahaleleri konusunda iyi eğitilmesi, üretim kalitesi ve iş güvenliği açısından büyük önem taşır.
Enerji verimliliği açısından, servo-hidrolik sistemlerin kullanılması hidroform preslerinde giderek yaygınlaşmaktadır. Bu sistemler, ihtiyaç duyulan basınç ve debiyi hassas şekilde ayarlayarak enerji tüketimini azaltır. Ayrıca çevre dostu hidrolik yağlar ve atık yönetim sistemleri kullanılarak üretimin çevresel etkileri minimize edilir.
Gelecekte hidroform preslerinde dijitalleşme, yapay zeka ve makine öğrenimi uygulamalarının daha fazla yer alması beklenmektedir. Bu teknolojiler, üretim verilerini analiz ederek proses optimizasyonu, bakım tahmini ve kalite kontrolü gibi alanlarda önemli katkılar sağlayacaktır. Ayrıca artırılmış gerçeklik destekli operatör eğitimleri ile makinelerin daha verimli ve güvenli kullanımı sağlanacaktır.
Sonuç olarak, hidroform presleri, karmaşık ve hafif metal parçaların üretiminde sunduğu yüksek hassasiyet, esneklik ve dayanıklılık ile modern endüstride vazgeçilmez bir rol oynar. Teknolojik gelişmeler ve otomasyon entegrasyonları sayesinde üretim kalitesi ve verimliliği sürekli artmakta, hidroform presleri geleceğin akıllı üretim tesislerinin temel ekipmanlarından biri olmaya devam etmektedir.
Hidroform presleri, metal şekillendirme teknolojileri içerisinde kendine özgü çalışma prensibi ve sunduğu avantajlarla ön plana çıkan ileri üretim makineleridir. Temelde, metal boru, profil veya ince sacların yüksek basınçlı hidrolik sıvı kullanılarak kalıp içine doğru şekillendirilmesini sağlayan bu presler, özellikle karmaşık geometriler ve hafif ama dayanıklı parçalar üretmek isteyen sanayi kolları için kritik önem taşır. Hidroform teknolojisi, metalin içten basınçla şekillendirilmesi prensibine dayanır ve bu sayede malzemeye dışarıdan mekanik kuvvet uygulanmadan, kontrollü ve homojen deformasyon sağlanır. Bu mekanizma, geleneksel presleme ve bükme yöntemlerine kıyasla hem üretim esnekliği hem de ürün kalitesi açısından önemli avantajlar sunar.
Hidroform preslerinin çalışma prensibini detaylandırmak gerekirse; işlem sırasında metal parça, genellikle kapalı iki parçalı kalıp içerisine yerleştirilir. İç kısmı boş olan boru veya profil, içinden yüksek basınçlı hidrolik sıvı geçirilerek basınç uygulanır. Bu yüksek basınç, metalin kalıp yüzeyine doğru genişlemesini sağlar ve kalıbın şekline tam uyumlu, pürüzsüz ve sağlam yapıda bir parça ortaya çıkar. Basınç kontrollü olduğu için malzeme üzerinde oluşan gerilmeler dengeli bir şekilde dağılır ve malzeme üzerinde çatlama, yırtılma veya buruşma gibi deformasyon kusurları minimize edilir. Bu yöntem, özellikle ince malzemelerin kullanılmasını mümkün kılarak hem malzeme tasarrufu sağlar hem de üretilen parçaların hafif ama dayanıklı olmasını mümkün kılar.
Hidroform pres teknolojisi, özellikle otomotiv sektöründe büyük rağbet görür. Çünkü araçlarda yakıt tasarrufu ve performans iyileştirmesi için ağırlığın azaltılması gerekir. Hidroform sayesinde araçların şasi parçaları, motor ve süspansiyon bileşenleri, egzoz sistemleri gibi kritik parçalar daha hafif, daha dayanıklı ve karmaşık geometrilerle üretilebilir. Bu teknoloji, parçaların işlevselliğini artırırken aynı zamanda montaj süreçlerini de kolaylaştırır. Örneğin, hidroform ile üretilen bir şasi parçası, geleneksel yöntemlerle üretilenlerden daha az kaynak ve ek parça gerektirir, bu da üretim süresini kısaltır ve maliyetleri düşürür.
Havacılık, savunma, bisiklet ve mobilya sektörleri de hidroform preslerinin yoğun şekilde kullanıldığı diğer alanlardır. Havacılıkta kullanılan parçalar yüksek mukavemet ve hafiflik gerektirirken, hidroform teknolojisi bu gereksinimleri karşılar. Savunma sanayinde dayanıklılık ve hassasiyet kritik olduğundan, hidroform presleri ile üretilen bileşenler yüksek standartlara uygundur. Bisiklet çerçeveleri ve mobilya bağlantı elemanları ise hem estetik hem de yapısal açıdan karmaşık tasarımları destekleyebilmesi nedeniyle hidroform presiyle şekillendirilir.
Teknolojik açıdan, hidroform preslerinde kullanılan hidrolik sistemlerin güvenilirliği ve performansı üretim kalitesini doğrudan etkiler. Yüksek basınçlı hidrolik pompalar, kontrol vanaları ve sensörler aracılığıyla sistemler hassas şekilde yönetilir. Günümüzde, gelişmiş elektronik kontrol üniteleri basınç, sıcaklık, akış hızı ve piston hareketini gerçek zamanlı izleyerek optimum proses koşullarını sağlar. Bu sayede, proses boyunca yüksek tutarlılık ve kalite elde edilir. Otomasyonun entegrasyonu ise üretim hızını ve tekrar edilebilirliği artırırken insan hatasını minimuma indirir.
Bakım ve operatör eğitimi de hidroform preslerinin verimli çalışmasında kritik rol oynar. Hidrolik sistemlerde yağ kalitesi, sızıntılar, filtre temizliği ve mekanik parçaların düzenli kontrolü, presin arızasız ve uzun ömürlü çalışmasını sağlar. Operatörler ise presin çalışma prensipleri, güvenlik tedbirleri ve acil durum prosedürleri konusunda detaylı eğitim almalıdır. Bu, iş güvenliği ve üretim kalitesi için hayati önem taşır.
Enerji verimliliği de günümüzde hidroform preslerinin tasarımında önemli bir kriterdir. Servo-hidrolik sistemlerin kullanılmasıyla enerji tüketimi optimize edilirken, çevre dostu hidrolik yağlar ve geri dönüşüm sistemleri sayesinde çevresel etkiler azaltılır. Bu yaklaşım, sürdürülebilir üretim hedeflerine uygun hareket eden firmalar için önemli bir rekabet avantajı sunar.
Gelecekte hidroform preslerinde dijitalleşmenin, yapay zeka ve makine öğrenimi teknolojilerinin daha fazla kullanılması beklenmektedir. Bu gelişmeler, proses kontrolünün daha hassas ve öngörülebilir olmasını sağlayacak; bakım faaliyetlerinin önceden planlanması ve hata oranlarının azaltılması mümkün olacaktır. Ayrıca artırılmış gerçeklik destekli operatör eğitimleri, makine kullanımını daha etkin ve güvenli hale getirecektir.
Özetle, hidroform presi metal şekillendirme alanında yüksek hassasiyet, dayanıklılık ve üretim esnekliği sunan bir teknolojidir. Hem ürün kalitesini hem de üretim verimliliğini artıran bu makineler, otomotivden havacılığa, mobilyadan savunmaya pek çok sektörde kritik bir rol üstlenmektedir. Teknolojinin gelişimiyle birlikte hidroform preslerinin önemi daha da artacak ve geleceğin üretim tesislerinin vazgeçilmez ekipmanlarından biri olmaya devam edecektir.
Hidroform presleri, metal şekillendirme teknolojilerinde hem üretim esnekliği hem de yüksek kalite standartlarını sağlamak amacıyla kullanılan ileri düzey makineler arasında yer alır. Bu presler, özellikle hafiflik, dayanıklılık ve karmaşık geometrik yapılar talep eden endüstriyel uygulamalarda tercih edilir. Günümüzün rekabetçi üretim ortamında, malzeme tasarrufu sağlamak ve üretim maliyetlerini düşürmek önemli hedefler arasında bulunurken, hidroform teknolojisi bu ihtiyaçlara etkin çözümler sunar. Hidroform presi ile üretim yapılan parçalar, geleneksel yöntemlerle üretilenlere kıyasla daha ince malzeme kullanımıyla aynı veya daha yüksek mukavemet değerlerine ulaşabilir. Bu durum, özellikle otomotiv ve havacılık sektörlerinde araç ve uçak ağırlığını azaltarak yakıt verimliliğini artırmak ve performansı yükseltmek için kritik önem taşır.
Hidroform işlemi, yüksek basınçlı sıvı kullanımı sayesinde malzemeye dıştan değil, içten basınç uygulanması prensibine dayanır. Bu iç basınç, metal boru, profil ya da ince sacın kalıp içerisinde kontrollü biçimde genişlemesini ve kalıbın şeklini almasını sağlar. Böylece malzemenin gerilme dağılımı homojenleşir ve yırtılma, çatlama gibi deformasyon riskleri minimize edilir. Bu teknik, geleneksel mekanik preslemeye kıyasla daha karmaşık ve hassas şekillerin üretilebilmesine olanak tanır. Ayrıca, işlem sırasında malzemenin yüzey kalitesi yüksek olur, bu da sonradan yapılacak yüzey işlemlerinin maliyetini ve süresini azaltır.
Hidroform preslerinin kullanıldığı endüstriyel alanlar oldukça geniştir. Otomotiv sektöründe motor ve süspansiyon parçaları, şasi bileşenleri, egzoz sistemleri ve yakıt tankları gibi kritik yapısal parçalar hidroform ile şekillendirilir. Bu parçaların hem hafif hem de dayanıklı olması, araçların performansını ve güvenliğini artırır. Havacılık sektöründe ise alüminyum ve titanyum alaşımları kullanılarak üretilen karmaşık yapısal bileşenlerde hidroform presleri vazgeçilmezdir. Bisiklet üretiminde, hafif ve dayanıklı çerçeveler hidroform sayesinde elde edilirken, mobilya sektöründe metal bağlantı elemanları ve dekoratif parçalar bu teknolojiyle üretilmektedir. Savunma sanayinde ise dayanıklılık ve hassasiyet ön planda olduğundan, hidroform presleri kritik bileşenlerin üretiminde kullanılır.
Teknolojik açıdan hidroform presleri, yüksek basınçlı hidrolik sistemlerin yanı sıra gelişmiş kontrol teknolojileri ile donatılmıştır. Elektronik sensörler ve otomasyon sistemleri, basınç, sıcaklık, sıvı akışı ve piston hareketlerini gerçek zamanlı izler ve ayarlar. Bu durum, prosesin tutarlı ve tekrarlanabilir olmasını sağlayarak ürün kalitesini artırır. Servo-hidrolik teknolojiler ise enerji verimliliğini üst düzeye çıkarır ve işletme maliyetlerini düşürür. Ayrıca, makinelerin otomatik besleme ve boşaltma sistemleri ile entegrasyonu üretim hatlarının hızını ve verimliliğini artırır.
Bakım açısından, hidroform preslerinin sağlıklı çalışması için hidrolik sistem yağlarının kalitesi ve seviyesinin düzenli kontrolü, filtrelerin temizliği, hidrolik hortum ve bağlantı noktalarının sızdırmazlıklarının denetlenmesi büyük önem taşır. Ayrıca kalıp yüzeylerinin düzenli olarak temizlenmesi ve mekanik hareketli parçaların yağlanması, presin uzun ömürlü olmasını sağlar. Operatörlerin kapsamlı eğitimi, makinenin verimli ve güvenli kullanımı açısından gereklidir. İş güvenliği kurallarına uygun hareket etmek, hem operatörlerin sağlığını korur hem de üretim sürecinde oluşabilecek hata ve kazaların önüne geçer.
Enerji verimliliği, çevresel sürdürülebilirlik ve maliyet optimizasyonu, günümüzde hidroform presleri tasarımında öncelikli konulardır. Servo-hidrolik sistemlerin kullanılması sayesinde presler, yalnızca ihtiyaç duyulan enerji miktarını kullanır ve böylece israf minimuma indirilir. Ayrıca, çevre dostu hidrolik yağları tercih edilir ve atıkların geri dönüşümü ile çevresel etkiler azaltılır. Bu gelişmeler, özellikle karbon ayak izini azaltmak isteyen üreticiler için önemli bir avantajdır.
Geleceğe baktığımızda, hidroform preslerinde dijitalleşme, yapay zeka ve makine öğrenimi entegrasyonunun artacağı öngörülmektedir. Bu teknolojiler, üretim süreçlerinin daha akıllı hale gelmesini sağlayarak kalite kontrol, proses optimizasyonu ve bakım tahmini gibi alanlarda büyük faydalar sunacaktır. Sensörlerden gelen verilerin analizi, proses parametrelerinin dinamik olarak ayarlanmasına imkan tanıyacak ve böylece üretim verimliliği ve ürün kalitesi üst seviyeye çıkacaktır. Ayrıca artırılmış gerçeklik ve sanal gerçeklik destekli eğitim platformları, operatörlerin makineleri daha etkin ve güvenli kullanmalarını destekleyecektir.
Sonuç olarak, hidroform presleri, metal şekillendirme alanında yüksek hassasiyet, dayanıklılık ve üretim esnekliği sunan, sektörlerin rekabet gücünü artıran kritik ekipmanlardır. Teknolojideki gelişmelerle birlikte bu makineler, enerji verimliliği, otomasyon ve dijitalleşme alanlarında sürekli yenilenerek, modern üretim tesislerinin temel yapıtaşları olmaya devam edecektir. Böylece hidroform presleri, sadece bugünün değil, geleceğin de metal şekillendirme çözümleri arasında önemli bir yer tutacaktır.
Hidroform presleri, modern metal şekillendirme teknolojilerinin en sofistike ve yenilikçi çözümlerinden biri olarak, özellikle karmaşık ve yüksek dayanıklılık gerektiren parçaların üretiminde tercih edilen makineler arasında başı çekmektedir. Geleneksel şekillendirme yöntemlerinden farklı olarak, hidroform teknolojisi, malzemenin iç kısmına uygulanan yüksek basınçlı sıvı sayesinde şekillendirme işleminin gerçekleştirilmesi esasına dayanır. Bu prensip, malzemenin homojen bir şekilde ve dıştan mekanik zorlamalar olmadan kalıp şekline uyum sağlamasını mümkün kılar. Dolayısıyla, hidroform presleri, sadece parça geometrisinde sağladığı esneklikle değil, aynı zamanda üretimde sağladığı kalite ve verimlilik avantajlarıyla da öne çıkar.
Teknolojik gelişmelerle birlikte, hidroform preslerinin hidrolik sistemleri son derece gelişmiş ve hassas kontrol üniteleri ile donatılmıştır. Yüksek basınçlı hidrolik sıvının kontrollü akışı, basınç ve sıcaklık sensörleri aracılığıyla gerçek zamanlı izlenmekte ve otomatik ayarlamalar yapılmaktadır. Bu durum, üretim sürecinde meydana gelebilecek sapmaların önüne geçerek, her bir parçanın standartlara uygun ve tekrar edilebilir şekilde üretilmesini sağlar. Özellikle üretim hatlarında kullanılan robotik sistemlerle entegrasyon, malzeme besleme, şekillendirme ve çıkarma süreçlerini otomatikleştirerek üretim hızını ve verimliliği önemli ölçüde artırır. Ayrıca enerji tüketimi de servo-hidrolik teknolojilerle optimize edilmekte, böylece işletme maliyetleri azaltılmakta ve çevresel sürdürülebilirlik hedeflerine katkıda bulunulmaktadır.
Hidroform presleri, özellikle otomotiv sanayinde araç performansını ve yakıt ekonomisini doğrudan etkileyen hafif ve dayanıklı parçaların üretiminde kritik rol oynar. Bu teknoloji ile üretilen şasi elemanları, motor parçaları, yakıt tankları ve egzoz sistemleri, aracın toplam ağırlığını azaltırken mukavemetini artırır. Bu durum hem performans hem de güvenlik açısından önemli avantajlar sağlar. Aynı zamanda, bu parçaların daha karmaşık geometrilerde ve daha az ek parça kullanılarak üretilmesi, montaj süreçlerini kolaylaştırır ve toplam üretim süresini kısaltır. Havacılık sektöründe ise hidroform presleri, alüminyum ve titanyum alaşımlarıyla üretilen hafif ve dayanıklı yapısal bileşenlerin elde edilmesinde vazgeçilmezdir. Bu sayede uçakların ağırlığı azalır, yakıt verimliliği artar ve uçuş performansı iyileşir.
Bisiklet üretimi ve mobilya sanayinde de hidroform preslerinin yeri büyüktür. Bisiklet çerçeveleri, hem dayanıklılığı artırmak hem de ağırlığı minimize etmek amacıyla hidroform yöntemiyle şekillendirilir. Mobilya sektöründe ise dekoratif ve yapısal metal parçaların karmaşık formlarda üretimi hidroform presleri sayesinde mümkün olur. Bu, tasarımda geniş bir yaratıcılık alanı açarken, ürünlerin estetik ve fonksiyonel özelliklerini artırır. Savunma sanayinde ise yüksek mukavemet ve hassasiyet gerektiren parçaların üretiminde hidroform teknolojisi kullanılır. Bu parçalar, zorlu çevre ve kullanım koşullarına dayanıklı olmak zorundadır ve hidroform presleri bu gereksinimleri karşılamak için ideal çözümler sunar.
Hidroform preslerinin bakım ve operatör eğitimi süreçleri de üretim kalitesinin sürdürülebilirliği açısından büyük önem taşır. Hidrolik sistemde kullanılan yağın kalitesi ve seviyesi düzenli olarak kontrol edilmeli, sızıntı ve aşınmalar erken tespit edilmelidir. Kalıp yüzeyleri temiz ve düzgün tutulmalı, mekanik hareketli parçalar düzenli olarak yağlanmalıdır. Operatörlerin, presin çalışma prensipleri, güvenlik standartları, acil durum prosedürleri ve makinelerin doğru kullanımı hakkında kapsamlı eğitimler almaları gerekir. Bu eğitimler, hem iş güvenliğini artırır hem de üretim sürecinde oluşabilecek hataları azaltır.
Enerji tasarrufu ve çevresel sürdürülebilirlik, hidroform preslerinin tasarımında öncelikli kriterler arasında yer almaktadır. Servo-hidrolik sistemlerin yaygınlaşması, makinelerin enerji kullanımını optimize ederken, çevre dostu hidrolik yağların tercih edilmesi ve atık yönetimi uygulamaları çevresel etkileri minimize eder. Bu sayede hidroform presleri, sadece ekonomik açıdan değil, aynı zamanda çevresel açıdan da sürdürülebilir üretim çözümleri sunar.
Gelecekte hidroform preslerinin dijital dönüşümünün hızlanması beklenmektedir. Yapay zeka ve makine öğrenimi algoritmaları, üretim verilerini analiz ederek proses optimizasyonu yapacak ve bakım ihtiyaçlarını önceden tahmin edecektir. Böylece arıza süreleri azalacak ve üretim hatlarının verimliliği artacaktır. Ayrıca artırılmış gerçeklik ve sanal gerçeklik teknolojileri, operatörlerin eğitiminde kullanılacak ve makinelerin daha güvenli ve etkin kullanılmasını sağlayacaktır. Bu gelişmeler, hidroform preslerinin daha akıllı, otomatik ve kullanıcı dostu makineler haline gelmesini sağlayarak modern üretim tesislerinin kalbinde yer almaya devam etmesini mümkün kılacaktır.
Sonuç olarak, hidroform presleri, metal şekillendirme sektöründe yüksek hassasiyet, dayanıklılık ve üretim verimliliği sağlayan kritik teknolojiler arasında yer almaktadır. Endüstriyel uygulamalardaki çeşitliliği, teknolojik gelişmelerle artan performansı ve sürdürülebilir üretim yaklaşımlarına uyumu ile hidroform presleri, geleceğin üretim süreçlerinin temel unsurlarından biri olmaya devam edecektir. Bu makineler, sektörlere rekabet avantajı sağlamakla kalmayıp, aynı zamanda çevresel etkileri azaltarak daha yeşil ve verimli üretim modellerinin gelişmesine öncülük etmektedir.
EMS Metal İşleme Makineleri
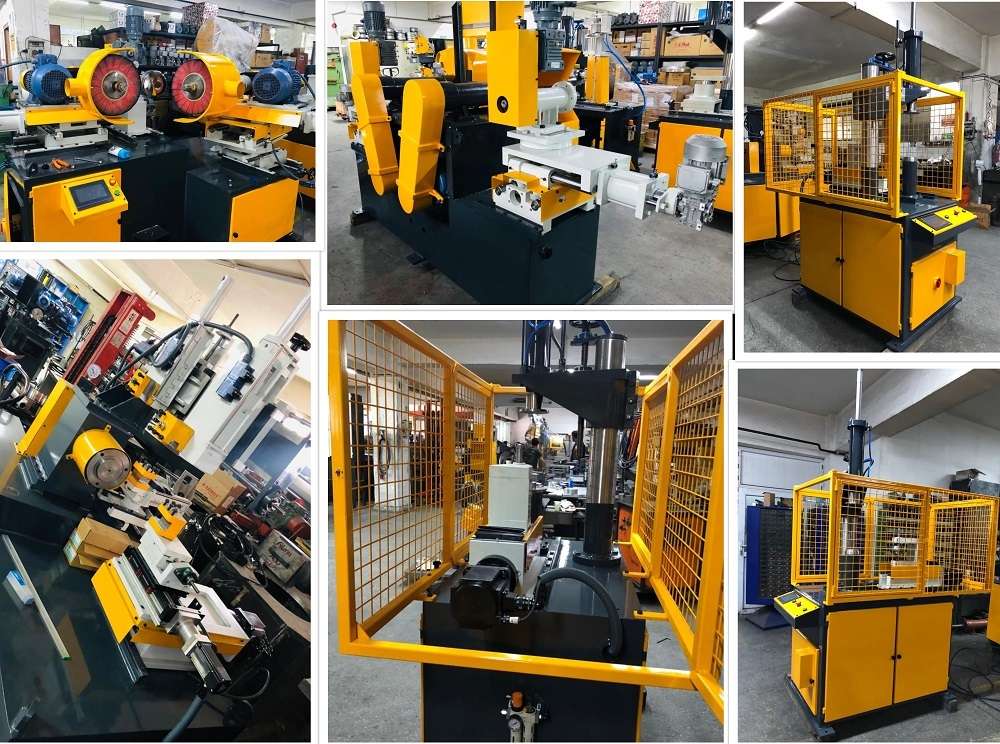
EMS Metal İşleme Makineleri olarak, endüstriyel üretim süreçlerinizi daha verimli, hassas ve kaliteli hale getirecek geniş bir makine yelpazesi sunmaktan gurur duyuyoruz. Üstün mühendislik ve ileri teknoloji ürünlerimizle, metal işleme endüstrisinin tüm ihtiyaçlarını karşılayacak çözümler sağlıyoruz. İşte sunduğumuz başlıca ürünler:
Hidrolik Transfer Presleri
Yüksek verimlilik ve otomasyon gerektiren büyük ölçekli üretim hatları için ideal olan hidrolik transfer preslerimiz, çok aşamalı işlemleri hızlı ve etkin bir şekilde gerçekleştirir. Yüksek hassasiyetli kontrol sistemleri sayesinde, ürün kalitesini artırır ve işçilik maliyetlerini düşürür.
Hidrolik Derin Sıvama Presleri
Metal levhaların karmaşık ve derin şekillendirme işlemlerini mükemmel bir hassasiyetle gerçekleştiren hidrolik derin sıvama preslerimiz, otomotiv, havacılık ve beyaz eşya gibi çeşitli endüstrilerde yüksek performans sunar. Yüksek basınç kapasitesi ile kalın ve sert metallerin işlenmesi için uygundur.
CNC Metal Sıvama (Spinning) Makineleri
Yüksek hassasiyetli CNC kontrollü metal sıvama makinelerimiz, ince metal levhaları döndürerek şekillendirmek için idealdir. Karmaşık geometriler ve hassas ölçüler için mükemmel çözümler sunar.
Etek Kesme Kordon Boğma Makineleri
Metal kapların alt eteklerinin kesilmesi ve kordon boğma işlemlerini yüksek hassasiyetle gerçekleştiren makinelerimiz, özellikle kapak ve kap üretiminde kalite ve verimlilik sağlar.
Kenar Kıvırma ve Kenar Kapama Makineleri
Metal parçaların kenarlarını kıvırma ve kapama işlemlerini gerçekleştiren makinelerimiz, düzgün ve dayanıklı kenar işlemleri sunar. Bu makineler, ambalaj, otomotiv ve beyaz eşya endüstrilerinde yaygın olarak kullanılır.
Boru ve Profil Bükme Makineleri
Farklı çap ve şekillerdeki boru ve profillerin hassas bir şekilde bükülmesini sağlayan makinelerimiz, inşaat, otomotiv ve mobilya sektörlerinde kullanılır. Güçlü yapıları ve hassas kontrol sistemleri ile yüksek kalite sağlar.
Silindirik Kaynak Makineleri
Silindirik parçaların mükemmel doğrulukla kaynaklanmasını sağlayan makinelerimiz, boru, tank ve diğer silindirik yapıların üretiminde yüksek kalite sunar.
Otomatik Mop Polisaj ve Zımpara Makineleri
Metal yüzeylerin pürüzsüz ve parlak hale getirilmesi için kullanılan otomatik mop polisaj ve zımpara makinelerimiz, çeşitli metal işleme sektörlerinde üstün yüzey kalitesi sağlar.
Daire Kesme Makineleri
Metal levhaların dairesel kesim işlemlerini hassas ve hızlı bir şekilde gerçekleştiren daire kesme makinelerimiz, yüksek üretim kapasitesi ve düşük hurda oranları ile öne çıkar.
EMS olarak, siz değerli müşterilerimize en ileri teknolojilerle donatılmış, dayanıklı ve verimli makineler sunmaktan memnuniyet duyarız. Ürünlerimiz ve hizmetlerimiz hakkında daha fazla bilgi almak için bizimle iletişime geçin. Sizlere en iyi çözümleri sunmak için buradayız.
Cıvata ve Akıllı Vida Kafası Boyama Makinesi
Modern endüstriyel üretim süreçlerinde, kalite kontrol ve verimlilik büyük önem taşır. Bu bağlamda, cıvata ve vida üretiminde, özellikle kafa boyama işlemi kritik bir adımdır. Cıvata ve akıllı vida kafası boyama makineleri, üretim hattında otomasyonu ve hassasiyeti sağlayarak bu işlemi optimize eder. Bu makineler, geleneksel yöntemlere göre birçok avantaj sunar ve endüstride devrim niteliğinde yenilikler getirir.